PVD (Physical Vapor Deposition) coating is a process that involves depositing a thin layer of material onto a substrate at relatively low temperatures compared to other coating methods like Chemical Vapor Deposition (CVD). The low-temperature nature of PVD makes it suitable for heat-sensitive materials, such as plastics and certain metals. The temperature range for PVD coating typically falls between 200°C to 400°C (392°F to 752°F), but it can be as low as 50°F (10°C) for certain substrates like plastics. This wide range allows PVD to be applied to a variety of materials without causing thermal distortion or degradation. The process is known for producing high-purity, uniform, and durable coatings with excellent adhesion, making it a preferred choice for applications requiring high performance and precision.
Key Points Explained:
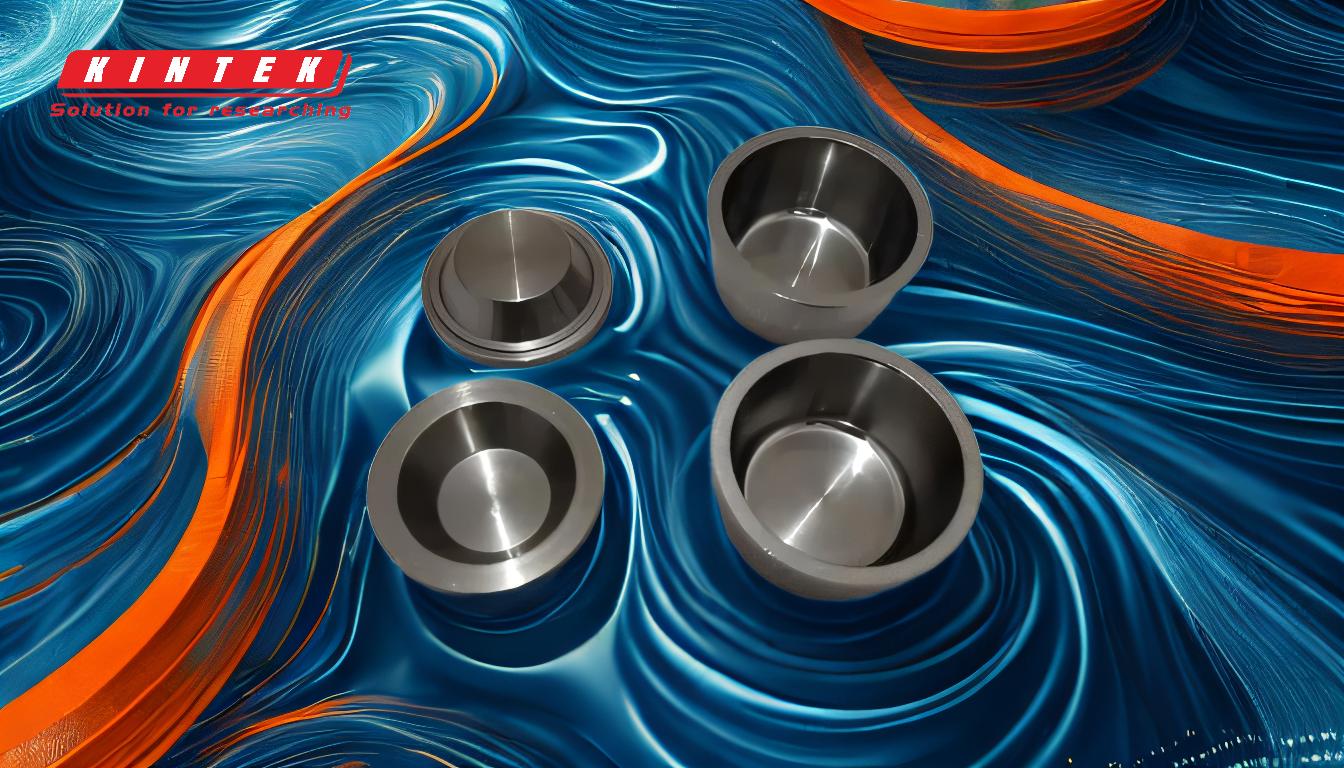
-
Temperature Range for PVD Coating:
- The typical temperature range for PVD coating is between 200°C to 400°C (392°F to 752°F). This range is significantly lower than that of CVD, which often requires temperatures above 800°C (1472°F).
- For heat-sensitive materials like plastics, the temperature can be controlled to as low as 50°F (10°C), ensuring that the substrate does not degrade or distort during the coating process.
-
Why Low Temperature is Important:
- Minimizing Thermal Distortion: High temperatures can cause parts to warp or lose their mechanical properties. PVD’s low-temperature process helps maintain the structural integrity of heat-sensitive materials.
- Suitability for Diverse Materials: The ability to operate at lower temperatures makes PVD suitable for a wide range of substrates, including plastics, zinc, brass, and steel, without compromising their properties.
-
Comparison with Other Coating Methods:
- Chemical Vapor Deposition (CVD): CVD typically requires much higher temperatures, often exceeding 800°C (1472°F), which can limit its use to materials that can withstand such heat.
- Electroplating: While electroplating can be done at lower temperatures, it often results in less durable and less uniform coatings compared to PVD.
-
Advantages of Low-Temperature PVD Coating:
- High Adhesion: The low-temperature process ensures excellent adhesion of the coating to the substrate, preventing issues like flaking or chipping.
- Uniformity and Purity: PVD coatings are known for their high purity and uniformity, which are critical for applications requiring precision and durability.
- Durability: PVD coatings are often harder and more corrosion-resistant than those applied by other methods, making them ideal for high-performance applications.
-
Applications of Low-Temperature PVD Coating:
- Heat-Sensitive Materials: PVD is ideal for coating plastics and other materials that cannot withstand high temperatures.
- Precision Tools: The process is widely used in the manufacturing of precision tools, where maintaining the integrity of the substrate is crucial.
- Aesthetic Finishes: PVD coatings provide a metallic luster without the need for additional polishing, making them popular for decorative applications.
-
Process Considerations:
- Substrate Cleaning: Before coating, the substrate must be thoroughly cleaned to remove any contaminants that could affect adhesion.
- Pretreatment: Some substrates may require pretreatment to enhance coating adhesion, especially for materials with low surface energy like plastics.
- Quality Control: Post-coating quality control ensures that the coating meets the required specifications for thickness, adhesion, and performance.
-
Challenges and Limitations:
- Coating Uniformity on Complex Shapes: While PVD provides excellent coating uniformity on flat surfaces, it can be challenging to achieve uniform coatings on complex geometries, especially on the back and sides of tools.
- Cost: The equipment and process for PVD coating can be more expensive than other coating methods, though the durability and performance of the coatings often justify the cost.
In summary, the low-temperature nature of PVD coating, typically ranging from 200°C to 400°C (or as low as 50°F for plastics), makes it a versatile and effective method for applying durable, high-performance coatings to a wide range of materials. This capability is particularly beneficial for heat-sensitive substrates, where maintaining material integrity is crucial. The process offers numerous advantages, including high adhesion, uniformity, and durability, making it a preferred choice for applications in precision tooling, decorative finishes, and more. However, challenges such as coating uniformity on complex shapes and higher costs must be considered when selecting PVD for specific applications.
Summary Table:
Aspect | Details |
---|---|
Temperature Range | 200°C to 400°C (392°F to 752°F); as low as 50°F (10°C) for plastics |
Key Benefits | High adhesion, uniformity, durability, and suitability for heat-sensitive materials |
Applications | Precision tools, decorative finishes, heat-sensitive materials |
Comparison with CVD | PVD operates at lower temperatures (200°C–400°C) vs. CVD (>800°C) |
Challenges | Uniformity on complex shapes, higher equipment costs |
Learn how PVD coating can enhance your project—contact our experts today!