Sputtering is a physical vapor deposition (PVD) technique used to deposit thin films of materials onto substrates. The process occurs in a vacuum chamber where a target material is bombarded with energetic ions, causing atoms to be ejected and deposited onto a substrate. The vacuum environment is critical to the success of the sputtering process, as it minimizes contamination and ensures the efficient transfer of material. The pressure inside the sputtering vacuum chamber typically ranges from the high-vacuum range (10^-6 mbar or better) for base pressure to the milliTorr range (10^-3 to 10^-2 mbar) during the deposition process. This controlled environment allows for the precise formation of thin films with minimal impurities.
Key Points Explained:
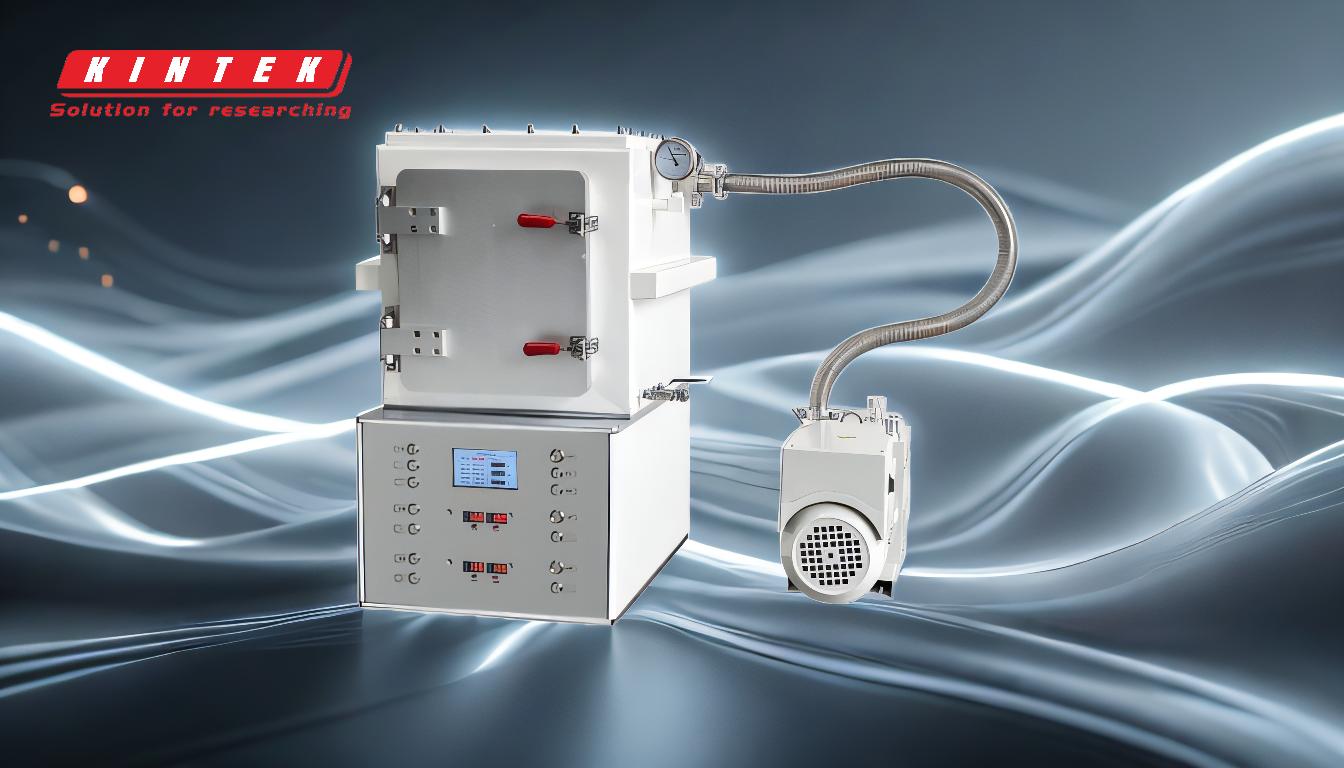
-
Base Pressure in Sputtering Vacuum:
- Before introducing the sputtering gas, the chamber is evacuated to a high vacuum to achieve a base pressure. This base pressure is typically in the range of 10^-6 mbar or better.
- The high vacuum ensures that the chamber is free from contaminants and residual gases, which could otherwise interfere with the deposition process and degrade the quality of the thin film.
-
Introduction of Sputtering Gas:
- Once the base pressure is achieved, a sputtering gas (usually an inert gas like argon) is introduced into the chamber. The gas flow is controlled using a flow controller, with rates varying from a few standard cubic centimeters per minute (sccm) in research settings to several thousand sccm in industrial production.
- The introduction of the sputtering gas increases the pressure in the chamber to the milliTorr range, which is necessary for the formation of plasma.
-
Operating Pressure During Sputtering:
- During the sputtering process, the pressure is maintained in the range of 10^-3 to 10^-2 mbar (milliTorr range). This pressure range is optimal for sustaining the plasma and ensuring efficient sputtering of the target material.
- The pressure is regulated using a pressure control system, which balances the gas flow and the pumping speed to maintain a stable environment.
-
Importance of Vacuum in Sputtering:
- The vacuum environment is crucial for the sputtering process as it minimizes the presence of background gases and contaminants. This ensures that the ejected atoms from the target material can travel unimpeded to the substrate, resulting in a high-quality thin film.
- The vacuum also allows for precise control over the deposition process, enabling the formation of uniform and defect-free films.
-
Comparison with Other Deposition Techniques:
- Sputtering vacuum systems are more complex than those used in thermal or e-beam evaporation. This complexity arises from the need to maintain a high vacuum base pressure and precisely control the gas flow and pressure during the deposition process.
- The ability to operate at lower pressures and with controlled gas flows makes sputtering a versatile and widely used technique for depositing a variety of materials, including metals, semiconductors, and insulators.
In summary, the pressure in a sputtering vacuum chamber is carefully controlled to ensure optimal conditions for the deposition of thin films. The process begins with achieving a high vacuum base pressure, followed by the introduction of sputtering gas to reach the operating pressure in the milliTorr range. This controlled environment is essential for producing high-quality, contamination-free thin films.
Summary Table:
Pressure Stage | Pressure Range | Purpose |
---|---|---|
Base Pressure | 10^-6 mbar or better | Ensures a contaminant-free environment before introducing sputtering gas. |
Operating Pressure | 10^-3 to 10^-2 mbar | Sustains plasma and enables efficient sputtering of the target material. |
Sputtering Gas Pressure | MilliTorr range | Facilitates plasma formation and controlled deposition of thin films. |
Optimize your thin film deposition process with expert guidance—contact us today!