Depositing extremely controlled thin films involves precise techniques that allow for the creation of ultra-thin layers, often down to the atomic level. The two primary methods for achieving this are Physical Vapor Deposition (PVD) and Chemical Vapor Deposition (CVD). PVD techniques, such as sputtering, involve the physical transfer of material from a target to a substrate, often using plasma generated by inert gases like argon. CVD, on the other hand, relies on chemical reactions to deposit thin films, often at high temperatures. Both methods are highly controllable and can be tailored to specific applications, such as semiconductor manufacturing, flexible solar cells, and OLEDs. Additionally, electrochemical methods and other chemical deposition techniques like sol-gel and spray pyrolysis offer further options for creating thin films with specific properties and morphologies.
Key Points Explained:
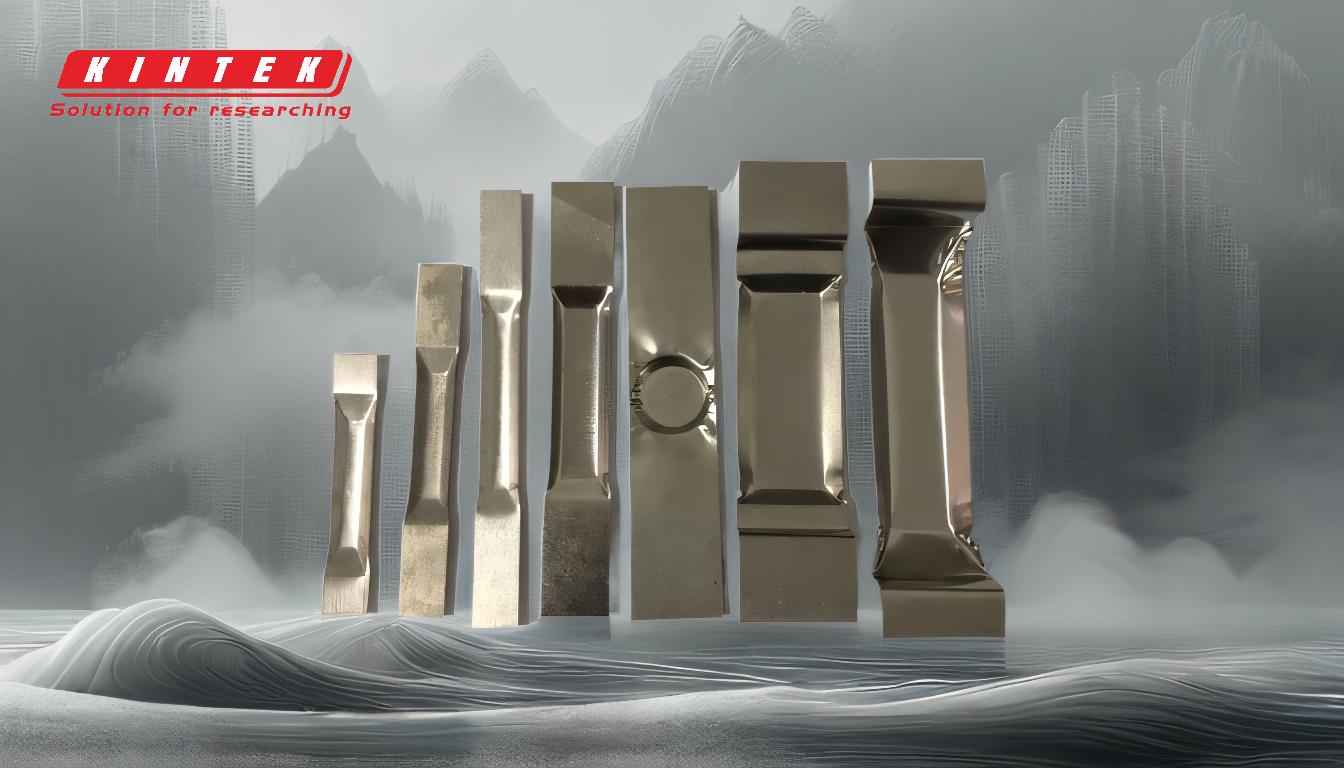
-
Physical Vapor Deposition (PVD):
- Sputtering: This is a common PVD technique where a target material is bombarded with high-energy ions, causing atoms to be ejected and deposited onto a substrate. For example, platinum thin films are often deposited using a DC magnetron sputtering system, which involves a platinum target, argon gas to generate plasma, and a turbo-molecular pump to maintain a vacuum.
- Evaporation: Another PVD method where the target material is heated until it evaporates, and the vapor then condenses on the substrate to form a thin film. This method is often used for metals and can achieve very thin layers.
-
Chemical Vapor Deposition (CVD):
- Process: CVD involves the use of chemical reactions to deposit thin films. A substrate is exposed to volatile precursors, which react or decompose on the surface to form the desired film. This method is widely used in the semiconductor industry for depositing silicon-based films.
- Variants: There are several variants of CVD, including plasma-enhanced CVD (PECVD) and atomic layer deposition (ALD), which offer even greater control over film thickness and composition.
-
Electrochemical Deposition:
- Techniques: This method involves the use of electrochemical reactions to deposit thin films. Techniques such as pulse potentiostatic and cyclic voltammetry are used to control the deposition process. For example, platinum thin films can be deposited using a computer-controlled electrochemical analyzer, with a platinum counter electrode and an Ag/AgCl reference electrode.
- Applications: Electrochemical deposition is particularly useful for creating films with specific electrical properties, such as those used in sensors and electronic devices.
-
Chemical Deposition Methods:
- Sol-Gel: This method involves the formation of a thin film from a solution or gel-like material, which is then dried to form the final film. It is often used for creating oxide films.
- Spray Pyrolysis: In this technique, a solution is sprayed onto a heated substrate, where it decomposes to form a thin film. This method is useful for creating films with complex compositions.
- Chemical Bath Deposition: This involves submerging the substrate in a chemical bath, where a reaction occurs to deposit the film. It is a simple and cost-effective method for creating thin films.
- Chemical Vapor Evaporation: This method uses thermally induced chemical reactions to deposit thin films. It is often used for creating films with high purity and uniformity.
-
Characterization Techniques:
- X-ray Diffraction (XRD): Used to analyze the crystal structure of the deposited films.
- Scanning Electron Microscopy (SEM): Provides detailed images of the film's surface morphology.
- Atomic Force Microscopy (AFM): Offers high-resolution images of the film's surface at the atomic level.
-
Applications:
- Semiconductors: Thin films are crucial in the manufacture of semiconductor devices, where precise control over film thickness and composition is essential.
- Flexible Electronics: Thin films are used in flexible solar cells and OLEDs, where they provide the necessary electrical and optical properties.
- Sensors: Electrochemically deposited thin films are used in various sensors, where they provide the necessary sensitivity and selectivity.
By understanding these key points, one can appreciate the complexity and precision required in depositing extremely controlled thin films. Each method has its own advantages and is chosen based on the specific requirements of the application.
Summary Table:
Method | Key Techniques | Applications |
---|---|---|
Physical Vapor Deposition (PVD) | Sputtering, Evaporation | Semiconductor manufacturing, metal thin films |
Chemical Vapor Deposition (CVD) | Plasma-enhanced CVD (PECVD), Atomic Layer Deposition (ALD) | Silicon-based films, high-purity coatings |
Electrochemical Deposition | Pulse potentiostatic, Cyclic voltammetry | Sensors, electronic devices |
Chemical Deposition Methods | Sol-Gel, Spray Pyrolysis, Chemical Bath Deposition, Chemical Vapor Evaporation | Oxide films, complex compositions, cost-effective solutions |
Characterization Techniques | XRD, SEM, AFM | Crystal structure analysis, surface morphology, atomic-level imaging |
Need precise thin film deposition solutions? Contact our experts today to discuss your requirements!