The effect of substrate temperature on film deposition processes, such as PVD (Physical Vapor Deposition) and CVD (Chemical Vapor Deposition), is significant and multifaceted. Substrate temperature influences the local state density, electron mobility, and optical properties of the film. Higher temperatures can compensate for suspended bonds on the film surface, thereby reducing defect density and improving film quality. While the precipitation rate is less affected by temperature, the denseness, surface reactions, and composition of the film are significantly enhanced at elevated temperatures. Plasma-assisted CVD can lower the required substrate temperature, offering a balance between process efficiency and film quality. Measurement techniques, such as infrared ratio thermometry, ensure precise temperature control during deposition.
Key Points Explained:
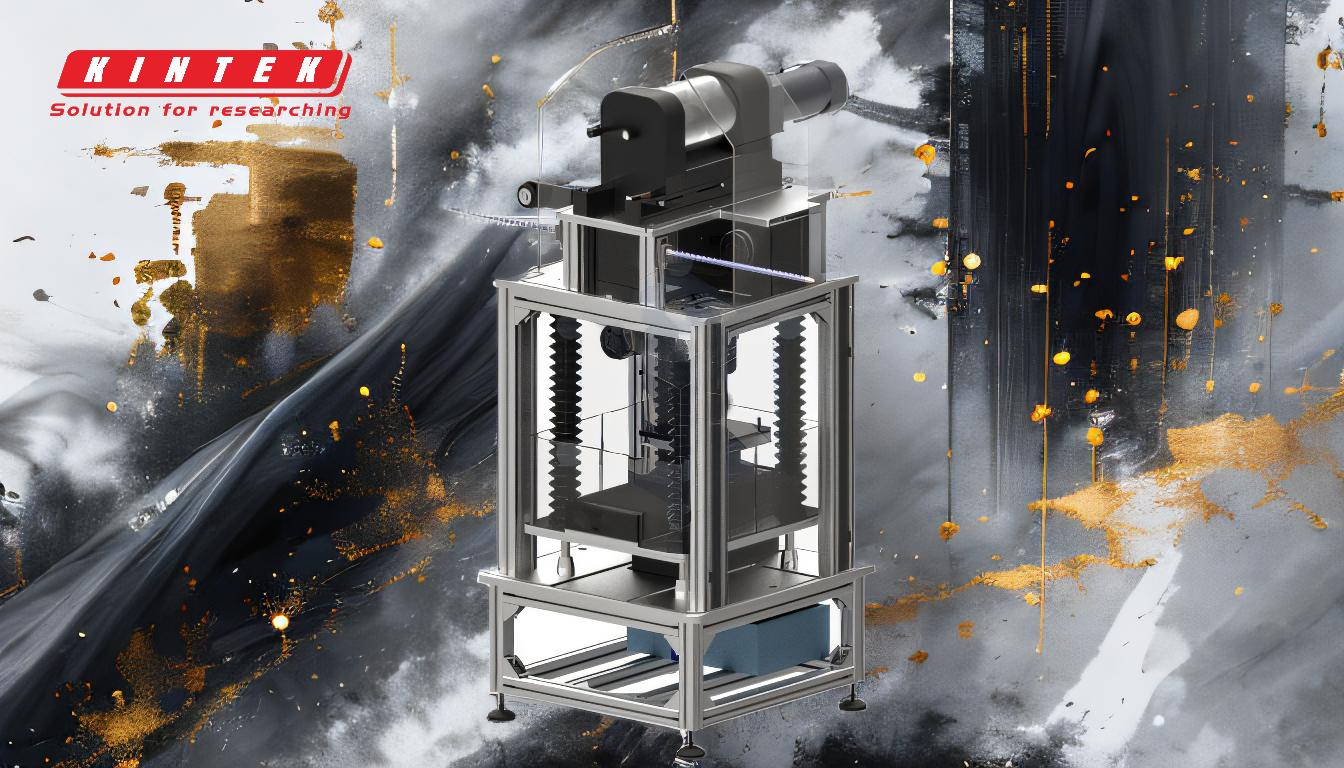
-
Impact on Film Quality:
- Local State Density and Electron Mobility: Substrate temperature directly affects the local state density and electron mobility within the film. Higher temperatures facilitate better atomic arrangement, leading to improved electrical properties.
- Optical Properties: The optical characteristics of the film, such as transparency and reflectivity, are influenced by the substrate temperature. Higher temperatures often result in films with superior optical performance.
-
Defect Density Reduction:
- Compensation of Suspended Bonds: Elevated substrate temperatures help in compensating for dangling or suspended bonds on the film surface. This compensation reduces the overall defect density, leading to a more uniform and defect-free film.
- Surface Reactions: Enhanced surface reactions at higher temperatures contribute to better film composition and adhesion, further reducing defects.
-
Film Denseness and Composition:
- Increased Denseness: Higher substrate temperatures promote denser film structures. This is crucial for applications requiring robust and durable coatings.
- Improved Composition: The chemical composition of the film is more uniform and controlled at elevated temperatures, ensuring consistent material properties across the film.
-
Process-Specific Temperature Requirements:
- PVD Processes: Typically, PVD processes operate at lower substrate temperatures. This is suitable for depositing films on temperature-sensitive substrates.
- CVD Processes: CVD generally requires higher substrate temperatures to facilitate the necessary chemical reactions for film deposition. However, plasma-assisted CVD can lower these temperature requirements, making it versatile for various applications.
-
Measurement and Control:
- Infrared Ratio Thermometry: Precise measurement of substrate temperature is crucial for controlling the deposition process. Techniques like two-color infrared ratio thermometry allow for accurate temperature monitoring, ensuring optimal film quality.
- Quartz Window and Incident Angle: The use of quartz windows and specific incident angles in temperature measurement setups ensures minimal interference and accurate thermal emission readings.
Understanding the effect of substrate temperature is essential for optimizing film deposition processes, ensuring high-quality films with desired properties for various applications.
Summary Table:
Aspect | Effect of Substrate Temperature |
---|---|
Film Quality | Higher temperatures improve local state density, electron mobility, and optical properties. |
Defect Density Reduction | Elevated temperatures compensate for suspended bonds, reducing defects and enhancing adhesion. |
Film Denseness & Composition | Increased denseness and uniform composition at higher temperatures. |
Process-Specific Requirements | PVD: Lower temperatures; CVD: Higher temperatures (plasma-assisted CVD lowers requirements). |
Measurement & Control | Infrared ratio thermometry ensures precise temperature control for optimal film quality. |
Optimize your film deposition processes with expert insights—contact us today!