The maximum permissible temperature for hydraulic oil used in stationary hydraulic systems is a critical factor in ensuring the efficiency, longevity, and safety of the system. Generally, the maximum operating temperature for hydraulic oil should not exceed 82°C (180°F). However, this can vary depending on the type of hydraulic oil, the system design, and the specific application. Exceeding this temperature can lead to accelerated oil degradation, reduced lubrication properties, and potential system failure. It is essential to monitor and control the temperature within the recommended range to maintain optimal performance and prevent damage to the hydraulic components.
Key Points Explained:
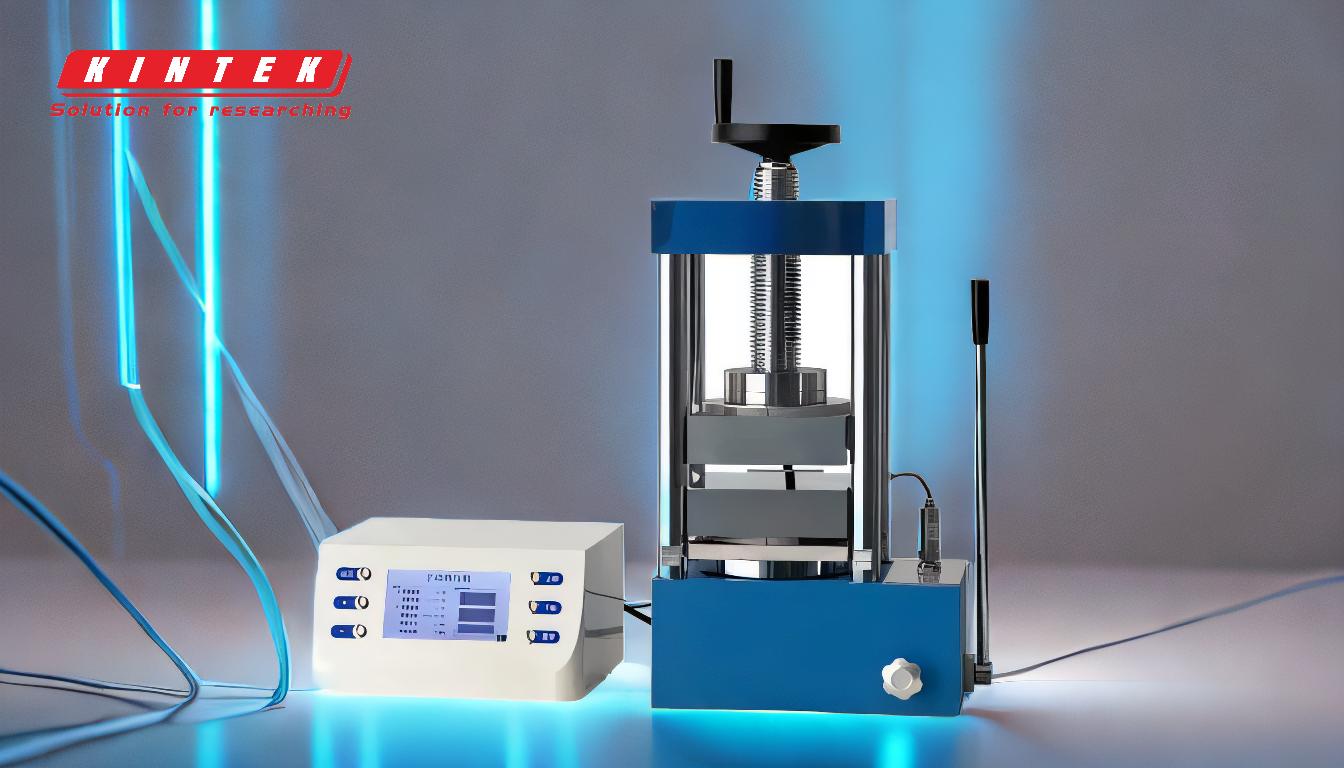
-
Recommended Maximum Temperature:
- The widely accepted maximum permissible temperature for hydraulic oil in stationary systems is 82°C (180°F). This is based on industry standards and ensures that the oil maintains its viscosity, lubrication properties, and chemical stability.
- Exceeding this temperature can cause the oil to oxidize, leading to the formation of sludge, varnish, and acids, which can damage system components.
-
Factors Influencing Maximum Temperature:
- Oil Type: Different hydraulic oils have varying thermal stability. For example, synthetic oils can often withstand higher temperatures compared to mineral-based oils.
- System Design: The efficiency of heat dissipation in the system, including the presence of coolers or heat exchangers, plays a significant role in determining the maximum permissible temperature.
- Operating Conditions: High ambient temperatures, continuous operation, and heavy loads can increase the oil temperature, requiring more stringent temperature control measures.
-
Consequences of Exceeding Maximum Temperature:
- Oil Degradation: High temperatures accelerate the breakdown of the oil's molecular structure, reducing its effectiveness as a lubricant and hydraulic medium.
- Component Wear: Increased temperatures can cause seals and hoses to harden and crack, leading to leaks and potential system failure.
- Reduced Efficiency: As the oil's viscosity decreases at higher temperatures, the system's hydraulic efficiency drops, resulting in poor performance and increased energy consumption.
-
Temperature Monitoring and Control:
- Thermal Sensors: Installing temperature sensors in the hydraulic system allows for real-time monitoring and early detection of overheating.
- Cooling Systems: Incorporating heat exchangers or coolers helps maintain the oil temperature within the safe operating range.
- Regular Maintenance: Periodic oil analysis and system inspections can identify potential issues before they lead to overheating.
-
Best Practices for Temperature Management:
- Use hydraulic oils with high thermal stability and oxidation resistance.
- Ensure proper system design with adequate cooling mechanisms.
- Avoid overloading the system and operate within the recommended load limits.
- Regularly check and replace worn-out components that could contribute to heat generation.
By adhering to these guidelines, you can ensure that your stationary hydraulic system operates efficiently and reliably, minimizing the risk of overheating and prolonging the lifespan of both the oil and the system components.
Summary Table:
Key Aspect | Details |
---|---|
Max Permissible Temperature | 82°C (180°F) |
Factors Influencing Temp | Oil type, system design, operating conditions |
Consequences of Overheating | Oil degradation, component wear, reduced system efficiency |
Monitoring & Control | Thermal sensors, cooling systems, regular maintenance |
Best Practices | Use high-stability oils, ensure proper cooling, avoid overloading systems |
Ensure your hydraulic system operates at peak efficiency—contact our experts today for tailored advice!