Coatings are essential for wear resistance as they protect materials and components from mechanical damage, extending their lifespan and reducing costs. By applying a thin layer of coating, materials gain enhanced surface properties such as increased hardness, improved wear resistance, and better performance under harsh conditions. This is particularly important in industries like automotive and aerospace, where components are subjected to extreme wear and tear. Coatings also allow for the reuse of existing parts, minimizing the need for new fabrication and addressing material scarcity. Overall, coatings are a cost-effective and efficient solution to improve durability and operational efficiency.
Key Points Explained:
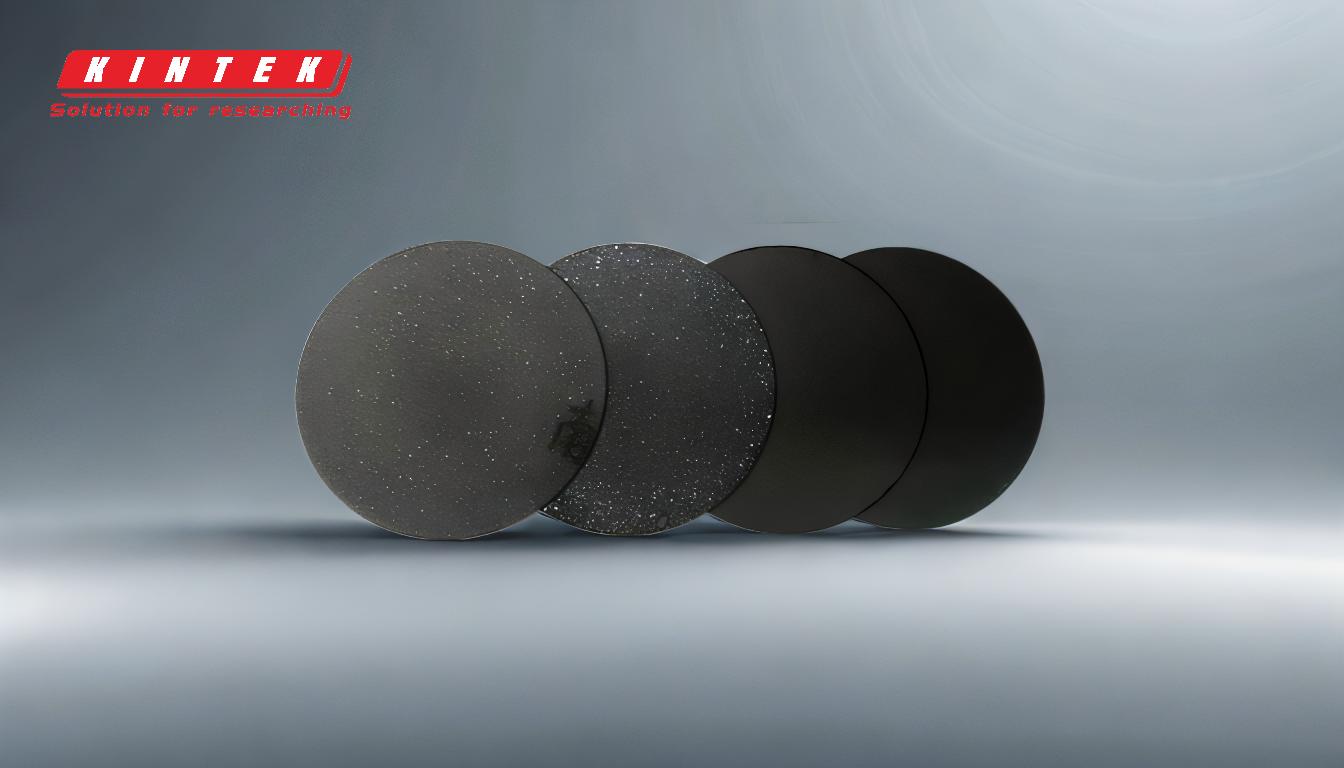
-
Protection Against Mechanical Damage:
- Coatings act as a protective barrier, shielding the underlying material from wear and tear caused by friction, abrasion, and impact. This is crucial for components exposed to harsh operating conditions, such as cutting tools, engine parts, and industrial machinery.
- By reducing direct contact between surfaces, coatings minimize material loss and deformation, ensuring longer operational life.
-
Enhanced Surface Hardness:
- Coatings often increase the surface hardness of materials, making them more resistant to scratches, dents, and other forms of mechanical damage. This is achieved through materials like diamond-like carbon (DLC), titanium nitride (TiN), or ceramic coatings.
- Increased hardness directly correlates with improved wear resistance, as harder surfaces are less prone to deformation under stress.
-
Cost Efficiency and Sustainability:
- Applying coatings to existing parts reduces the need for frequent replacements, lowering material and production costs. This is especially beneficial in industries where high-performance materials are expensive or scarce.
- Coatings are typically only micrometers thick, meaning they use minimal material while providing significant functional benefits, contributing to sustainability efforts.
-
Extended Tool and Component Life:
- In manufacturing, coatings on cutting tools and machinery components significantly extend their lifespan by reducing wear. This leads to fewer interruptions in production and lower maintenance costs.
- For example, coated cutting tools can operate at higher speeds and temperatures without degrading, improving efficiency and output quality.
-
Industry-Specific Applications:
- Automotive Industry: Coatings improve wear resistance in engine components, brake systems, and transmission parts, ensuring reliability and performance under demanding conditions.
- Aerospace Industry: Coatings reduce wear on aircraft components, such as turbine blades and landing gear, while also providing additional benefits like corrosion resistance and fuel efficiency.
- General Manufacturing: Coatings are used on molds, dies, and other tools to withstand repetitive use and harsh environments.
-
Functional and Aesthetic Benefits:
- Beyond wear resistance, coatings can modify surface texture, improve thermal or electrical insulation, and enhance wettability or hydrophobicity. These properties can be tailored to specific applications, adding both functional and aesthetic value.
- For instance, decorative coatings in the automotive industry not only protect against wear but also enhance the visual appeal of vehicles.
-
Reduction in Material Scarcity:
- By extending the life of existing components, coatings reduce the demand for raw materials, addressing issues of material scarcity and promoting resource conservation.
- This is particularly important for industries reliant on rare or expensive materials, such as aerospace and high-tech manufacturing.
In summary, coatings are indispensable for wear resistance due to their ability to protect, harden, and extend the life of materials and components. They offer a cost-effective, sustainable, and versatile solution to combat wear and tear, making them a critical technology across various industries.
Summary Table:
Key Benefits of Coatings | Details |
---|---|
Protection Against Mechanical Damage | Shields materials from friction, abrasion, and impact, ensuring longer operational life. |
Enhanced Surface Hardness | Increases resistance to scratches and dents using materials like DLC, TiN, or ceramics. |
Cost Efficiency and Sustainability | Reduces replacement needs, lowers costs, and promotes sustainability. |
Extended Tool and Component Life | Improves lifespan of cutting tools and machinery, reducing maintenance costs. |
Industry-Specific Applications | Used in automotive, aerospace, and manufacturing for wear resistance and performance. |
Functional and Aesthetic Benefits | Adds surface texture, insulation, and visual appeal. |
Reduction in Material Scarcity | Extends component life, reducing demand for raw materials. |
Learn how coatings can enhance your industry’s efficiency—contact us today!