Electric arc furnaces (EAFs) are versatile industrial equipment primarily used for melting and refining steel. They are a cornerstone of modern steelmaking, especially in recycling scrap steel, but they can also process other raw materials like hot metal from blast furnaces or direct-reduced iron. EAFs are capable of producing a wide range of steel grades, including carbon steel, alloy steel, stainless steel, tool steel, and specialty alloys. The process involves generating high temperatures (up to 3275°F or 1800°C) using electric arcs, which melt the raw materials efficiently. EAFs are energy-intensive, requiring 350-370 kWh of energy to melt scrap, and are widely used in industries such as automotive, aerospace, construction, and food processing.
Key Points Explained:
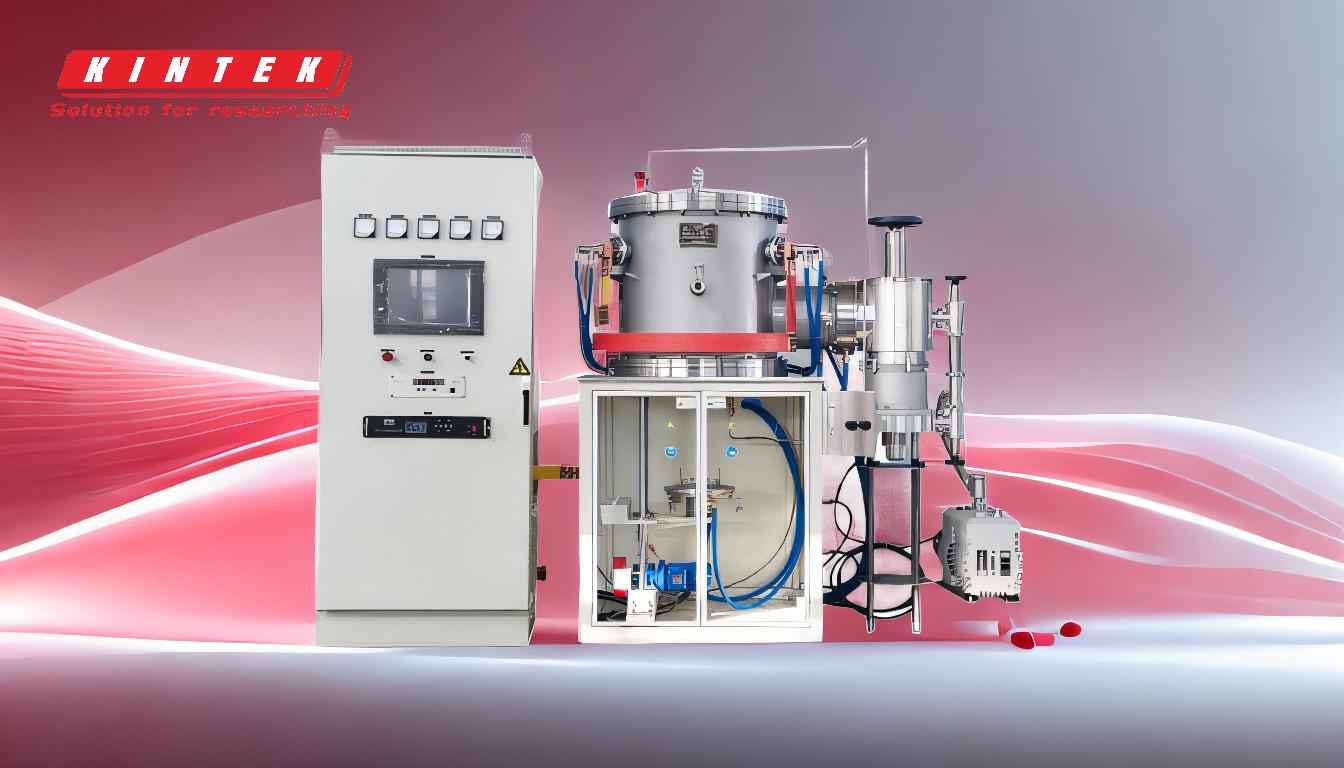
-
Primary Use: Recycling Scrap Steel
- Electric arc furnaces are primarily used to recycle scrap steel, making them a sustainable and cost-effective solution for steel production.
- Scrap steel is melted using high-powered electric arcs, which generate extreme heat to liquefy the metal.
- This process reduces the reliance on virgin iron ore and minimizes environmental impact compared to traditional blast furnaces.
-
Versatility in Raw Materials
- While scrap steel is the most common feedstock, EAFs can also process other materials:
- Hot metal from blast furnaces: This can be used when available economically.
- Direct-reduced iron (DRI): A high-quality alternative to scrap, often used in regions with limited scrap availability.
- This flexibility allows EAFs to adapt to varying market conditions and material availability.
- While scrap steel is the most common feedstock, EAFs can also process other materials:
-
Production of Various Steel Grades
- EAFs are capable of producing a wide range of steel grades, including:
- Carbon steel: Used in construction, automotive, and machinery.
- Alloy steel: Enhanced with elements like manganese, nickel, or chromium for specific properties.
- Stainless steel: Resistant to corrosion, widely used in food processing, chemical industries, and medical equipment.
- Tool steel: High-strength steel used for cutting and shaping tools.
- Specialty alloys: Tailored for specific applications in aerospace, energy, and other high-tech industries.
- This versatility makes EAFs indispensable for industries requiring high-quality and specialized steels.
- EAFs are capable of producing a wide range of steel grades, including:
-
Energy Consumption and Efficiency
- The EAF process is energy-intensive, requiring approximately 350-370 kWh of electricity to melt one ton of scrap steel.
- Despite the high energy demand, EAFs are more efficient than traditional blast furnaces in terms of resource utilization and environmental impact.
- Modern EAFs are equipped with advanced technologies to optimize energy use and reduce emissions.
-
Process Details
- Electric Arc Generation: Electrodes create an electric arc that generates the heat needed to melt the metal. Temperatures can reach up to 3275°F (1800°C).
- Slag Formation: Limestone is often added to the furnace to form slag, which helps remove impurities from the molten metal.
- Oxygen Injection: Oxygen may be introduced during the process to refine the steel and remove carbon and other impurities.
-
Applications Across Industries
- EAFs are used in various industries to produce steel products such as:
- Large slabs and beams: For construction and infrastructure projects.
- Shredded scrap: Recycled into new steel products.
- Specialty steels: For automotive, aircraft, machine tools, and transportation industries.
- Their ability to produce high-quality steel makes them essential for meeting the demands of modern manufacturing and construction.
- EAFs are used in various industries to produce steel products such as:
-
Environmental and Economic Benefits
- EAFs contribute to sustainability by recycling scrap steel, reducing the need for mining and processing raw materials.
- They produce fewer greenhouse gas emissions compared to traditional steelmaking methods.
- The flexibility in feedstock and the ability to produce a wide range of steel grades make EAFs economically advantageous for steelmakers.
In summary, electric arc furnaces are a critical technology in modern steel production, offering versatility, efficiency, and sustainability. They enable the recycling of scrap steel while producing high-quality and specialized steels for a wide range of industrial applications.
Summary Table:
Key Feature | Details |
---|---|
Primary Use | Recycling scrap steel for sustainable steel production. |
Versatility | Processes scrap steel, hot metal, and direct-reduced iron (DRI). |
Steel Grades Produced | Carbon steel, alloy steel, stainless steel, tool steel, specialty alloys. |
Energy Consumption | 350-370 kWh per ton of scrap steel. |
Applications | Automotive, aerospace, construction, food processing, and more. |
Environmental Benefits | Reduces greenhouse gas emissions and reliance on virgin iron ore. |
Learn how electric arc furnaces can transform your steel production—contact our experts today!