The energy efficiency of a rotary kiln is a critical factor in its operational performance, influenced by various design and operational parameters. Key factors include the kiln's inclination angle, rotation speed, temperature, material flow rate, and discharge rate, which collectively determine how effectively the kiln processes materials. Additionally, thermal efficiency can be enhanced through design improvements such as heat recuperators (e.g., pre-heaters and coolers) that recover energy from exhaust gases and preheat combustion air. Regular maintenance, monitoring, and upgrades to supporting equipment, such as burners, also play a significant role in optimizing energy efficiency. Furthermore, understanding the material's properties, such as particle size distribution, thermal conductivity, and chemical composition, is essential for designing a kiln that maximizes energy efficiency while achieving desired process outcomes.
Key Points Explained:
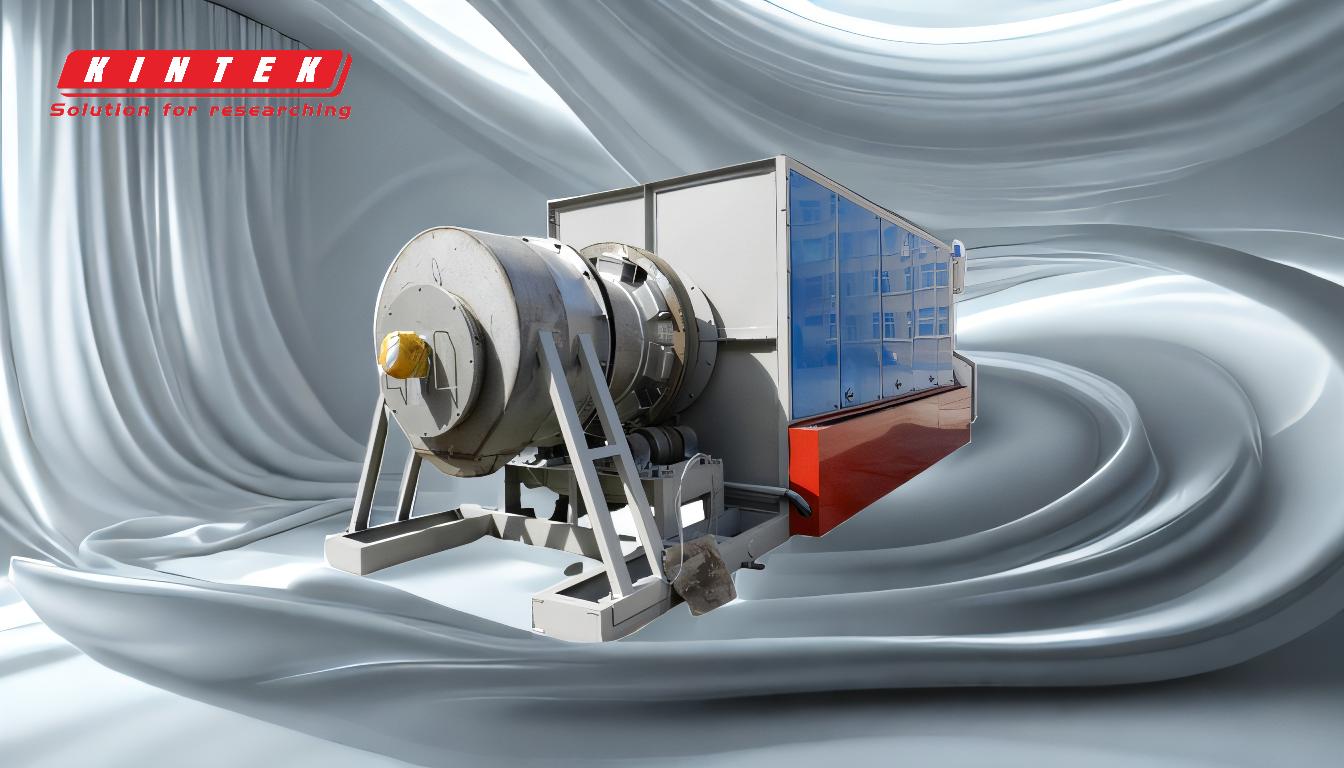
-
Operational Parameters Affecting Energy Efficiency
- The energy efficiency of a rotary kiln is directly influenced by operational parameters such as:
- Inclination angle: Determines the residence time of materials in the kiln.
- Rotation speed: Affects the mixing and heat transfer within the kiln.
- Temperature: Must be optimized to ensure proper material processing without excessive energy consumption.
- Material flow rate and discharge rate: These control the throughput and ensure consistent processing conditions.
- These parameters must be carefully balanced to achieve optimal energy efficiency.
- The energy efficiency of a rotary kiln is directly influenced by operational parameters such as:
-
Design Improvements for Enhanced Efficiency
- Rotary kilns can incorporate design features to improve energy efficiency:
- Heat recuperators: Devices like pre-heaters recover heat from exhaust gases to preheat incoming materials, reducing the energy required for heating.
- Coolers: These not only cool the final product but also recover heat for preheating combustion air or other energy needs.
- Refractory ceramic fiber layers: Adding these to the kiln lining improves thermal insulation, reducing heat loss and enhancing thermal efficiency.
- Rotary kilns can incorporate design features to improve energy efficiency:
-
Material Properties and Their Impact
- The design and operation of a rotary kiln must account for the material's properties, including:
- Particle size distribution: Affects how materials flow and interact within the kiln.
- Thermal conductivity and specific heat: Influence the rate at which materials heat up and transfer heat.
- Chemical composition and heat of reaction: Determine the energy required for chemical transformations.
- Understanding these properties allows for better kiln design and operation, minimizing energy waste.
- The design and operation of a rotary kiln must account for the material's properties, including:
-
Maintenance and Equipment Upgrades
- Regular maintenance and monitoring are essential for sustaining energy efficiency:
- Routine inspections: Ensure equipment operates at peak performance and identify areas for improvement.
- Upgrading supporting equipment: For example, replacing single-channel burners with multi-channel burners improves combustion efficiency and reduces material residence time, enhancing overall energy efficiency.
- Regular maintenance and monitoring are essential for sustaining energy efficiency:
-
Quantitative Understanding of Transport Phenomena
- Improving energy efficiency requires a deeper understanding of:
- Momentum transport: Determines how particles move within the kiln, affecting mixing and heat transfer.
- Energy transport: Influences the heating rate of individual particles, which is critical for optimizing thermal efficiency.
- Advances in these areas can lead to more efficient kiln designs and operations.
- Improving energy efficiency requires a deeper understanding of:
-
Practical Steps for Energy Efficiency Optimization
- To maximize energy efficiency, consider the following steps:
- Optimize operational parameters: Adjust inclination angle, rotation speed, and temperature to achieve the best balance of throughput and energy use.
- Invest in heat recovery systems: Install pre-heaters and coolers to capture and reuse waste heat.
- Upgrade equipment: Use advanced burners and refractory materials to improve combustion and insulation.
- Conduct regular maintenance: Ensure all components are functioning efficiently and address any issues promptly.
- To maximize energy efficiency, consider the following steps:
By addressing these key points, rotary kiln operators can significantly improve energy efficiency, reducing operational costs and environmental impact while maintaining high production standards.
Summary Table:
Key Factors | Impact on Energy Efficiency |
---|---|
Inclination Angle | Determines material residence time, affecting heat transfer and energy use. |
Rotation Speed | Influences mixing and heat transfer efficiency within the kiln. |
Temperature | Optimized to ensure proper material processing without excessive energy consumption. |
Material Flow Rate | Controls throughput and ensures consistent processing conditions. |
Heat Recuperators | Recover heat from exhaust gases to preheat materials, reducing energy demand. |
Refractory Layers | Improve thermal insulation, minimizing heat loss and enhancing efficiency. |
Material Properties | Particle size, thermal conductivity, and chemical composition affect energy requirements. |
Maintenance & Upgrades | Regular inspections and advanced equipment upgrades sustain optimal energy efficiency. |
Ready to optimize your rotary kiln's energy efficiency? Contact our experts today for tailored solutions!