The preheat temperature for cast iron brazing typically ranges between 120-150°C, depending on the size and complexity of the part. Preheating is essential to minimize thermal stress and ensure proper bonding. For small parts, a conventional oven may suffice, while larger parts may require localized heating using oxy-fuel or LPG torches. The brazing temperature should ideally be the lowest possible within the recommended range, usually at least 25°C (50°F) above the liquidus temperature of the braze alloy. Indirect preheating of critical areas is also recommended to achieve uniform heat distribution and prevent cracking.
Key Points Explained:
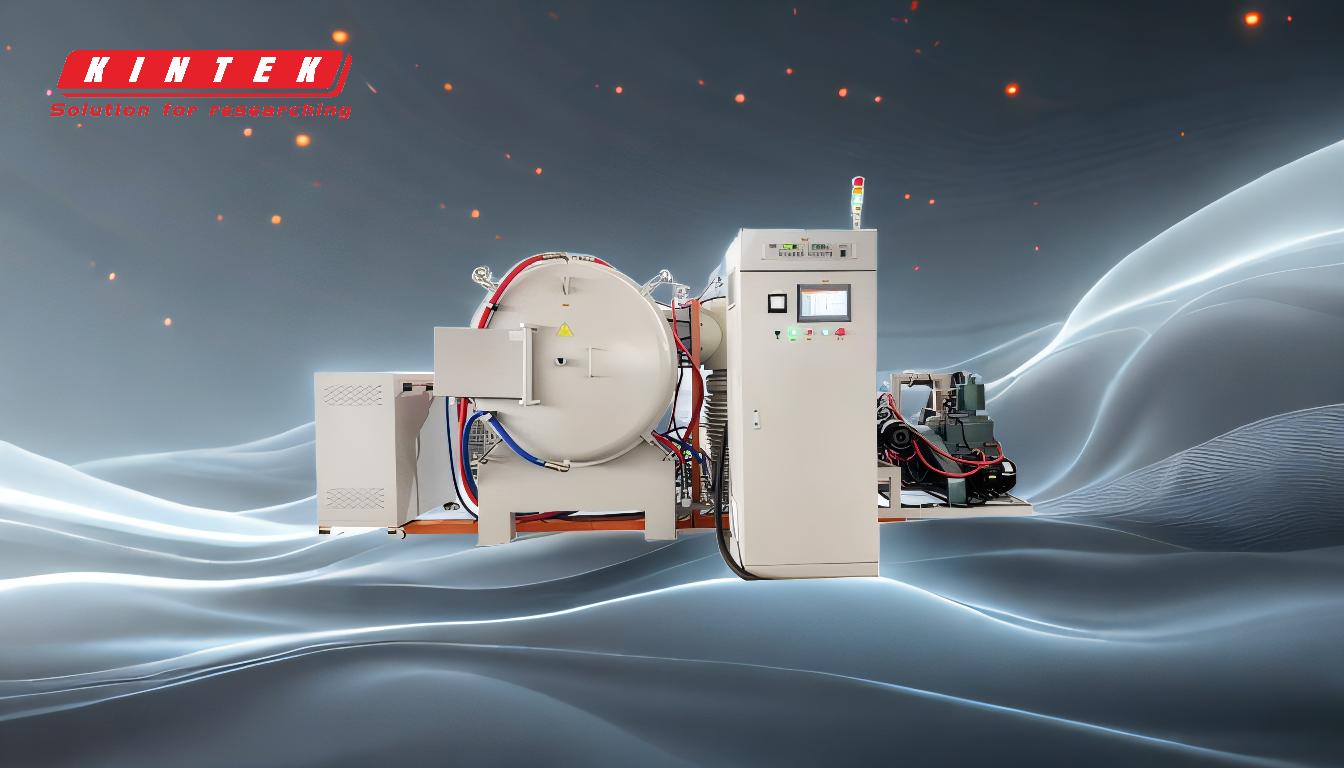
-
Preheat Temperature Range:
- The recommended preheat temperature for cast iron brazing is 120-150°C. This range ensures that the material is sufficiently warmed to reduce thermal stress while avoiding excessive heat that could lead to distortion or cracking.
-
Preheating Methods:
- Small Parts: For smaller components, a conventional oven is often sufficient to achieve the required preheat temperature. This method ensures even heating and is easy to control.
- Large Parts: Larger or more complex parts may require localized heating using tools like an oxy-fuel torch or LPG burner. These methods allow for targeted heating of specific areas, which is crucial for preventing uneven thermal expansion.
-
Importance of Gradual Heating:
- Preheating should be gradual to avoid thermal shock, which can cause cracking or warping in cast iron. Indirect preheating of critical areas ensures that the heat is evenly distributed, reducing the risk of localized stress.
-
Brazing Temperature Considerations:
- The brazing temperature should be set at the lowest possible value within the recommended range, typically 25°C (50°F) above the liquidus temperature of the braze alloy. This ensures proper flow and bonding of the filler material without overheating the base metal.
-
Visual Indicators for Preheating:
- For cast iron, a dull red color is often used as a visual indicator that the material has reached the appropriate preheat temperature. This method is particularly useful when using torches or other localized heating tools.
-
Indirect Preheating:
- Indirect preheating involves warming surrounding or critical areas of the workpiece to ensure uniform heat distribution. This technique is especially important for large or complex parts where direct heating might not be sufficient to prevent thermal stress.
By following these guidelines, you can ensure a successful brazing process for cast iron, minimizing the risk of defects and achieving strong, durable joints.
Summary Table:
Aspect | Details |
---|---|
Preheat Temperature | 120-150°C, depending on part size and complexity |
Preheating Methods | - Small parts: Conventional oven - Large parts: Oxy-fuel or LPG torches |
Brazing Temperature | 25°C (50°F) above the braze alloy's liquidus temperature |
Visual Indicator | Dull red color for preheat temperature |
Key Tip | Use indirect preheating for uniform heat distribution and stress reduction |
Need expert advice on cast iron brazing? Contact us today for tailored solutions!