Temperature plays a critical role in the sintering process, influencing the bonding, densification, and overall material properties of the final product. At high temperatures, typically several thousand degrees Celsius, particles bond and diffuse, leading to grain growth and densification. However, temperature control is essential, as improper heating rates or inconsistent temperatures can lead to uneven sintering, insufficient densification, or even material degradation. The sintering environment, including atmosphere and cooling rates, also interacts with temperature to determine the final mechanical properties, such as tensile strength and impact energy. Understanding the relationship between temperature and sintering kinetics is vital for optimizing the process and achieving desired material characteristics.
Key Points Explained:
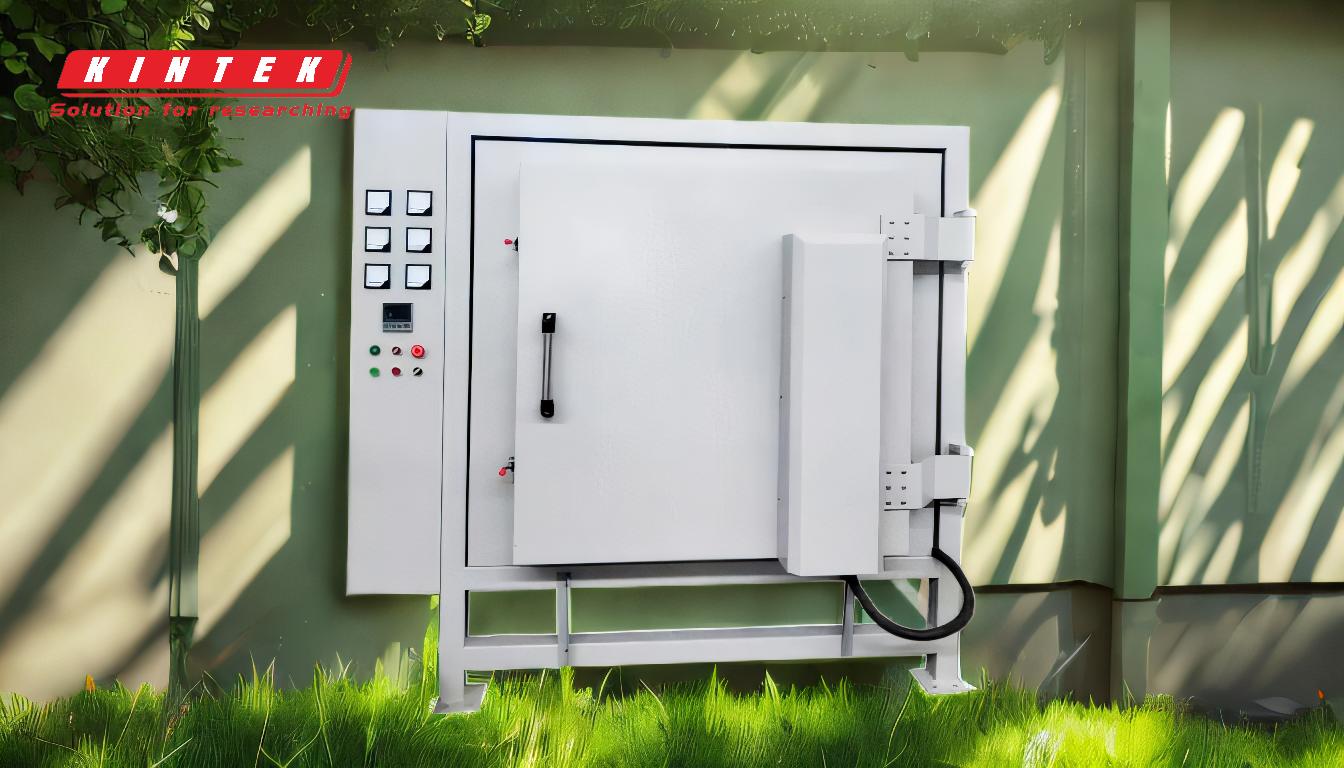
-
Temperature and Particle Bonding:
- High temperatures, often reaching thousands of degrees Celsius, are necessary to promote bonding and diffusion between powder particles.
- This bonding leads to grain growth and densification, which are critical for achieving the desired mechanical properties in the final product.
- Without sufficient temperature, the particles may not fuse properly, resulting in a weak or porous structure.
-
Temperature Control and Heating Rates:
- The rate at which temperature is increased (ramp rate) from room temperature to the sintering temperature is crucial.
- Rapid heating can cause uneven sintering, leading to insufficient densification in some areas and over-sintering in others. This can result in a high-temperature melting peak and high crystallinity, which may degrade material properties.
- Consistent temperature during the hold phase and controlled cooling rates are equally important to ensure uniform sintering and prevent defects.
-
Temperature and Sintering Kinetics:
- Sintering kinetics, including grain boundary diffusion and bulk diffusion, are heavily dependent on temperature.
- Higher temperatures accelerate these diffusion processes, leading to faster densification and improved material properties.
- However, excessive temperatures can cause undesirable effects, such as grain coarsening or melting, which can compromise the material's integrity.
-
Temperature and Material Properties:
- High-temperature sintering can enhance mechanical properties such as tensile strength, bending fatigue strength, and impact energy.
- The sintering temperature must be carefully chosen based on the material composition and desired properties to avoid over-sintering or under-sintering.
- For example, smaller particles and homogeneous compositions require precise temperature control to achieve optimal densification.
-
Interaction with Other Variables:
- Temperature interacts with other sintering variables, such as atmosphere (air, vacuum, or inert gases), pressure, and particle size.
- For instance, in a vacuum or inert atmosphere, higher temperatures can be used without oxidation, leading to better densification and material properties.
- Pressure can complement temperature by enhancing particle rearrangement and eliminating porosity, especially in materials that are difficult to sinter at lower temperatures.
-
Temperature Ranges and Their Effects:
- From room temperature to around 900°C, there is little effect on sintering, as most materials require higher temperatures for significant diffusion and bonding.
- The critical temperature range is typically between 900°C and the material's melting point, where sintering kinetics are most active.
- Cooling rates from the sintering temperature back to around 900°C are also critical, as rapid cooling can introduce thermal stresses and affect the final microstructure.
-
Practical Considerations for Equipment and Consumables Purchasers:
- When selecting sintering equipment, consider the maximum temperature capabilities, temperature uniformity, and control precision.
- Ensure that the equipment can handle the required heating and cooling rates for the specific materials being processed.
- For consumables, such as furnace linings or heating elements, choose materials that can withstand the high temperatures and thermal cycling associated with sintering.
By understanding the effects of temperature on the sintering process, purchasers can make informed decisions about equipment and consumables to optimize sintering outcomes and achieve the desired material properties.
Summary Table:
Aspect | Impact of Temperature |
---|---|
Particle Bonding | High temperatures promote bonding and diffusion, leading to grain growth and densification. |
Heating Rates | Controlled ramp rates prevent uneven sintering and material degradation. |
Sintering Kinetics | Higher temperatures accelerate diffusion, but excessive heat can cause grain coarsening. |
Material Properties | Optimal sintering enhances tensile strength, fatigue strength, and impact energy. |
Interaction with Variables | Temperature works with atmosphere, pressure, and particle size to influence outcomes. |
Temperature Ranges | Critical range: 900°C to melting point; cooling rates affect microstructure. |
Equipment Considerations | Choose equipment with precise temperature control and uniform heating capabilities. |
Ready to optimize your sintering process? Contact our experts today for tailored solutions!