Hot Isostatic Pressing (HIP) is a manufacturing process that uses high temperature and pressure to improve the properties of materials, particularly metals and ceramics. It involves placing materials in a sealed container filled with an inert gas, which is then subjected to equal pressure on all surfaces. This process enhances material density, mechanical properties, and bonding between particles. HIP is widely used in industries requiring high-performance materials, such as aerospace, automotive, and medical devices. The process can be categorized into wet-bag and dry-bag methods, depending on the setup. Additionally, warm isostatic pressing is a variation that uses heated liquid media for precise temperature control.
Key Points Explained:
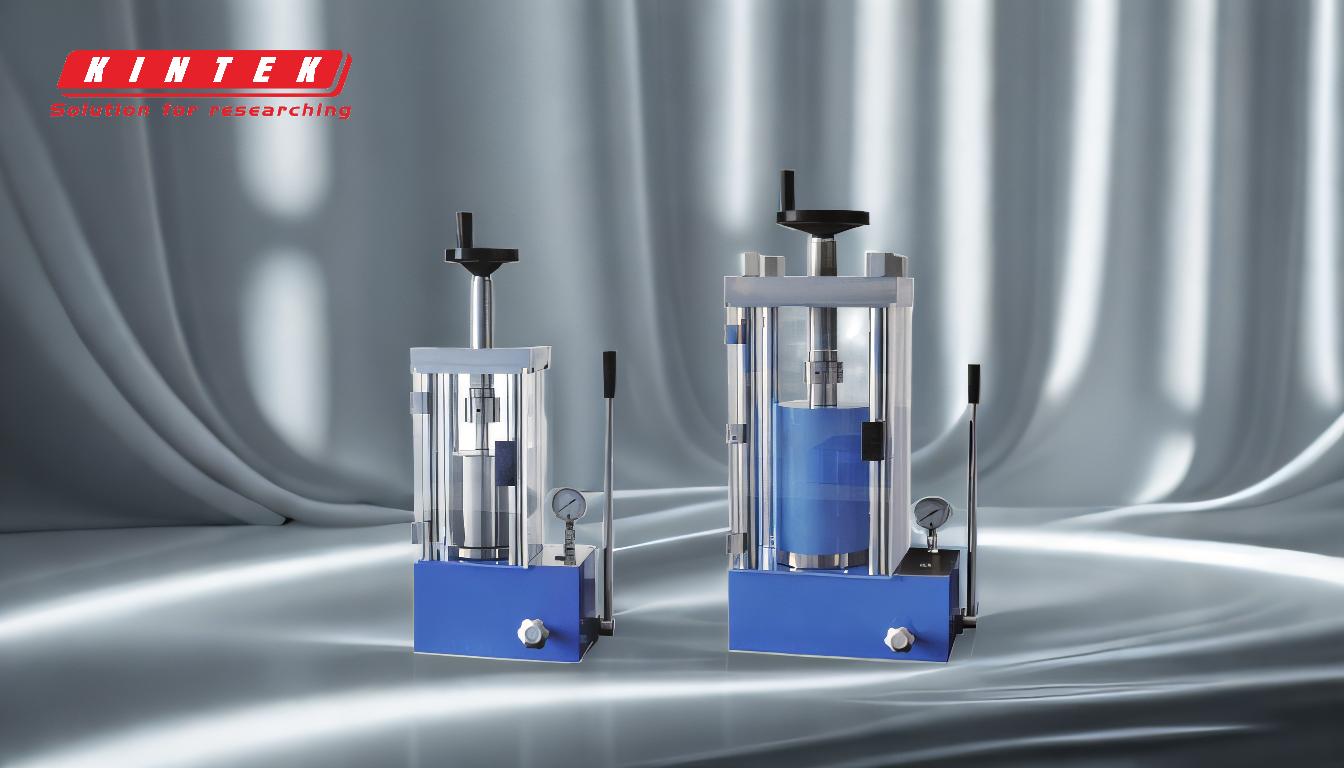
-
Process Overview:
- Hot Isostatic Pressing (HIP) involves applying high pressure (up to 100 MPa) and high temperature (up to 1000°C) to materials using an inert gas as the pressuring medium.
- The materials, often in powder or solid form, are placed in a sealed container and subjected to uniform pressure from all directions.
- This process results in materials with nearly 100% density, excellent metallurgical bonding, and improved mechanical properties.
-
Applications and Benefits:
- HIP is used to bond or clad multiple materials together, enhancing their structural integrity and performance.
- It significantly improves material properties such as wear resistance, corrosion resistance, and mechanical strength.
- The process can increase fatigue life by 10 to 100 times and achieve material densities close to theoretical values.
-
Methods of Isostatic Pressing:
- Wet-Bag Isostatic Pressing: The product is placed in a flexible mold submerged in a liquid medium. Pressure is applied uniformly, and the mold is removed after pressing.
- Dry-Bag Isostatic Pressing: The mold is fixed within the pressure vessel, and the liquid medium is injected directly into the mold. This method is faster and more suitable for mass production.
-
Warm Isostatic Pressing:
- A warm isostatic press is a variation of HIP that uses a heated liquid medium for precise temperature control.
- The liquid medium is heated to the desired temperature before being injected into the sealed pressing cylinder. A heat generator ensures accurate temperature maintenance during the process.
-
Material Outcomes:
- HIP produces compacts with minimal porosity, leading to materials with superior mechanical and thermal properties.
- The process is ideal for creating components with complex shapes and high-performance requirements, such as turbine blades, medical implants, and aerospace parts.
-
Industrial Significance:
- HIP is critical in industries where material performance and reliability are paramount, such as aerospace, automotive, and medical manufacturing.
- The ability to achieve near-theoretical density and enhance material properties makes HIP a preferred method for producing high-quality components.
By combining high pressure and temperature, HIP transforms materials into highly durable and reliable products, making it an indispensable process in advanced manufacturing.
Summary Table:
Aspect | Details |
---|---|
Process | High pressure (up to 100 MPa) and high temperature (up to 1000°C) applied using inert gas. |
Applications | Aerospace, automotive, medical devices, and high-performance material manufacturing. |
Benefits | Enhanced density, mechanical properties, wear resistance, and fatigue life. |
Methods | Wet-bag (flexible mold) and dry-bag (fixed mold) isostatic pressing. |
Material Outcomes | Near 100% density, superior mechanical and thermal properties, minimal porosity. |
Industrial Use | Critical for producing high-quality, durable components in advanced manufacturing. |
Unlock the potential of Hot Isostatic Pressing for your industry—contact our experts today to learn more!