The porosity of sintered ceramics is a critical property that influences their strength, durability, and performance in various applications. Porosity refers to the ratio of pore volume to the total volume of the material and is determined by factors such as the initial porosity of the green compact, sintering temperature, sintering time, and the application of pressure during the process. Sintered ceramics are created by compacting powdered natural materials like silica, quartz, and clay under extreme heat and pressure, which reduces porosity and enhances properties like hardness, chemical stability, and resistance to environmental factors. The final porosity can be controlled by adjusting sintering conditions, making it a versatile material for diverse industrial and architectural uses.
Key Points Explained:
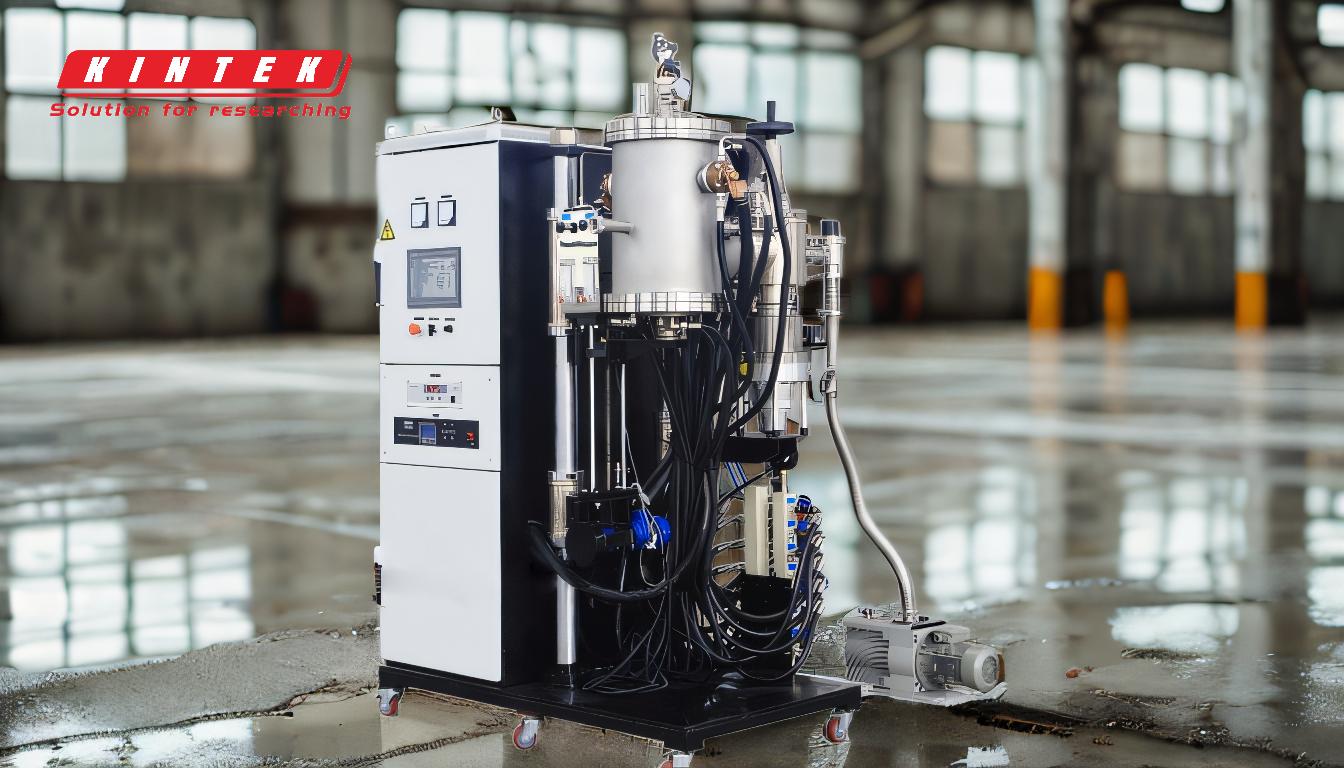
-
Definition of Porosity in Sintered Ceramics:
- Porosity is the ratio of pore volume to the total volume of the material.
- It is a key factor influencing the mechanical, thermal, and chemical properties of sintered ceramics.
- Lower porosity generally results in higher strength, hardness, and durability.
-
Factors Influencing Porosity:
-
Initial Porosity of the Green Compact:
- The porosity of the unsintered ("green") compact significantly affects the final porosity.
- Higher initial porosity requires more extensive sintering to achieve densification.
-
Sintering Temperature:
- Higher temperatures enhance particle diffusion, leading to reduced porosity.
- Pure oxide ceramics, for example, require higher temperatures due to solid-state diffusion.
-
Sintering Time:
- Longer sintering times allow for more complete densification, reducing porosity.
-
Application of Pressure:
- Applying pressure during sintering can accelerate densification and reduce porosity.
-
Initial Porosity of the Green Compact:
-
Measurement of Porosity:
- Porosity is measured as the ratio of pore volume to total volume.
- Other related properties include:
- Relative density (ratio of porous body density to non-porous material density).
- Pore size distribution, which affects permeability and strength.
- Apparent hardness (including pore effects) and solid hardness (excluding pore effects).
-
Impact of Porosity on Material Properties:
-
Strength and Hardness:
- Lower porosity enhances radial crushing strength and hardness.
-
Chemical Stability:
- Reduced porosity improves resistance to chemical attack and staining.
-
Thermal and Environmental Resistance:
- Sintered ceramics with controlled porosity are highly resistant to UV rays, extreme temperatures, and weathering.
-
Strength and Hardness:
-
Applications of Sintered Ceramics:
- Sintered ceramics are used in high-traffic areas, architectural surfaces, and industrial applications due to their durability and low porosity.
- Their resistance to abrasion, staining, and extreme conditions makes them ideal for demanding environments.
-
Control of Porosity During Manufacturing:
- Manufacturers can tailor porosity by adjusting the composition of raw materials, sintering conditions, and the application of pressure.
- This flexibility allows for the creation of sintered ceramics with specific properties for targeted applications.
By understanding and controlling porosity, manufacturers can optimize the performance of sintered ceramics for a wide range of applications, ensuring they meet the required standards for strength, durability, and resistance to environmental factors.
Summary Table:
Key Aspect | Details |
---|---|
Definition of Porosity | Ratio of pore volume to total volume, influencing strength and durability. |
Factors Influencing Porosity | Initial porosity, sintering temperature, time, and applied pressure. |
Measurement of Porosity | Includes pore volume ratio, relative density, and pore size distribution. |
Impact on Material Properties | Enhances strength, hardness, chemical stability, and environmental resistance. |
Applications | High-traffic areas, architectural surfaces, and industrial uses. |
Control During Manufacturing | Adjust raw materials, sintering conditions, and pressure for tailored porosity. |
Optimize your sintered ceramics for superior performance—contact our experts today!