DC magnetron sputtering is a plasma-based coating technique where a direct current (DC) power source generates a plasma in a low-pressure gas environment, typically argon. The process involves bombarding a target material (usually a metal or ceramic) with high-energy ions, causing atoms to be ejected from the target and deposited onto a substrate. A key feature of this method is the use of a magnetic field, which confines electrons near the target surface, increasing plasma density and sputtering efficiency. The magnetic field also ensures uniform deposition and higher sputtering rates by controlling the motion of charged particles. This technique is widely used for depositing high-quality coatings, particularly with pure metals like iron, copper, and nickel.
Key Points Explained:
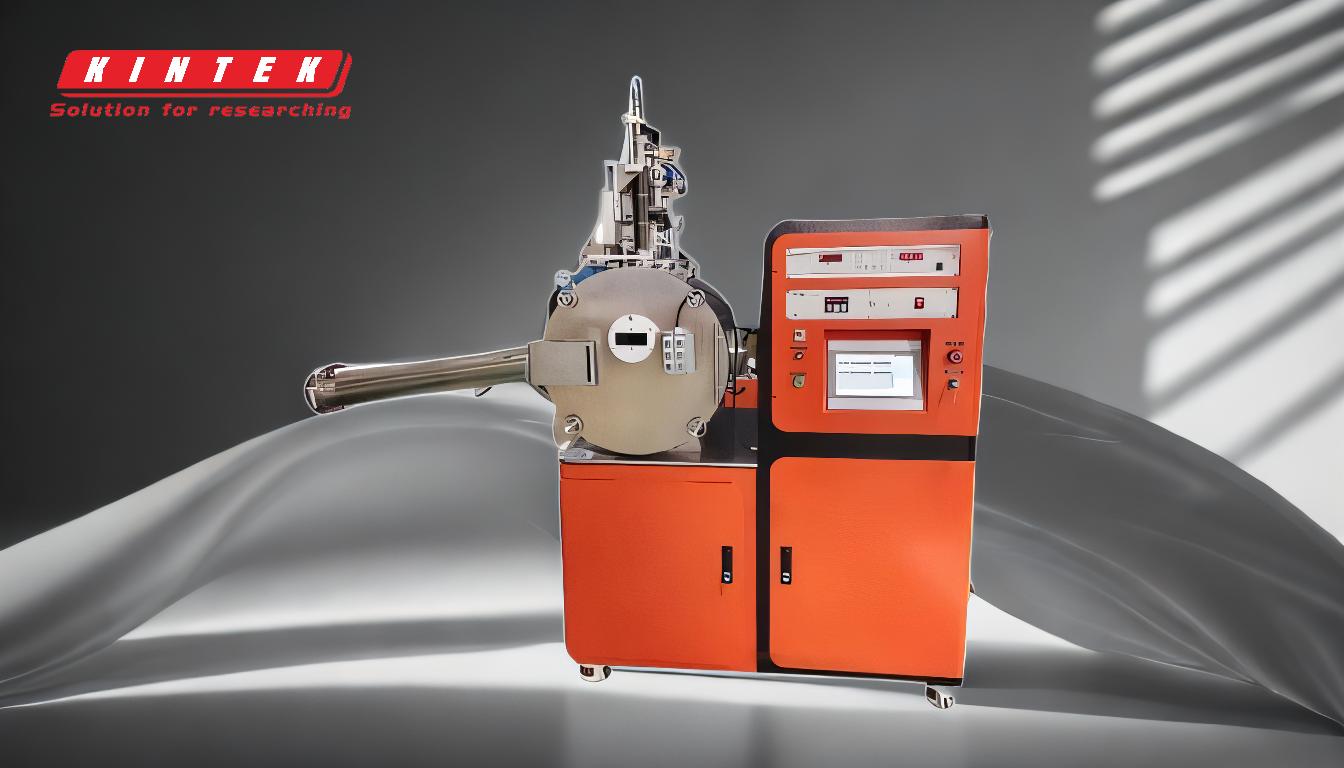
-
DC Magnetron Sputtering Overview:
- DC magnetron sputtering is a physical vapor deposition (PVD) technique used to deposit thin films on substrates.
- It involves a DC power supply to generate a plasma in a low-pressure gas environment, typically argon.
- The process is characterized by the ejection of atoms from a target material due to ion bombardment, followed by deposition onto a substrate.
-
Role of the Magnetic Field:
- The magnetic field is generated by a magnetic assembly near the target and is perpendicular to the electric field.
- It traps electrons near the target surface, increasing their path length and enhancing plasma density.
- This confinement of electrons boosts the ionization of gas atoms, leading to a higher sputtering rate and more efficient deposition.
-
Plasma Generation and Ion Bombardment:
- A high negative voltage is applied to the target, creating a strong electric field.
- Positive argon ions from the plasma are accelerated toward the negatively charged target.
- The kinetic energy of these ions causes atoms to be ejected from the target surface in a process called sputtering.
-
Cycloidal Motion of Charged Particles:
- The magnetic field causes electrons and ions to move in a cycloidal (spiral) path near the target surface.
- This motion increases the likelihood of collisions between electrons and gas atoms, sustaining the plasma and enhancing sputtering efficiency.
-
Advantages of Magnetic Field Confinement:
- Higher plasma density near the target surface results in faster sputtering rates.
- Uniform deposition is achieved due to controlled motion of charged particles.
- Substrate damage is minimized as the magnetic field prevents excessive ion bombardment.
-
Process Parameters:
- Chamber pressure typically ranges from 1 to 100 mTorr.
- The target material is usually a pure metal (e.g., iron, copper, nickel) or ceramic.
- The substrate is placed on the anode, while the target is held by the cathode.
-
Applications:
- DC magnetron sputtering is widely used in industries requiring high-quality thin films, such as semiconductors, optics, and decorative coatings.
- It is particularly suitable for depositing conductive materials due to the use of a DC power source.
-
Glow Discharge Phenomenon:
- The plasma emits a colorful glow, known as a glow discharge, which is a visual indicator of the ionization process.
- This glow consists of electrons (yellow) and gas ions (red), signifying the presence of a stable plasma.
By understanding these key points, equipment and consumable purchasers can better evaluate the suitability of DC magnetron sputtering for their specific applications, ensuring optimal performance and cost-effectiveness.
Summary Table:
Key Aspect | Details |
---|---|
Technique | Physical vapor deposition (PVD) for thin film coating. |
Plasma Generation | DC power source in a low-pressure argon environment. |
Magnetic Field Role | Confines electrons, increases plasma density, and enhances sputtering rates. |
Target Materials | Pure metals (e.g., iron, copper, nickel) or ceramics. |
Applications | Semiconductors, optics, decorative coatings. |
Process Parameters | Chamber pressure: 1–100 mTorr; target on cathode, substrate on anode. |
Discover how DC magnetron sputtering can elevate your thin film processes—contact our experts today!