A vacuum furnace operates under controlled pressure conditions, typically ranging from –0.1 MPa to several Pascals (Pa), depending on the specific application. This low-pressure environment is crucial for processes like ceramic firing, vacuum smelting, degassing, annealing, and brazing, as it minimizes contamination from gases like carbon and oxygen. The vacuum furnace's design includes components such as a high-speed diffusion pump, a vacuum chamber with a high-temperature hot zone, and a control cabinet to maintain precise pressure and temperature conditions. The operating environment must be clean, with operators wearing clean garments and gloves to prevent contamination. The furnace's ability to achieve uniform temperature distribution, rapid cooling, and computer-controlled repeatability makes it ideal for high-precision industrial applications.
Key Points Explained:
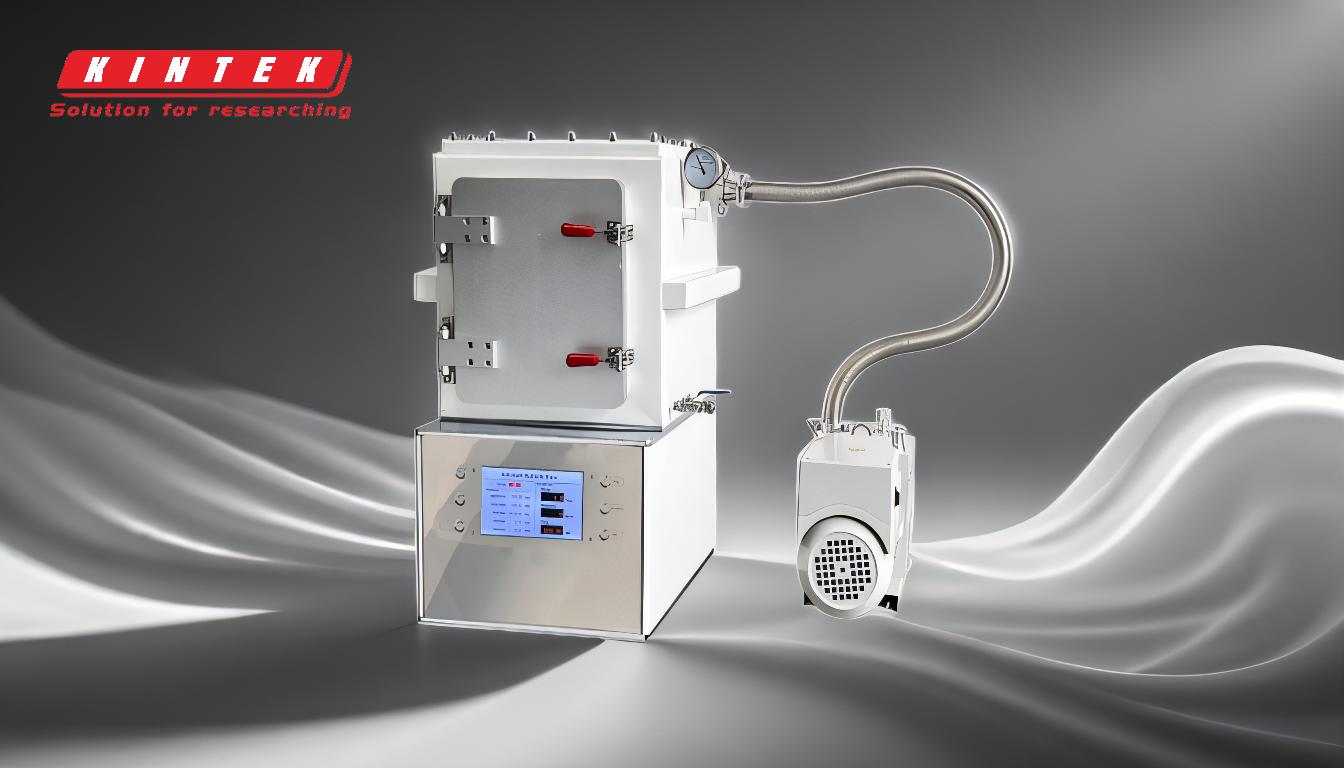
-
Pressure Range in a Vacuum Furnace:
- The pressure inside a vacuum furnace typically ranges from –0.1 MPa to several Pascals (Pa). This range is essential for creating a low-pressure environment that minimizes contamination and ensures high-purity results.
- The vacuum degree is maintained using components like a high-speed diffusion pump, which effectively removes gases and byproducts from the chamber.
-
Applications Requiring Vacuum Conditions:
- Vacuum furnaces are used for processes such as ceramic firing, vacuum smelting, degassing of electric vacuum parts, annealing, brazing, and ceramic-metal sealing.
- These applications benefit from the absence of oxidation and contamination, which are critical for achieving high-quality results.
-
Temperature Control and Uniformity:
- Vacuum furnaces offer precise temperature control, with ranges typically between 1600-2400°C. The uniform temperature distribution ensures consistent results across the heating zone.
- Rapid cooling (quenching) capabilities further enhance process efficiency by shortening cycle times.
-
Contamination Prevention:
- The low-pressure environment significantly reduces contamination from gases like carbon and oxygen. This is particularly important for applications requiring high-purity materials.
- Operators must follow strict cleanliness protocols, including wearing clean garments and gloves, to prevent introducing impurities.
-
Key Components of a Vacuum Furnace:
- High-Speed Diffusion Pump: Maintains the vacuum by removing gases and byproducts.
- Vacuum Chamber with High-Temperature Hot Zone: Provides the controlled environment for heating and cooling processes.
- Control Cabinet: Ensures precise regulation of temperature, pressure, and other parameters.
-
Operational Requirements:
- Operators must adhere to strict cleanliness and safety protocols, including wearing clean garments and gloves.
- The furnace environment must be free from contaminants to ensure optimal performance and product quality.
-
Advantages of Using a Vacuum Furnace:
- Uniform Temperature Distribution: Ensures consistent results across the heating zone.
- Precise Temperature Control: Allows for repeatable and reliable processes.
- Low Contamination: Minimizes the presence of unwanted gases and impurities.
- Rapid Cooling: Reduces process cycle times and enhances efficiency.
- Computer-Controlled Processes: Ensures repeatability and precision in industrial applications.
By understanding the pressure requirements and operational parameters of a vacuum furnace, users can optimize their processes for high-quality, contamination-free results.
Summary Table:
Aspect | Details |
---|---|
Pressure Range | –0.1 MPa to several Pascals (Pa) |
Key Applications | Ceramic firing, vacuum smelting, degassing, annealing, brazing |
Temperature Range | 1600-2400°C |
Key Components | High-speed diffusion pump, vacuum chamber, control cabinet |
Advantages | Uniform heating, rapid cooling, low contamination, precise control |
Operational Requirements | Clean environment, strict operator protocols |
Ready to optimize your processes with a vacuum furnace? Contact our experts today for tailored solutions!