Sintering is a process with ancient roots, particularly in pottery and ceramics, dating back thousands of years. Its application in powder metallurgy can be traced to ancient civilizations like the Egyptians. Over time, sintering has evolved significantly, with advancements in materials and technologies. The process involves compacting and forming solid materials by applying heat or pressure without liquefaction, allowing atoms to diffuse and fuse particles into a cohesive structure. Modern sintering, as a scientific and commercial practice, began with William Coolidge's work in 1909, leading to the production of ductile tungsten wire. Today, sintering is a well-established method for fabricating components, with applications ranging from ceramics to metals and cemented carbides.
Key Points Explained:
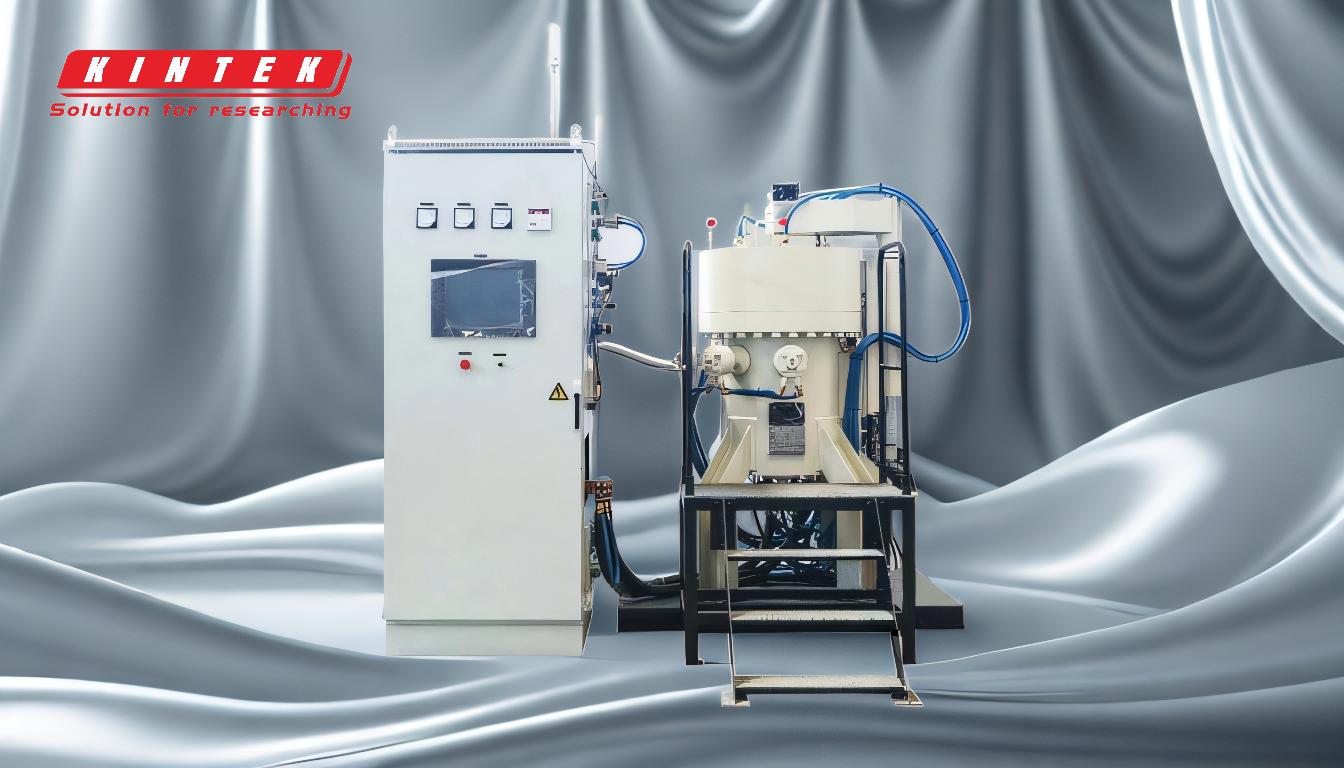
-
Ancient Origins of Sintering:
- Sintering has been used in pottery and ceramics for thousands of years, with evidence of its application in ancient civilizations like the Egyptians.
- Primitive methods involved the wet fusion of clay particles to create durable ceramic items, as well as metal powder decoration and glazing.
-
Definition and Process of Sintering:
- Sintering, or frittage, is a process that compacts and forms a solid mass of material by applying heat or pressure without melting it to the point of liquefaction.
- Atoms diffuse across particle boundaries, fusing them into a single solid piece, making it ideal for materials with high melting points like tungsten and molybdenum.
-
Evolution of Sintering Technologies:
- Modern sintering began scientifically and commercially with William Coolidge's work in 1909, which led to the production of ductile tungsten wire for lamp filaments.
- The science of sintering started to emerge in the 1940s and matured by the mid-1980s, leading to significant advancements in materials and applications.
-
Applications of Sintering:
- Sintering is well established as a component fabrication approach, with applications in ceramics, metals, and cemented carbides.
- Ceramic sintering has been practiced for 26,000 years, while metallic sintering and cemented carbides are more recent developments.
-
Role of Sintering Furnaces:
- The development of sintering furnaces has been crucial in advancing sintering technologies, allowing for precise control over temperature and pressure to achieve desired material properties.
- These furnaces have enabled the production of high-performance materials used in various industries, from electronics to aerospace.
By understanding the history and evolution of sintering, we can appreciate its significance in modern manufacturing and material science. The continuous advancements in sintering technologies, particularly through the use of sintering furnaces, have expanded its applications and improved the quality of sintered products.
Summary Table:
Key Aspect | Details |
---|---|
Ancient Origins | Used in pottery and ceramics for thousands of years, dating back to ancient civilizations like the Egyptians. |
Definition | Compacts and forms solid materials by applying heat or pressure without liquefaction. |
Modern Evolution | Began scientifically with William Coolidge's work in 1909, leading to ductile tungsten wire production. |
Applications | Used in ceramics, metals, and cemented carbides for component fabrication. |
Role of Sintering Furnaces | Crucial for precise temperature and pressure control, enabling high-performance materials. |
Discover how sintering can transform your manufacturing process—contact our experts today!