The heat capacity of a muffle furnace is not a fixed value but depends on several factors, including the furnace's design, materials, insulation, and the specific heating elements used. Muffle furnaces are designed to reach high temperatures, often exceeding 1000°C, and their heat capacity is influenced by their ability to store and transfer heat efficiently. Modern electric muffle furnaces, which use high-temperature heating elements like Nichrome, are designed for precise temperature control and uniform heat distribution. The heat capacity is also affected by the furnace's chamber size, insulation thickness, and the materials being processed. Overall, the heat capacity is a function of the furnace's ability to maintain high temperatures while minimizing heat loss.
Key Points Explained:
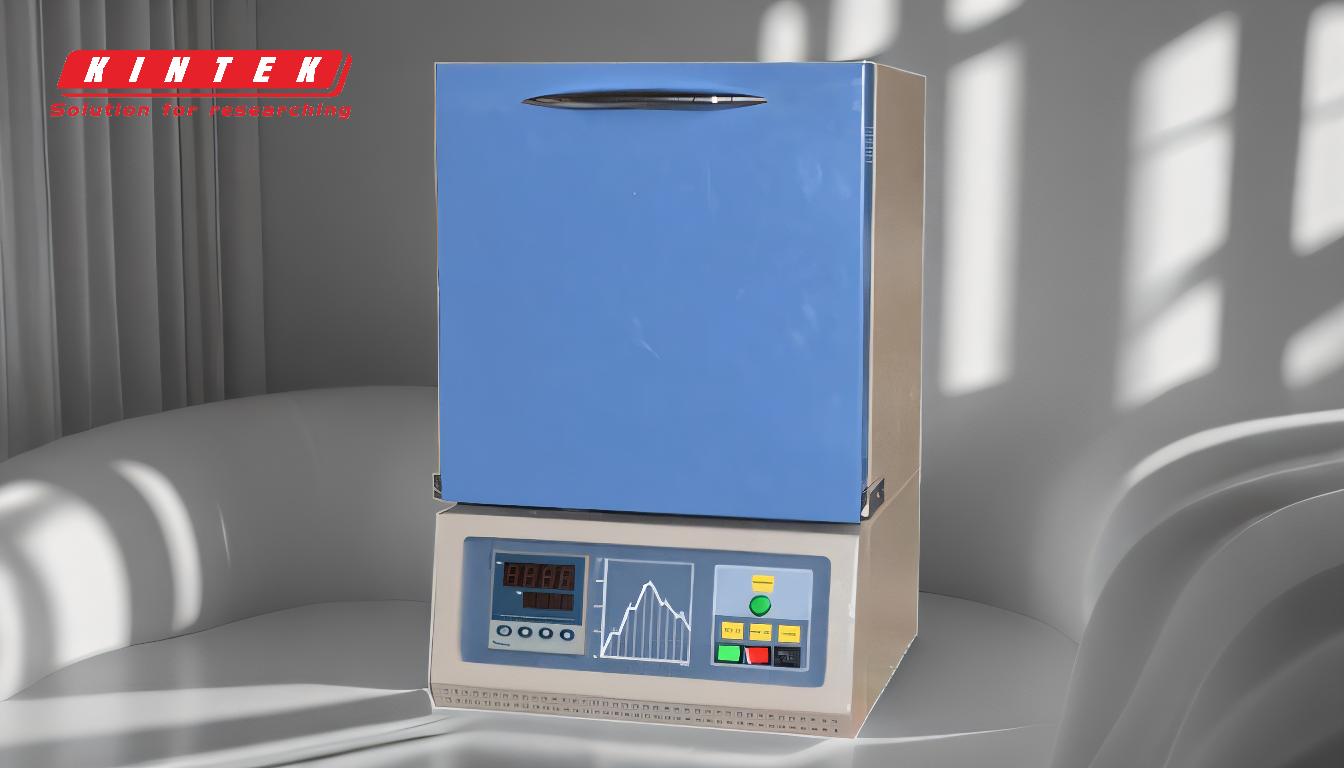
-
Definition and Design of a Muffle Furnace:
- A muffle furnace is a high-temperature furnace with separate combustion and heating chambers. Historically, it was designed to prevent contamination from combustion byproducts. Modern versions are typically electric, using high-temperature heating elements like Nichrome, which eliminate combustion byproducts and allow for precise temperature control.
- The heating chamber, often called the "dehydration tank," is airtight, ensuring that the material being heated is not contaminated.
-
Heat Capacity Factors:
- Materials and Insulation: Muffle furnaces are constructed with heat-resistant materials and thick insulating walls to maintain high temperatures. The materials used, such as high-temperature ceramics and metals, contribute to the furnace's ability to store heat.
- Heating Elements: Electric resistance heating elements, like Nichrome, are used in modern muffle furnaces. These elements can reach temperatures up to 1800°C and are designed for efficient heat transfer and uniform temperature distribution.
- Chamber Size and Design: The size of the heating chamber and the thickness of the insulation affect the furnace's heat capacity. Smaller chambers with thicker walls are more efficient at maintaining high temperatures.
-
Temperature Range and Control:
- Muffle furnaces can reach very high temperatures, often exceeding 1000°C, with some models capable of reaching up to 2000°C. The ability to control and maintain these temperatures is crucial for applications in experimental research and material processing.
- Temperature control options include manual, digital, and programmable controls, which allow for precise regulation of the furnace's heat output.
-
Applications and Efficiency:
- Muffle furnaces are used in various industries for processes that require high temperatures, such as metalworking, ceramics, and experimental research. Their design minimizes processing time and costs by efficiently maintaining high temperatures.
- The heat capacity of a muffle furnace is optimized for specific applications, ensuring that the furnace can handle the thermal demands of the materials being processed.
-
Heat Transfer Mechanisms:
- Muffle furnaces use a combination of radiant and convection heat transfer to ensure homogeneous treatment of workpieces. This dual mechanism enhances the furnace's ability to distribute heat evenly, contributing to its overall heat capacity.
In summary, the heat capacity of a muffle furnace is influenced by its design, materials, insulation, and heating elements. Modern electric muffle furnaces are engineered for high-temperature applications, with precise temperature control and efficient heat transfer mechanisms. The furnace's ability to maintain high temperatures while minimizing heat loss is a key factor in its heat capacity, making it suitable for a wide range of industrial and research applications.
Summary Table:
Factor | Description |
---|---|
Design | Separate combustion and heating chambers prevent contamination. |
Materials & Insulation | Heat-resistant materials and thick insulation maintain high temperatures. |
Heating Elements | Nichrome elements ensure efficient heat transfer and uniform temperature. |
Chamber Size | Smaller chambers with thicker walls improve heat retention. |
Temperature Control | Manual, digital, or programmable controls for precise heat regulation. |
Heat Transfer | Radiant and convection mechanisms ensure even heat distribution. |
Discover the perfect muffle furnace for your needs—contact our experts today!