The power requirement for a muffle furnace depends on its size, design, and intended use. Generally, muffle furnaces require a stable and sufficient power supply to ensure efficient operation. Key considerations include proper grounding, installation of an additional power switch, and adherence to safety protocols to prevent overheating or electrical hazards. The working environment must also be free of flammable materials and corrosive gases, and the furnace should be placed on a stable surface. Understanding the operating procedures and maintaining the equipment regularly are essential for safe and effective use.
Key Points Explained:
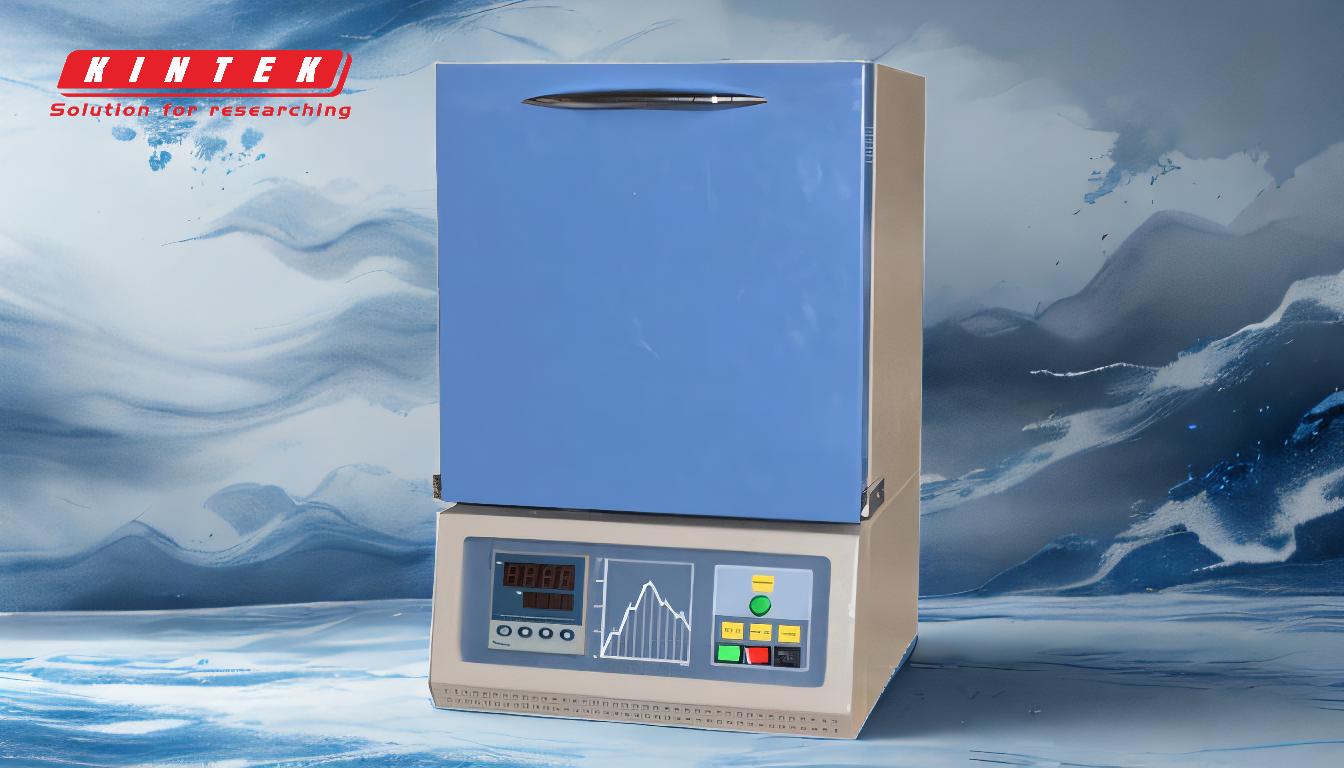
-
Power Supply and Requirements:
- Muffle furnaces typically require a stable power supply, often ranging from 110V to 240V, depending on the model and capacity.
- The power requirement is directly proportional to the furnace's size and maximum operating temperature. Larger furnaces or those designed for higher temperatures generally consume more power.
- An additional power switch should be installed at the power cord introduction point to control the total power supply, ensuring safety and ease of operation.
-
Grounding and Electrical Safety:
- Both the electric furnace and its controller must be reliably grounded to prevent electrical hazards and ensure safe operation.
- Proper grounding reduces the risk of electric shock and protects the equipment from power surges or fluctuations.
-
Working Environment:
- The working environment for a muffle furnace should be free of flammable, explosive, or corrosive materials to prevent accidents and equipment damage.
- The furnace should be placed on a solid, stable surface, such as a concrete table or shelf, to minimize vibration and ensure proper operation.
-
Controller Placement:
- The controller should be placed away from the furnace to avoid overheating and should be protected from vibrations, which could affect its performance.
-
Operational Safety:
- Operators must familiarize themselves with the operating procedures and wear appropriate protective equipment.
- Overloading the furnace should be avoided, and the furnace should be kept clean to maintain efficiency and safety.
- Regular equipment checks are necessary to identify and address potential issues early.
-
Maintenance and Usage:
- Avoid rapid cooling or heating, as this can damage the furnace or compromise its performance.
- Prohibit placing flammable or combustible materials inside or around the furnace.
- Ensure good ventilation in the operating area to dissipate heat and prevent the buildup of harmful gases.
-
Power Management:
- Turn off the power after use to conserve energy and reduce the risk of accidents.
- In case of malfunction, stop using the furnace immediately and seek professional assistance.
By following these guidelines, users can ensure the safe and efficient operation of a muffle furnace while meeting its power requirements.
Summary Table:
Key Aspect | Details |
---|---|
Power Supply | 110V to 240V, depending on model and capacity. |
Power Management | Install an additional power switch; turn off power after use. |
Grounding | Reliable grounding for furnace and controller to prevent electrical hazards. |
Working Environment | Free of flammable, explosive, or corrosive materials; stable surface. |
Controller Placement | Away from furnace to avoid overheating and vibrations. |
Operational Safety | Follow procedures, avoid overloading, and perform regular checks. |
Maintenance | Avoid rapid heating/cooling; ensure ventilation and cleanliness. |
Need help selecting or maintaining a muffle furnace? Contact our experts today for personalized guidance!