Sintering is a critical process in material manufacturing, particularly in powder metallurgy, where it transforms powdered materials into dense, strong, and functional components. This process involves heating compacted metal powders to temperatures just below their melting points, allowing the particles to bond and form a solid structure. Sintering is essential for producing materials with high melting points or complex compositions that are difficult to process through traditional melting and casting methods. It also offers sustainability benefits by minimizing waste and enhancing the structural integrity of the final product. Additionally, sintering plays a vital role in industries like steel production, where it improves blast furnace efficiency and reduces operational costs.
Key Points Explained:
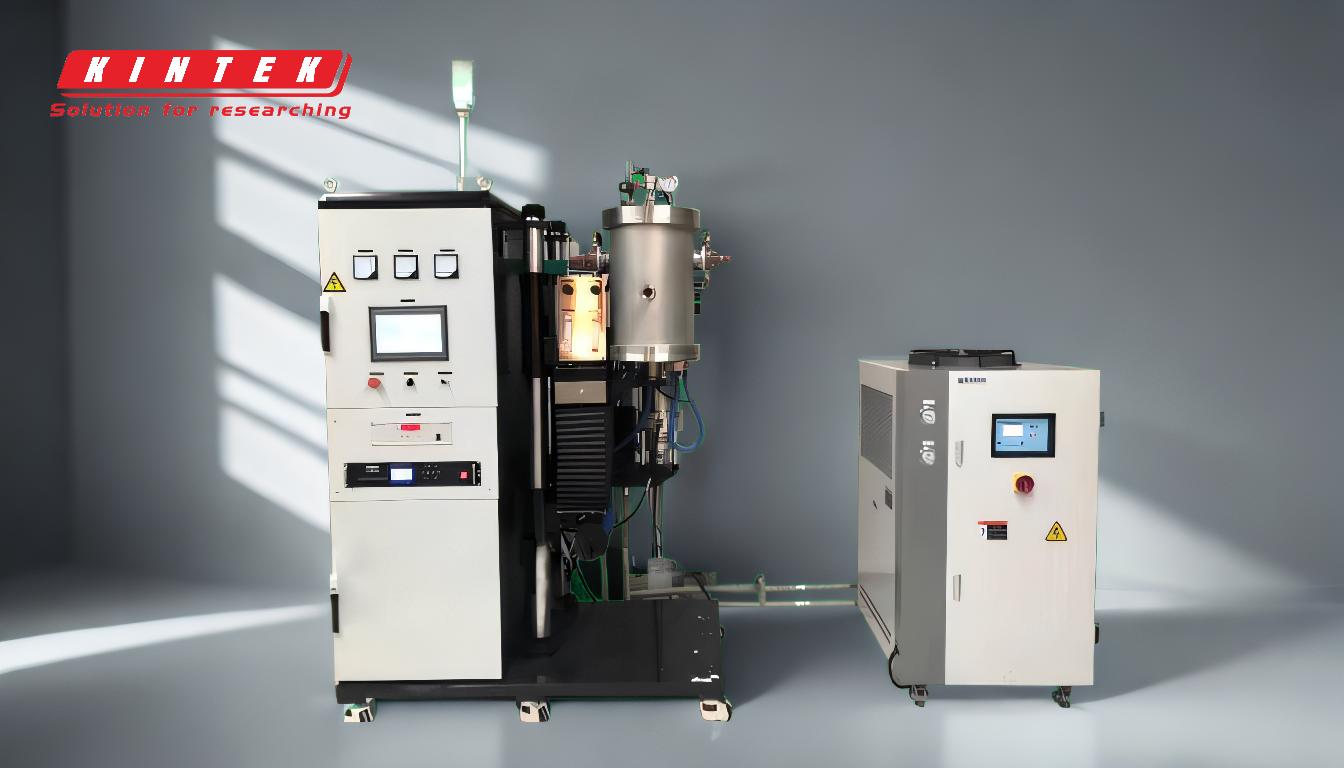
-
Definition and Process of Sintering:
- Sintering is a thermal process used in powder metallurgy where compacted metal powders are heated to just below their melting points. This causes the particles to bond together, forming a dense and strong material. The process is analogous to how ice cubes fuse at their contact points in a glass of water, creating a solid structure without fully melting.
-
Importance in Material Manufacturing:
- Sintering is particularly valuable for materials that are challenging to process through traditional methods like melting and casting. This includes materials with high melting points or complex compositions. By using sintering, manufacturers can produce components with enhanced strength, hardness, and structural integrity.
-
Sustainability and Waste Reduction:
- Metal sintering is a sustainable process because it generates minimal waste compared to other metalworking techniques. This makes it an environmentally friendly option for producing metal components, aligning with modern sustainability goals.
-
Role in Steel Production:
- In steel manufacturing, sintering is used to produce sintered ore, which serves as clinker for ironmaking. This process involves mixing iron ore powder, non-tobacco coal, and lime in specific ratios. The resulting sintered ore improves blast furnace efficiency by enhancing permeability, reducing the coking ratio, and ensuring smooth furnace operation.
-
Enhancement of Material Properties:
- The sintering process not only bonds metal particles but also closes porous spaces within the material, resulting in a denser and more durable final product. This makes sintered components suitable for high-performance applications where strength and durability are critical.
-
Applications Across Industries:
- Sintering is widely used in various industries, including automotive, aerospace, and electronics, to produce complex and high-strength components. It is also essential in the production of ceramics, refractory materials, and advanced composites.
-
Equipment Used in Sintering:
- The sintering process typically requires specialized equipment such as a sintering furnace. These furnaces are designed to provide precise temperature control and uniform heating, ensuring optimal bonding of metal particles and consistent quality of the final product.
In summary, sintering is a versatile and indispensable process in modern manufacturing, offering numerous benefits such as material efficiency, sustainability, and the ability to produce high-performance components. Its applications span multiple industries, making it a cornerstone of advanced material production.
Summary Table:
Aspect | Key Insights |
---|---|
Definition | A thermal process bonding metal powders below melting points for solid structures. |
Material Benefits | Produces strong, durable, and high-performance components. |
Sustainability | Minimizes waste, aligning with eco-friendly manufacturing goals. |
Steel Production Role | Enhances blast furnace efficiency and reduces operational costs. |
Industry Applications | Widely used in automotive, aerospace, electronics, and ceramics. |
Equipment | Requires specialized sintering furnaces for precise temperature control. |
Learn how sintering can revolutionize your manufacturing process—contact our experts today for more insights!