CVD stands for Chemical Vapor Deposition, a process used to deposit thin films or coatings onto a substrate by utilizing chemical reactions in a vapor phase. This technology is widely employed in various industries, including aerospace, semiconductors, solar cells, smart glass, and nanotechnology, to produce high-quality thin films for advanced applications. CVD reactors are specialized equipment designed to facilitate this process, enabling precise control over the deposition of materials like graphene, carbon nanotubes, and semiconductor thin films.
Key Points Explained:
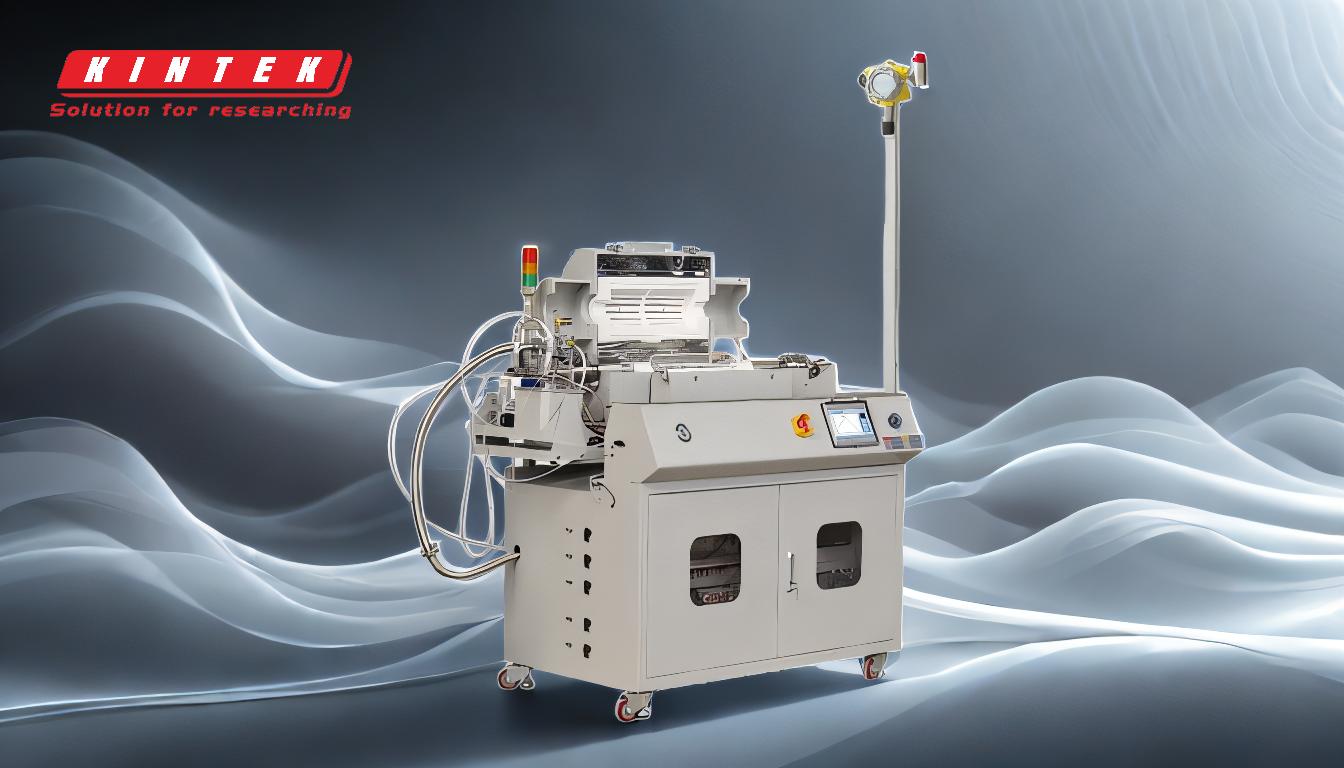
-
Full Form of CVD:
- CVD stands for Chemical Vapor Deposition.
- It is a technology that uses chemical reactions in a vapor phase to deposit thin films or coatings onto a substrate.
-
Purpose of CVD Reactors:
- CVD reactors are designed to facilitate the deposition of high-quality thin films.
- These reactors are used in research and industrial applications to produce materials with "device quality," meaning they meet stringent performance standards.
-
Applications of CVD Reactors:
- Semiconductors: CVD is used to deposit thin films for semiconductor devices.
- Aerospace Engineering: High-performance coatings are applied to materials used in aerospace applications.
- Solar Cells: CVD is used to create thin-film solar cells for renewable energy.
- Smart Glass: CVD deposits coatings that enable functionalities like tinting or energy efficiency.
- Nanotechnology: CVD is used to grow materials like carbon nanotubes, nanowires, and graphene.
- LEDs and MEMs: CVD is critical in the fabrication of light-emitting diodes (LEDs) and microelectromechanical systems (MEMs).
- Diamond Growth: CVD is used to create synthetic diamonds in laboratory settings.
-
How CVD Reactors Work:
- A chemical vapor is introduced into the reactor chamber.
- The vapor undergoes a chemical reaction, often at moderate temperatures and pressures, to form a solid material.
- The solid material is deposited onto a substrate, creating a thin film or coating.
-
Advantages of CVD Reactors:
- Precision: CVD allows for precise control over the thickness and composition of the deposited material.
- Versatility: CVD can deposit a wide range of materials, including metals, ceramics, and polymers.
- Scalability: CVD processes can be scaled for industrial production.
-
Types of CVD Reactors:
- Atmospheric Pressure CVD (APCVD): Operates at atmospheric pressure, often used for simpler processes.
- Low-Pressure CVD (LPCVD): Operates at reduced pressures, allowing for better control and uniformity.
- Plasma-Enhanced CVD (PECVD): Uses plasma to enhance the chemical reaction, enabling lower temperature processes.
-
Example Use Case:
- CVD reactors are used in the production of liquid crystal displays (LCDs) by depositing tin oxide on glass substrates.
- This process is critical for creating conductive layers in LCDs and other electronic devices.
-
Future of CVD Reactors:
- Ongoing advancements aim to improve the efficiency, precision, and versatility of CVD reactors.
- New designs, such as the replacement of discontinuous APCVD reactors, enable more refined studies and processes.
By understanding the full form and functionality of CVD reactors, purchasers and researchers can better evaluate their suitability for specific applications, ensuring optimal performance and cost-effectiveness in their projects.
Summary Table:
Aspect | Details |
---|---|
Full Form | Chemical Vapor Deposition (CVD) |
Purpose | Deposits high-quality thin films or coatings onto substrates |
Applications | Semiconductors, aerospace, solar cells, smart glass, nanotechnology, LEDs |
Advantages | Precision, versatility, scalability |
Types of CVD Reactors | APCVD, LPCVD, PECVD |
Example Use Case | Tin oxide deposition for LCD production |
Future | Improved efficiency, precision, and versatility |
Ready to explore how CVD reactors can enhance your projects? Contact us today for expert guidance!