The pressure required for isostatic pressing of ceramics varies depending on the specific process and material. Warm isostatic pressing typically uses pressures around 300 MPa, while cold isostatic pressing (CIP) often operates at an average pressure of 200–250 MPa. The general range for forming ceramics through isostatic pressing is between 21 and 210 MPa (3000 to 30000 psi). The process involves loading the sample into a pressure vessel, applying the required temperature and pressure, and then holding and relaxing to return to ambient conditions.
Key Points Explained:
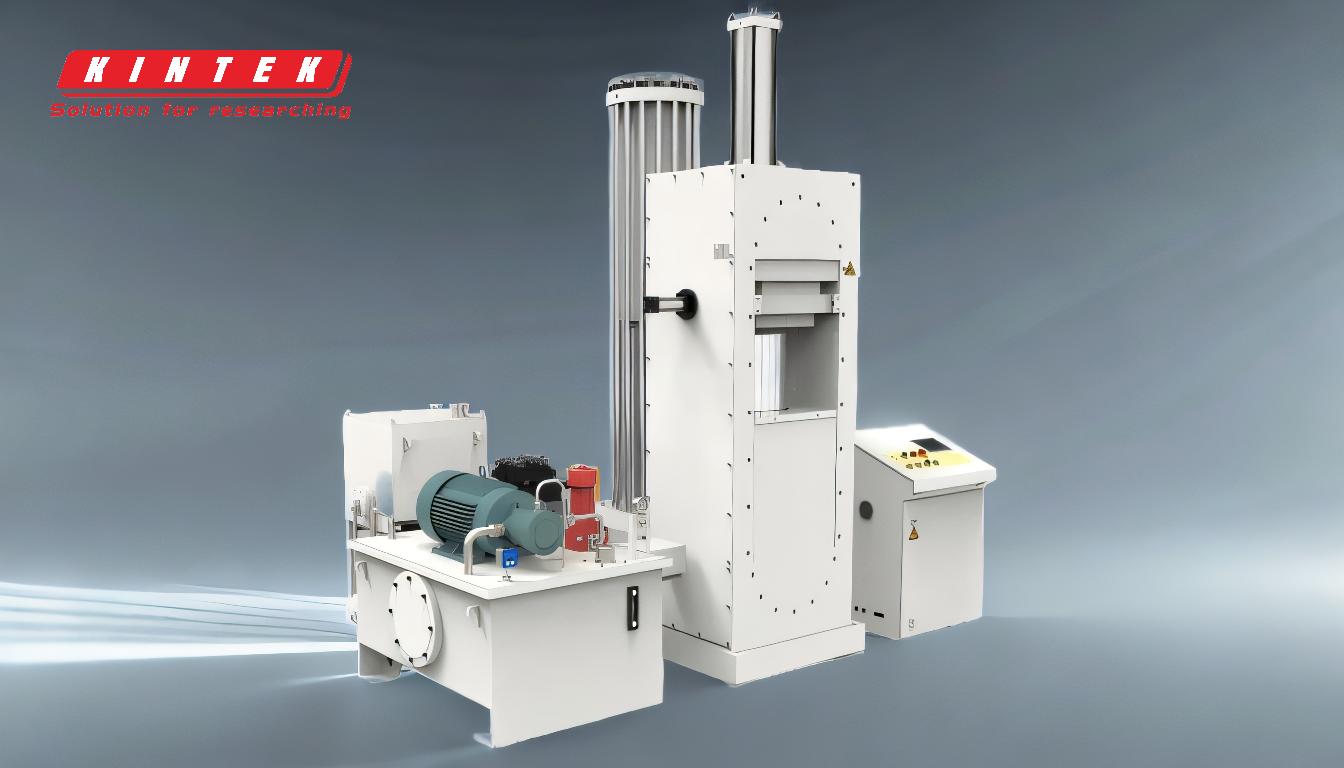
-
Pressure Range for Isostatic Pressing of Ceramics
- The pressure used in isostatic pressing depends on the type of process and the material being processed.
- For warm isostatic pressing, the pressure is typically around 300 MPa.
- For cold isostatic pressing (CIP), the average pressure is usually in the range of 200–250 MPa.
- The general forming pressure range for ceramics in isostatic pressing is 21 to 210 MPa (3000 to 30000 psi).
-
Process Details
- The isostatic pressing process involves placing the sample inside a pressure vessel.
- The temperature and pressure are elevated to the required levels using process control systems.
- After achieving the desired conditions, the system holds the pressure and temperature for a specific duration.
- Finally, the system undergoes a relaxation process to return to ambient conditions.
-
Factors Influencing Pressure Selection
- The choice of pressure depends on the material properties, such as density and strength requirements.
- Higher pressures (e.g., 300 MPa) are used for warm isostatic pressing to achieve better densification and material properties.
- Lower pressures (e.g., 21–210 MPa) are suitable for forming ceramics in cold isostatic pressing, where the focus is on shaping rather than densification.
-
Applications and Implications
- Warm isostatic pressing is often used for advanced ceramics requiring high density and strength.
- Cold isostatic pressing is more common for forming ceramics into complex shapes before sintering.
- The pressure range ensures that the ceramics achieve the desired mechanical and structural properties without causing damage during the process.
By understanding these key points, equipment and consumable purchasers can make informed decisions about the appropriate pressure settings for their specific ceramic processing needs.
Summary Table:
Process Type | Pressure Range | Key Applications |
---|---|---|
Warm Isostatic Pressing | ~300 MPa | Advanced ceramics requiring high density and strength. |
Cold Isostatic Pressing | 200–250 MPa | Forming ceramics into complex shapes before sintering. |
General Forming Range | 21–210 MPa (3000–30000 psi) | Suitable for shaping ceramics without densification. |
Need help selecting the right pressure for your ceramic processing? Contact our experts today!