The graphite furnace technique is a high-temperature processing method that utilizes graphite as a heating element and structural material. It is widely used in various industrial and research applications due to its ability to achieve extremely high temperatures, fast heating rates, and excellent temperature control. Graphite furnaces are versatile and can operate in different environments, including vacuum or protective atmospheres, making them suitable for processes like sintering, graphitizing, silicizing, and pyrolysis. Their applications span from material testing and alloy melting to advanced research in reaction kinetics and high-pressure environments. Below, the key aspects of the graphite furnace technique are explained in detail.
Key Points Explained:
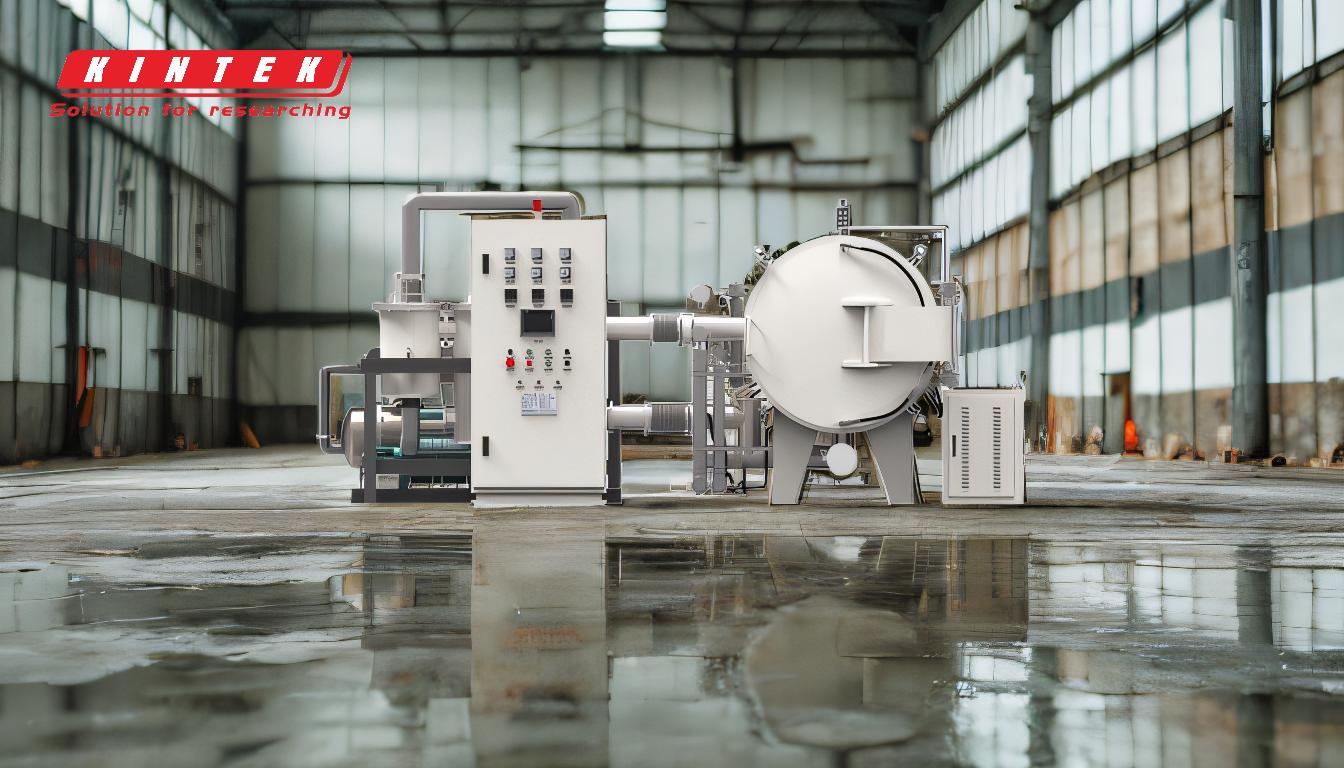
-
High-Temperature Capability:
- Graphite furnaces are designed to generate extremely high temperatures, making them ideal for processes that require intense heat, such as sintering, graphitizing, and pyrolysis.
- The use of graphite as a heating element allows for efficient heat transfer and stability at high temperatures, which is critical for achieving consistent results in high-temperature applications.
-
Fast Heating Speed:
- One of the standout features of graphite furnaces is their ability to heat up rapidly. This reduces processing time and improves efficiency, which is particularly beneficial in industrial settings where time is a critical factor.
- The fast heating speed is attributed to the excellent thermal conductivity of graphite, which ensures that heat is distributed evenly and quickly throughout the furnace.
-
Temperature Uniformity and Control:
- Graphite furnaces are known for their good temperature uniformity, which ensures that all parts of the material being processed are exposed to the same temperature conditions. This is essential for achieving consistent results in processes like sintering and alloy melting.
- High-temperature controllability allows for precise adjustments, making it possible to maintain specific temperature profiles required for advanced research and industrial applications.
-
Versatility in Operating Environments:
- Graphite furnaces can operate in a variety of environments, including vacuum and protective atmospheres. This flexibility makes them suitable for processes that require controlled conditions to prevent oxidation or contamination.
- For example, vacuum graphite furnaces are used for high-temperature treatment of materials in environments where air or other reactive gases could interfere with the process.
-
Common Applications:
- Melting and Alloy Production: Graphite furnaces are used to melt metals and create alloys, benefiting from their high-temperature capabilities and uniform heating.
- Material Testing and Research: They are employed in test facilities to investigate reaction kinetics at high temperatures and pressures, as well as to study the behavior of solid electrolytes.
- Sintering and Graphitizing: These processes involve compacting and heating materials to form solid structures, which is facilitated by the high temperatures and controlled environments provided by graphite furnaces.
- Specialized Processes: Applications like pressure sintering, foaming, and silicizing rely on the unique properties of graphite furnaces to achieve the desired material properties.
-
Advantages of Graphite Furnaces:
- Ease of Operation: Graphite tube furnaces, in particular, are noted for their user-friendly design, making them accessible for both industrial and research purposes.
- Durability and Stability: Graphite's resistance to thermal shock and chemical stability at high temperatures contribute to the longevity and reliability of these furnaces.
- Energy Efficiency: The fast heating speed and efficient heat transfer reduce energy consumption, making graphite furnaces a cost-effective solution for high-temperature processing.
In summary, the graphite furnace technique is a powerful and versatile method for high-temperature processing, offering advantages such as rapid heating, precise temperature control, and adaptability to various environments. Its applications are diverse, ranging from industrial manufacturing to advanced scientific research, making it an essential tool in material science and engineering.
Summary Table:
Key Feature | Description |
---|---|
High-Temperature Capability | Achieves extreme temperatures for sintering, graphitizing, and pyrolysis. |
Fast Heating Speed | Rapid heating due to graphite's excellent thermal conductivity. |
Temperature Control | Ensures uniform heating and precise temperature adjustments. |
Versatile Environments | Operates in vacuum or protective atmospheres, preventing oxidation. |
Common Applications | Melting, alloy production, material testing, sintering, and specialized processes. |
Advantages | Easy operation, durability, stability, and energy efficiency. |
Discover how the graphite furnace technique can enhance your processes—contact us today for expert advice!