The sputtering process is a physical vapor deposition (PVD) technique used to deposit thin films of material onto a substrate. It involves creating a plasma in a vacuum chamber by ionizing an inert gas, typically argon. Positively charged ions from the plasma are accelerated toward a negatively charged target material, causing atoms to be ejected from the target's surface. These ejected atoms travel through the chamber and deposit onto the substrate, forming a thin film. The process is highly controlled and precise, making it suitable for applications requiring high accuracy, such as semiconductor manufacturing and optical coatings.
Key Points Explained:
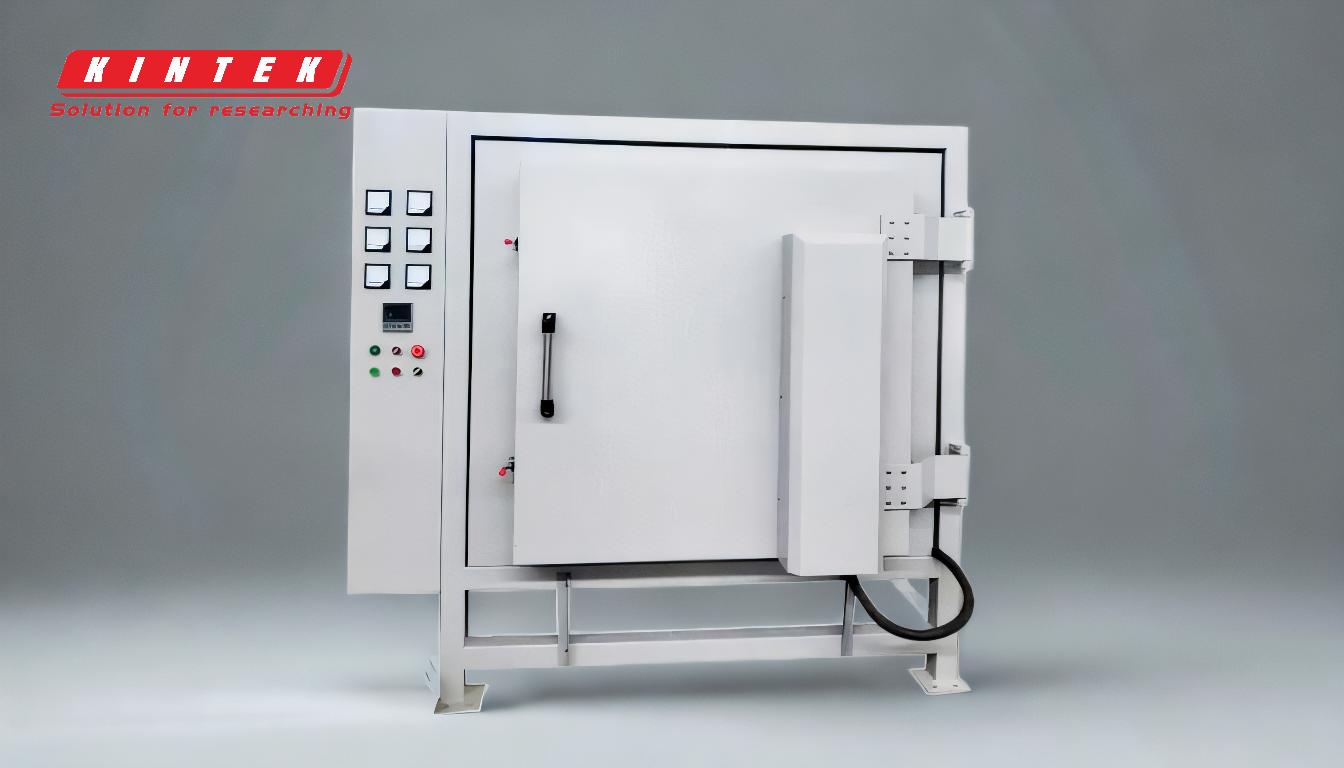
-
Vacuum Chamber Setup:
- The sputtering process takes place in a vacuum chamber to minimize contamination and ensure a controlled environment.
- The target material (source) and the substrate (destination) are placed inside the chamber.
- A voltage is applied between the target (cathode) and the substrate (anode), creating an electric field.
-
Plasma Creation:
- An inert gas, typically argon, is introduced into the vacuum chamber.
- The gas is ionized to create a plasma, a state of matter consisting of free electrons and positively charged ions.
- Ionization occurs when free electrons from the target collide with argon atoms, stripping them of electrons and creating positively charged argon ions.
-
Ion Bombardment:
- The positively charged argon ions are accelerated toward the negatively charged target material due to the electric field.
- When these ions strike the target, they transfer their kinetic energy to the target atoms, causing them to be ejected from the surface. This phenomenon is known as sputtering.
-
Ejection of Target Atoms:
- The energy from the ion bombardment is sufficient to dislodge atoms or molecules from the target material.
- These ejected atoms enter the gaseous state and form a vapor stream within the chamber.
-
Deposition on Substrate:
- The sputtered atoms travel through the chamber and deposit onto the substrate.
- The atoms adhere to the substrate surface, forming a thin film through condensation.
- The deposition process is line-of-sight, meaning the atoms travel in straight paths from the target to the substrate.
-
Advantages of Sputtering:
- Precision: The process allows for highly accurate and uniform thin film deposition.
- Versatility: It can be used with a wide range of materials, including metals, semiconductors, and insulators.
- Control: Parameters such as gas pressure, voltage, and target composition can be adjusted to tailor the film properties.
-
Applications:
- Semiconductors: Sputtering is widely used in the fabrication of integrated circuits and microelectronics.
- Optical Coatings: It is employed to create anti-reflective, reflective, and protective coatings on lenses and mirrors.
- Magnetic Storage: The process is used to deposit thin films for hard disk drives and other magnetic storage devices.
By understanding these key points, one can appreciate the intricate mechanism of the sputtering process and its significance in modern manufacturing and technology.
Summary Table:
Key Aspect | Details |
---|---|
Process | Physical vapor deposition (PVD) technique using plasma and ion bombardment. |
Environment | Vacuum chamber to minimize contamination and ensure precision. |
Plasma Creation | Ionization of inert gas (argon) to create positively charged ions. |
Ion Bombardment | Positively charged ions eject atoms from the target material. |
Deposition | Ejected atoms form a thin film on the substrate. |
Advantages | High precision, versatility, and control over film properties. |
Applications | Semiconductors, optical coatings, and magnetic storage devices. |
Discover how the sputtering process can enhance your manufacturing—contact our experts today!