The objective of Physical Vapor Deposition (PVD) is to create thin, durable, and high-performance coatings on various substrates through a vacuum-based process. PVD enhances the properties of materials, such as corrosion resistance, wear resistance, UV resistance, and chemical resistance, while also providing aesthetic benefits. It is widely used in industries like semiconductors, optics, medical devices, and protective coatings, offering an environmentally friendly solution without harmful byproducts.
Key Points Explained:
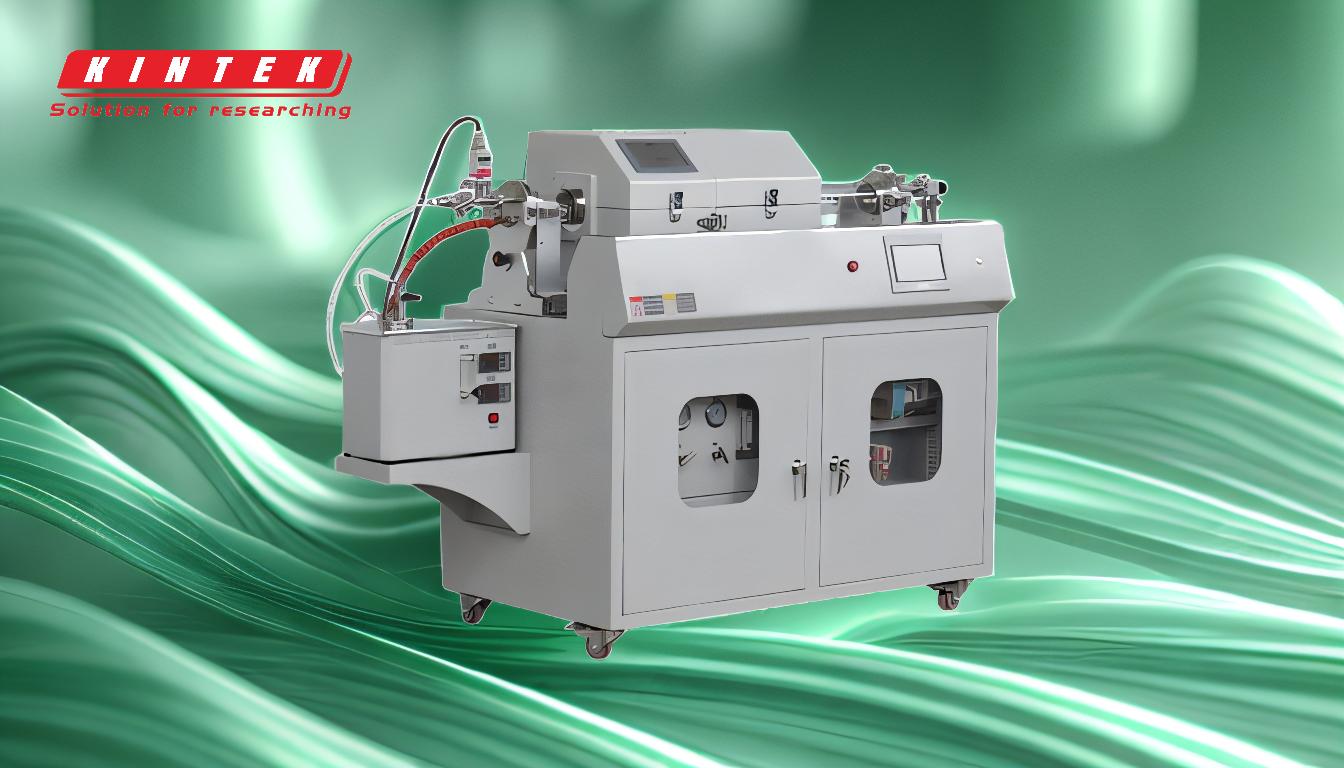
-
Enhancing Material Performance:
- PVD is primarily used to improve the performance of materials by depositing thin, durable coatings. These coatings can enhance properties such as:
- Corrosion Resistance: Protects substrates from environmental degradation.
- Wear Resistance: Increases the lifespan of components subjected to friction.
- UV Resistance: Prevents damage from ultraviolet light exposure.
- Chemical Resistance: Shields materials from chemical reactions or erosion.
- PVD is primarily used to improve the performance of materials by depositing thin, durable coatings. These coatings can enhance properties such as:
-
Creating Thin, Durable Coatings:
- PVD involves vaporizing a solid material in a vacuum and depositing it onto a substrate. This process results in:
- Thin Films: Typically ranging from nanometers to micrometers in thickness.
- Durability: The coatings are highly adherent and resistant to peeling or flaking.
- Precision: Allows for controlled deposition of pure materials or alloys with specific properties.
- PVD involves vaporizing a solid material in a vacuum and depositing it onto a substrate. This process results in:
-
Applications Across Industries:
- PVD is versatile and used in various industries, including:
- Semiconductors: For creating microchips and solar panels.
- Optics: For coating lenses to improve clarity and durability.
- Medical Devices: For enhancing biocompatibility and wear resistance.
- Protective Coatings: For tools, automotive parts, and decorative finishes.
- PVD is versatile and used in various industries, including:
-
Environmentally Friendly Process:
- PVD is considered eco-friendly because:
- No Harmful Byproducts: The process does not produce toxic chemicals or waste.
- Energy Efficiency: It operates in a vacuum, minimizing energy loss.
- Sustainability: Reduces the need for frequent replacements due to enhanced durability.
- PVD is considered eco-friendly because:
-
Aesthetic and Functional Benefits:
- PVD coatings offer both functional and decorative advantages:
- Aesthetic Appeal: Provides a range of colors and finishes for decorative purposes.
- Functional Performance: Combines beauty with enhanced material properties.
- PVD coatings offer both functional and decorative advantages:
-
No Chemical Reactions Involved:
- PVD is a purely physical process, meaning:
- Material Purity: The deposited material retains its original composition.
- Controlled Deposition: Allows for precise control over coating thickness and properties.
- PVD is a purely physical process, meaning:
By achieving these objectives, PVD serves as a critical technology for advancing material science and meeting the demands of modern industries.
Summary Table:
Key Aspect | Details |
---|---|
Material Performance | Enhances corrosion, wear, UV, and chemical resistance. |
Coating Characteristics | Thin films (nanometers to micrometers), durable, and precise. |
Applications | Semiconductors, optics, medical devices, protective coatings. |
Environmental Benefits | No harmful byproducts, energy-efficient, and sustainable. |
Aesthetic & Functional | Offers decorative finishes and enhanced material properties. |
Process | Purely physical, ensuring material purity and controlled deposition. |
Learn how PVD can transform your materials—contact our experts today for tailored solutions!