Sintering is a critical process in manufacturing that transforms powdered materials into dense, strong, and durable components. Its primary objective is to bond particles together under high temperatures (below the melting point) and sometimes pressure, resulting in improved mechanical properties, reduced porosity, and enhanced strength. This process is widely used in industries such as metalworking, ceramics, and glass production, offering advantages like energy efficiency, material consistency, and the ability to create complex shapes. Sintering also allows for precise control over material properties, making it a versatile and environmentally friendly manufacturing technique.
Key Points Explained:
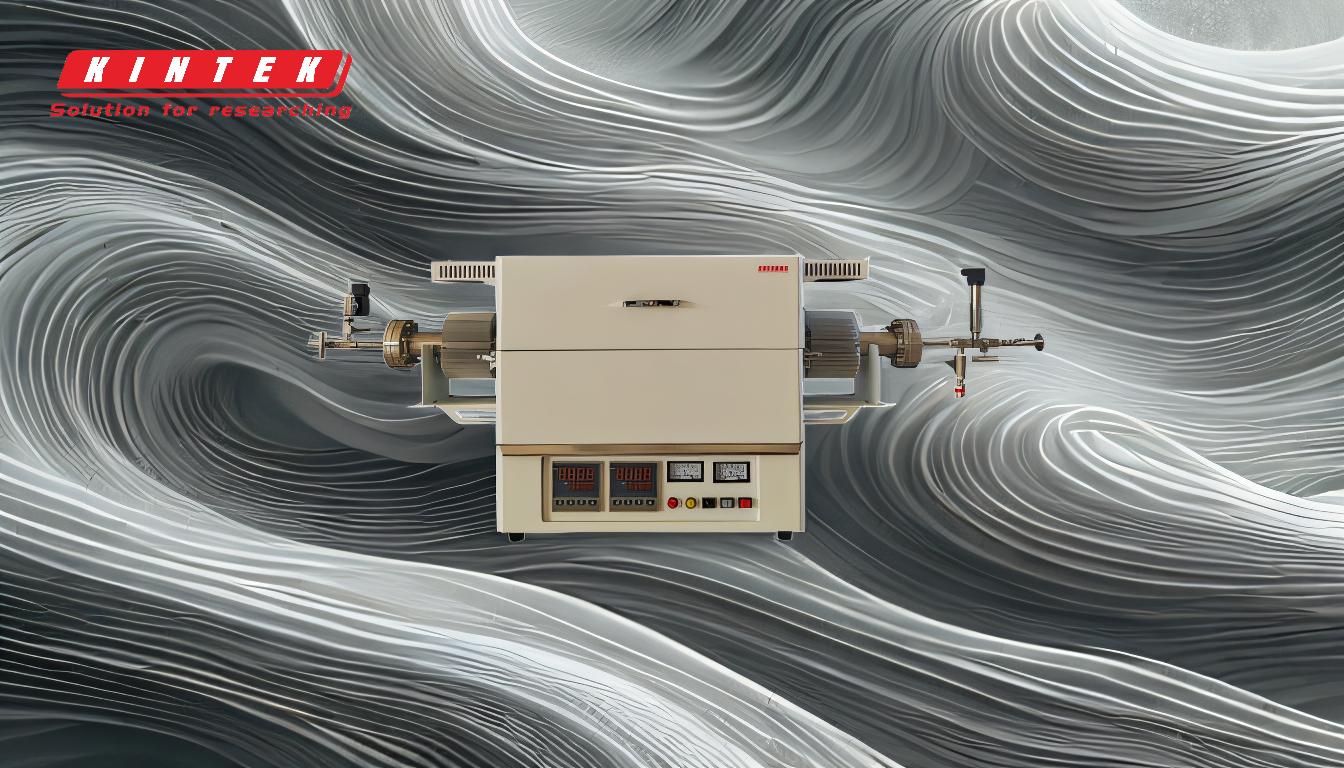
-
Transformation of Powdered Material into a Dense Body
- Sintering converts loose powdered materials (e.g., metal, ceramic, or glass powders) into a solid, dense structure.
- This is achieved by heating the material below its melting point, allowing particles to bond through diffusion and atomic rearrangement.
- The process eliminates pores and reduces voids, resulting in a more compact and uniform material.
-
Improvement of Mechanical Properties
- Sintering enhances the strength, durability, and hardness of materials by minimizing porosity and creating strong inter-particle bonds.
- It allows for the production of components with consistent mechanical properties, which is crucial for high-performance applications.
- The process can be fine-tuned to achieve specific material characteristics, such as increased wear resistance or improved toughness.
-
Energy Efficiency and Environmental Benefits
- Sintering requires less energy compared to melting and casting processes, as it operates at temperatures below the material's melting point.
- This makes it a more sustainable and cost-effective manufacturing method.
- The reduced energy consumption also contributes to lower greenhouse gas emissions, aligning with environmentally friendly production practices.
-
Versatility Across Industries
- Sintering is used in a wide range of industries, including automotive, aerospace, electronics, and construction.
- It enables the production of complex shapes and high-tech materials, such as porous metals, magnetic components, and structural steel parts.
- The process is compatible with various materials, including metals, ceramics, and composites, making it highly adaptable.
-
Control Over Material Properties and Dimensions
- Sintering allows manufacturers to control the final dimensions of a part by accounting for minor shrinkage during the process.
- The cooling rate can be adjusted to fine-tune the material's microstructure and properties, such as hardness or ductility.
- This precision ensures that the final product meets specific design and performance requirements.
-
Cost-Effectiveness and Flexibility
- Sintering is a cost-effective alternative to traditional manufacturing methods like casting, forging, and extrusion.
- It eliminates the need for solid-liquid phase changes, reducing material waste and production costs.
- The process is highly flexible, enabling the creation of components that would otherwise be difficult or impossible to produce using conventional techniques.
-
Applications in High-Performance Components
- Sintering is used to manufacture critical components such as gears, bearings, rotors, and electrical contacts.
- These parts benefit from the enhanced strength, durability, and consistency achieved through sintering.
- The process is also essential for producing advanced materials like structural steel parts and magnetic alloys.
-
Bonding Without Melting
- Unlike melting, sintering bonds particles together without liquefying the material.
- This preserves the material's original properties while improving its structural integrity.
- The absence of melting also reduces the risk of defects, such as cracks or voids, in the final product.
In summary, sintering is a versatile and efficient manufacturing process that transforms powdered materials into high-performance components. Its objectives include improving mechanical properties, reducing porosity, and enabling precise control over material characteristics. By offering energy efficiency, cost-effectiveness, and flexibility, sintering plays a vital role in modern manufacturing across various industries.
Summary Table:
Key Aspect | Description |
---|---|
Process | Bonds particles under high temperatures (below melting point) to create dense, strong components. |
Mechanical Properties | Enhances strength, durability, and hardness by reducing porosity and improving bonds. |
Energy Efficiency | Requires less energy than melting, making it sustainable and cost-effective. |
Versatility | Used in automotive, aerospace, electronics, and more for complex shapes and materials. |
Material Control | Allows precise control over dimensions, microstructure, and material properties. |
Applications | Produces gears, bearings, rotors, and advanced materials like magnetic alloys. |
Transform your manufacturing process with sintering—contact our experts today to learn more!