Rubber molding is a versatile manufacturing process used to shape uncured rubber into functional products by heating and reshaping it in a metal cavity. The three primary types of rubber molding are injection molding, compression molding, and transfer molding, each with its own unique approach and applications. These processes are part of a broader rubber manufacturing workflow that includes compounding, extrusion, calendering, vulcanization, latex processing, and polyurethane production. Understanding the specific steps and techniques involved in rubber molding is essential for producing high-quality rubber products tailored to various industries.
Key Points Explained:
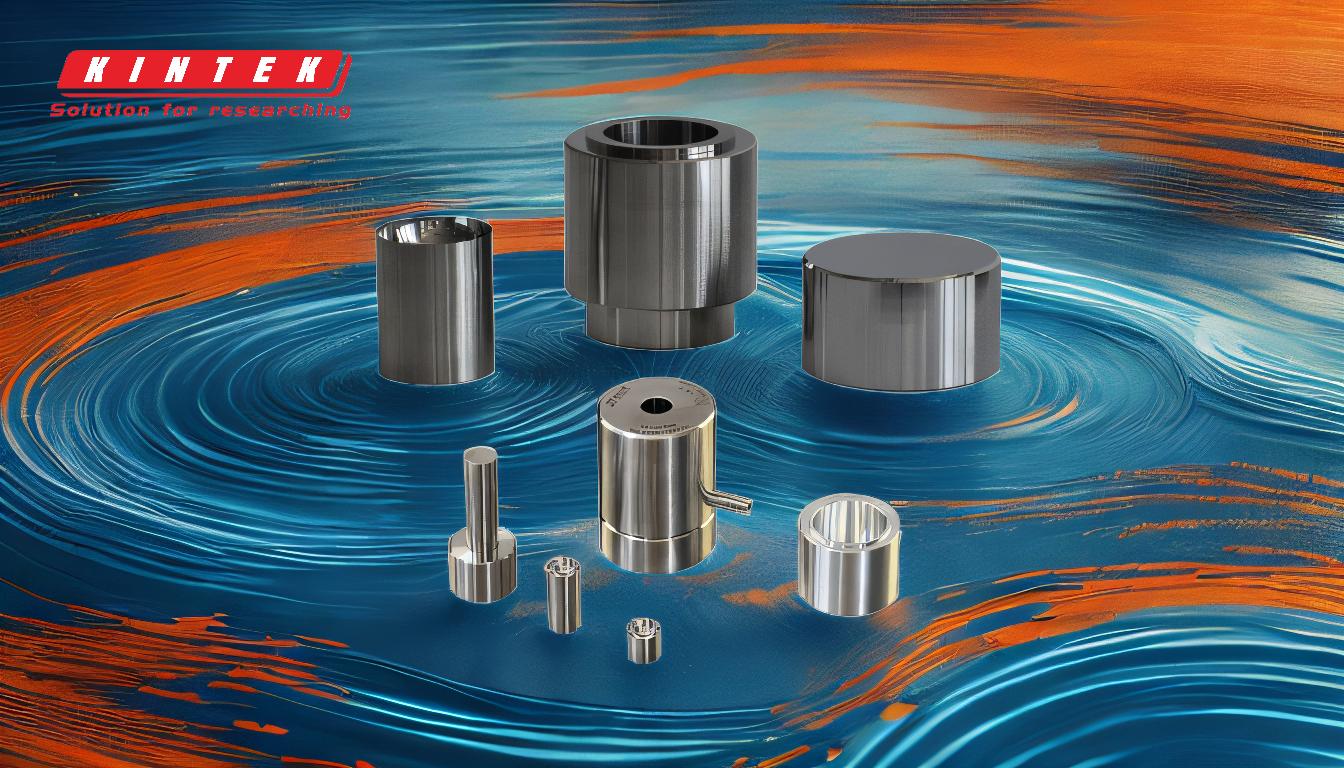
-
Overview of Rubber Molding
- Rubber molding is a process that transforms uncured rubber into usable products by heating and shaping it in a metal mold.
- It is one of several methods for manufacturing rubber products, alongside extrusion, die-cut sheet rolling, open vulcanization, and continuous vulcanization.
- The process is widely used in industries such as automotive, aerospace, medical, and consumer goods due to its ability to produce durable, flexible, and precise components.
-
Types of Rubber Molding Processes
-
Injection Molding:
- Uncured rubber is injected into a heated mold cavity under high pressure.
- Ideal for high-volume production of complex shapes with tight tolerances.
- Commonly used for seals, gaskets, and O-rings.
-
Compression Molding:
- Pre-measured rubber is placed into an open mold cavity, which is then closed and heated under pressure.
- Suitable for large, simple parts and low to medium production volumes.
- Often used for automotive components like bushings and mounts.
-
Transfer Molding:
- Rubber is transferred from a chamber into a closed mold cavity using a plunger.
- Combines elements of both injection and compression molding, offering a balance of precision and simplicity.
- Frequently used for intricate parts requiring consistent material distribution.
-
Injection Molding:
-
Key Steps in the Rubber Molding Process
-
Material Preparation:
- Rubber compounds are prepared by mixing raw rubber with additives like fillers, plasticizers, and curing agents.
- This step ensures the material has the desired properties, such as elasticity, strength, and resistance to heat or chemicals.
-
Mold Design and Preparation:
- Molds are custom-designed based on the product's specifications.
- They are typically made from durable materials like steel or aluminum to withstand high temperatures and pressures.
-
Molding Process:
- The chosen molding method (injection, compression, or transfer) is employed to shape the rubber.
- Heat and pressure are applied to cure the rubber, solidifying it into the desired form.
-
Post-Processing:
- After molding, the rubber product may undergo additional steps like trimming, surface finishing, or quality inspection.
- These steps ensure the product meets the required specifications and performance standards.
-
Material Preparation:
-
Advantages of Rubber Molding
- Versatility: Can produce a wide range of shapes, sizes, and complexities.
- Durability: Rubber products are resistant to wear, tear, and environmental factors.
- Cost-Effectiveness: Suitable for both high-volume and low-volume production, depending on the method used.
- Precision: Ensures consistent quality and tight tolerances, especially with injection molding.
-
Applications of Rubber Molding
- Automotive: Seals, gaskets, vibration dampers, and hoses.
- Medical: Syringe stoppers, seals, and medical device components.
- Consumer Goods: Footwear, grips, and protective covers.
- Industrial: Gaskets, seals, and vibration isolation components.
By understanding the manufacturing process of rubber molding, including its types, steps, and applications, purchasers of equipment and consumables can make informed decisions about the best methods and materials for their specific needs. This knowledge ensures the production of high-quality rubber products that meet industry standards and performance requirements.
Summary Table:
Aspect | Details |
---|---|
Types of Molding | Injection, Compression, Transfer |
Key Steps | Material Prep, Mold Design, Molding Process, Post-Processing |
Advantages | Versatility, Durability, Cost-Effectiveness, Precision |
Applications | Automotive, Medical, Consumer Goods, Industrial |
Discover how rubber molding can meet your production needs—contact our experts today!