Flash sintering (FS) is an advanced sintering technique characterized by its low energy consumption and ultra-fast processing speed. It involves applying an electric field (DC or AC) directly to a material sample while heating it in a furnace. When a threshold temperature is reached, a sudden nonlinear increase in current occurs, generating intense Joule heating. This rapid heating densifies the material within seconds, often at much lower temperatures compared to traditional sintering methods. Flash sintering is particularly effective for achieving high-density materials without degrading their original properties, making it suitable for sintering amorphous, nanocrystalline, and gradient functional materials.
Key Points Explained:
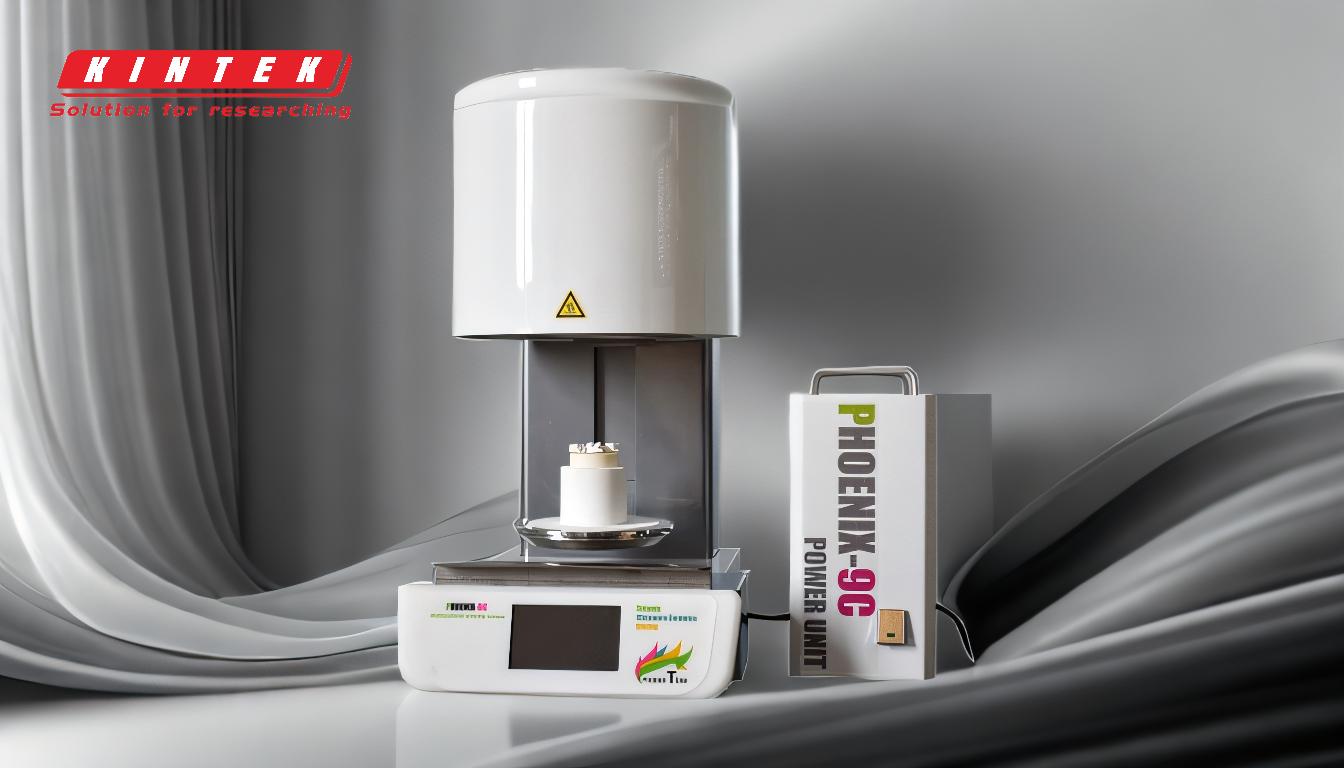
-
Definition and Purpose of Flash Sintering:
- Flash sintering is a modern sintering technology designed to achieve rapid densification of materials at lower temperatures and with significantly reduced energy consumption.
- It is particularly useful for sintering materials that are sensitive to high temperatures or require precise control over their microstructure, such as amorphous or nanocrystalline materials.
-
Mechanism of Flash Sintering:
- Electric Field Application: A DC or AC electric field is applied directly to the material sample.
- Threshold Temperature: The material is heated in a furnace until it reaches a specific threshold temperature.
- Thermal Runaway and Joule Heating: At this threshold, a sudden nonlinear increase in current occurs, leading to thermal runaway and intense Joule heating.
- Rapid Densification: The intense heating causes the material to densify rapidly, often within seconds.
-
Advantages of Flash Sintering:
- Low Energy Consumption: Flash sintering requires less energy compared to traditional sintering methods.
- Ultra-Fast Processing: The entire sintering process can be completed in seconds, significantly reducing processing time.
- Low-Temperature Sintering: Materials can be sintered at much lower temperatures, preserving their original properties and microstructure.
- Versatility: Suitable for a wide range of materials, including amorphous, nanocrystalline, and gradient functional materials.
-
Comparison with Traditional Sintering Methods:
- Hot Press Sintering: Involves heating and pressurizing the material in a furnace, which is slower and requires higher temperatures.
- Spark Plasma Sintering (SPS): Uses self-heating through electrical discharge to achieve rapid temperature rise, but flash sintering is even faster and more energy-efficient.
- Microwave Sintering: Uses microwave energy for heating, but flash sintering provides more precise control over the sintering process and faster results.
-
Applications of Flash Sintering:
- Amorphous and Nanocrystalline Materials: Flash sintering allows these materials to be densified before grain growth occurs, preserving their unique properties.
- Gradient Functional Materials: Effective for sintering bonds between different metals or between metals and non-metals, enabling the creation of complex, multi-material structures.
- Energy-Efficient Manufacturing: Ideal for industries looking to reduce energy consumption and processing time while maintaining high material quality.
-
Key Steps in Flash Sintering:
- Sample Preparation: The material sample is prepared and placed in the furnace.
- Application of Electric Field: A DC or AC electric field is applied to the sample.
- Heating: The furnace heats the sample to the threshold temperature.
- Flash Event: Once the threshold is reached, the current increases nonlinearly, causing rapid Joule heating and densification.
- Cooling: The sintered material is cooled gradually to room temperature.
-
Challenges and Considerations:
- Control of Parameters: Precise control of temperature, electric field, and current is essential to achieve consistent results.
- Material Compatibility: Not all materials may be suitable for flash sintering, and further research is needed to expand its applicability.
- Equipment Requirements: Specialized equipment capable of applying precise electric fields and monitoring the sintering process is required.
In summary, flash sintering is a groundbreaking technology that offers significant advantages in terms of energy efficiency, processing speed, and material quality. Its ability to sinter materials at low temperatures and with minimal energy consumption makes it a promising technique for various industrial applications. However, careful control of process parameters and further research into material compatibility are necessary to fully realize its potential.
Summary Table:
Aspect | Details |
---|---|
Definition | Advanced sintering technique for rapid densification at low temperatures. |
Key Mechanism | Electric field application, threshold temperature, and Joule heating. |
Advantages | Low energy, ultra-fast processing, low-temperature sintering, versatility. |
Applications | Amorphous, nanocrystalline, and gradient functional materials. |
Challenges | Precise parameter control, material compatibility, specialized equipment. |
Ready to explore how flash sintering can transform your material processing? Contact us today for expert guidance!