Calcination temperature plays a critical role in determining the structural, chemical, and physical properties of materials. It influences phase transformations, crystallinity, particle size, porosity, and surface area, which in turn affect the material's performance in various applications. By carefully controlling the calcination temperature, one can optimize the material's properties for specific uses, such as catalysis, energy storage, or ceramics. However, excessively high temperatures can lead to undesirable effects, such as sintering, agglomeration, or phase decomposition. Understanding the influence of calcination temperature is essential for tailoring materials to meet specific functional requirements.
Key Points Explained:
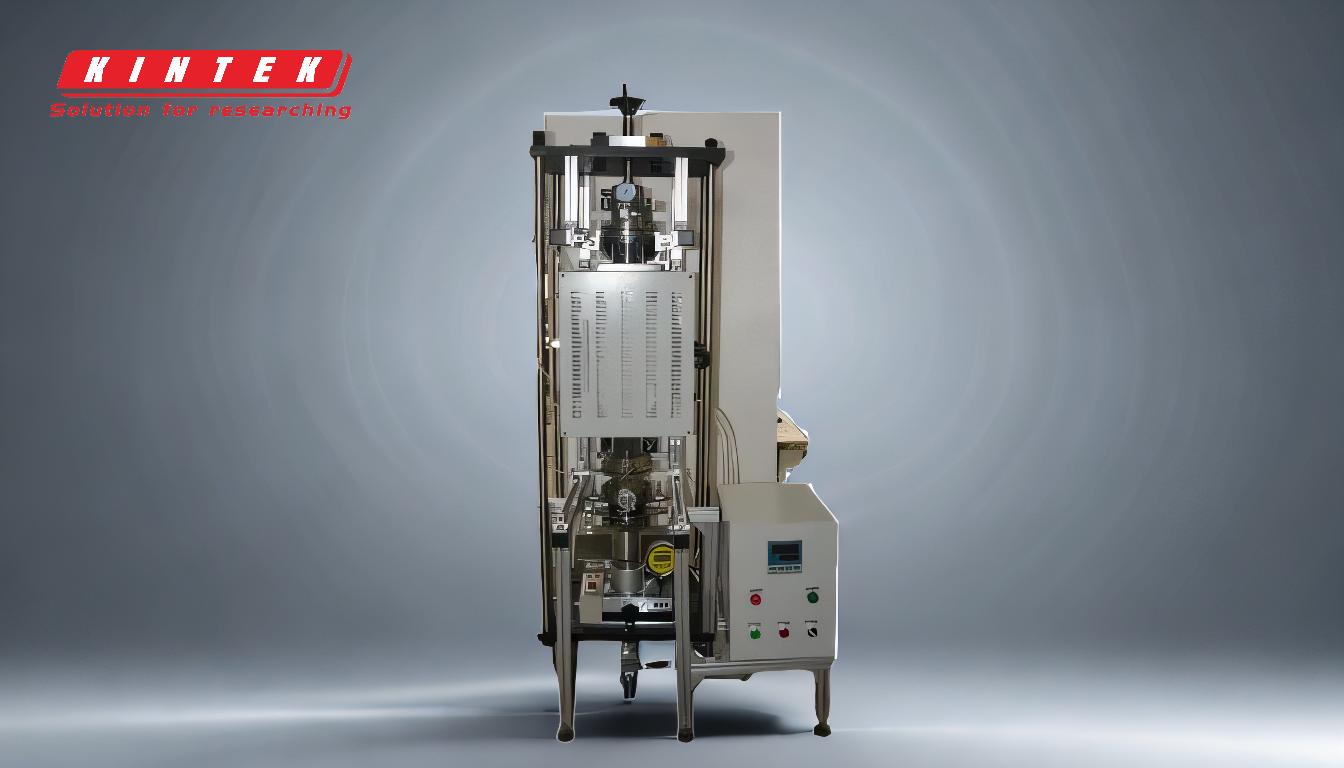
-
Phase Transformation and Crystallinity:
- Explanation: Calcination temperature directly affects the phase composition and crystallinity of materials. At lower temperatures, materials may remain amorphous or partially crystalline. As the temperature increases, phase transitions occur, leading to the formation of more stable crystalline phases. For example, in the production of ceramics, calcination at higher temperatures can promote the formation of desired crystalline phases like alumina or zirconia.
- Impact: Proper control of calcination temperature ensures the formation of the desired phase, which is crucial for achieving optimal mechanical, thermal, and chemical properties.
-
Particle Size and Morphology:
- Explanation: Calcination temperature influences the growth of particles. At moderate temperatures, particles may grow slightly, improving crystallinity without significant agglomeration. However, at excessively high temperatures, particles can sinter or fuse together, leading to larger particle sizes and reduced surface area.
- Impact: Smaller particle sizes and controlled morphology are often desirable for applications like catalysis, where high surface area enhances reactivity. Excessive particle growth can reduce performance.
-
Porosity and Surface Area:
- Explanation: Calcination temperature affects the porosity and surface area of materials. Lower temperatures may preserve a higher surface area and porosity, which is beneficial for applications like adsorption or catalysis. Higher temperatures can cause pore collapse or densification, reducing surface area.
- Impact: Tailoring calcination temperature allows for the optimization of porosity and surface area, which are critical for applications requiring high reactivity or adsorption capacity.
-
Chemical Stability and Decomposition:
- Explanation: Some materials undergo chemical decomposition or phase changes at specific temperatures. For example, metal hydroxides or carbonates decompose into oxides during calcination. The temperature must be carefully controlled to ensure complete decomposition without degrading the material.
- Impact: Proper calcination ensures the formation of stable, high-purity phases, which are essential for applications in electronics, energy storage, or catalysis.
-
Sintering and Agglomeration:
- Explanation: At very high temperatures, sintering can occur, where particles fuse together, reducing surface area and porosity. Agglomeration can also lead to uneven particle size distribution.
- Impact: Sintering and agglomeration can negatively affect material performance, particularly in applications requiring high surface area or uniform particle size.
-
Thermal and Mechanical Properties:
- Explanation: Calcination temperature influences the thermal and mechanical properties of materials. Higher temperatures generally improve mechanical strength and thermal stability but may also introduce brittleness.
- Impact: Understanding the balance between temperature and material properties is essential for applications like refractory materials or structural ceramics.
-
Application-Specific Optimization:
- Explanation: Different applications require different material properties. For example, catalysts may need high surface area and porosity, while structural ceramics require high density and mechanical strength.
- Impact: By adjusting calcination temperature, materials can be optimized for specific applications, ensuring maximum performance and efficiency.
-
Energy Efficiency and Cost Considerations:
- Explanation: Higher calcination temperatures require more energy, increasing production costs. Balancing temperature with desired material properties is essential for cost-effective manufacturing.
- Impact: Optimizing calcination temperature can reduce energy consumption and production costs while still achieving the desired material properties.
By understanding and controlling the influence of calcination temperature, manufacturers and researchers can tailor materials to meet specific functional requirements, ensuring optimal performance in a wide range of applications.
Summary Table:
Aspect | Impact |
---|---|
Phase Transformation | Determines crystallinity and phase stability for desired material properties. |
Particle Size and Morphology | Controls particle growth and surface area for enhanced reactivity or strength. |
Porosity and Surface Area | Optimizes porosity for high reactivity or adsorption capacity. |
Chemical Stability | Ensures complete decomposition without degrading material quality. |
Sintering and Agglomeration | Prevents particle fusion, maintaining uniform size and surface area. |
Thermal and Mechanical Properties | Balances strength, stability, and brittleness for specific applications. |
Application-Specific Optimization | Tailors materials for catalysis, ceramics, or energy storage. |
Energy Efficiency | Reduces energy consumption and production costs while achieving desired properties. |
Need help optimizing calcination temperature for your materials? Contact our experts today!