The pressure range for a lab filter press typically varies depending on the specific model and application, but it generally falls within 100 to 225 psi (pounds per square inch) or 7 to 15 bar. This range ensures efficient filtration of solids from liquids, making it suitable for laboratory-scale operations. The pressure is applied to force the liquid through the filter media, leaving the solids behind as a filter cake. The exact pressure range can be adjusted based on the material being filtered, the desired filtration speed, and the equipment's design.
Key Points Explained:
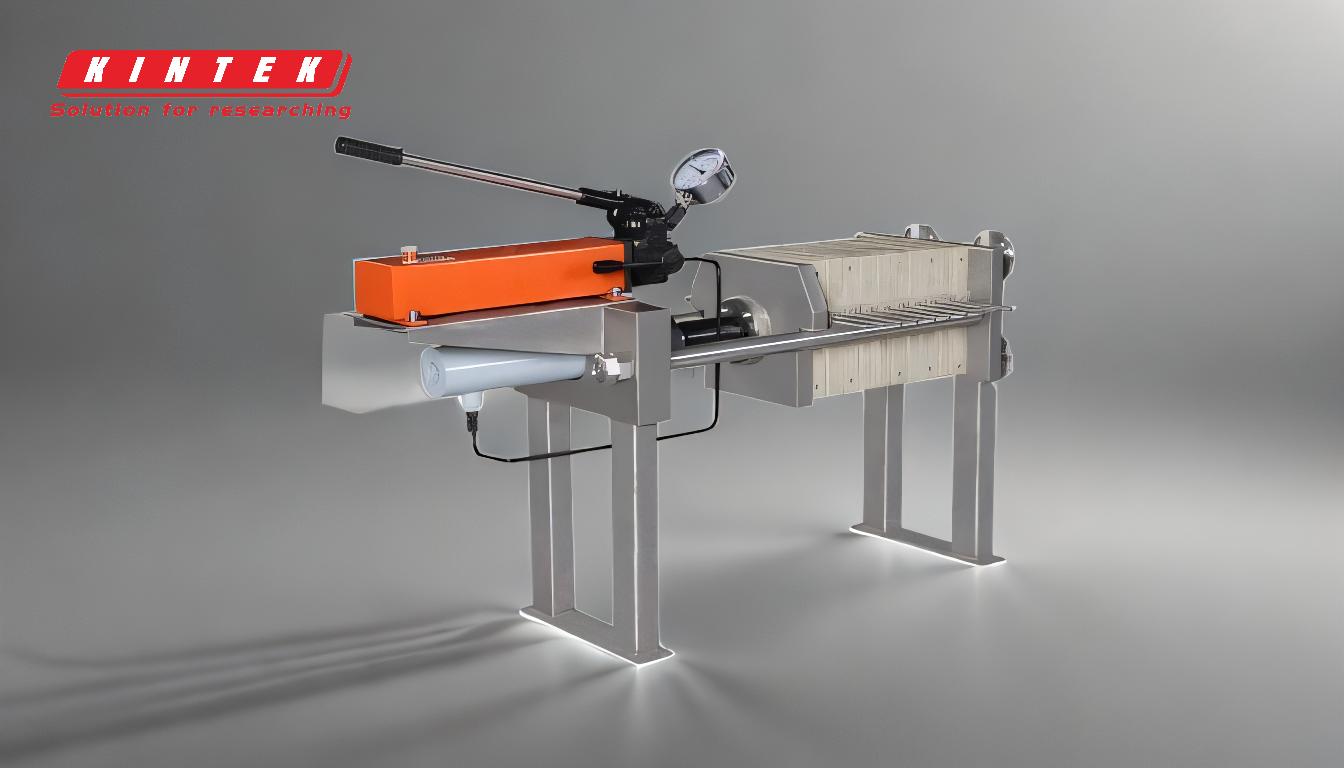
-
Typical Pressure Range for Lab Filter Presses:
- Lab filter presses usually operate within a pressure range of 100 to 225 psi (7 to 15 bar). This range is optimal for achieving effective separation of solids and liquids in laboratory settings.
- The pressure is applied hydraulically or mechanically, depending on the design of the filter press.
-
Factors Influencing Pressure Range:
- Material Properties: The viscosity and particle size of the slurry being filtered can influence the required pressure. Thicker or more viscous materials may require higher pressures.
- Filtration Speed: Higher pressures can speed up the filtration process but may risk damaging the filter media or equipment if not carefully controlled.
- Equipment Design: The design of the filter press, including the size and type of filter plates, affects the pressure range it can handle.
-
Applications of Lab Filter Presses:
- Lab filter presses are used in various industries, including pharmaceuticals, food and beverage, chemical processing, and environmental testing. They are ideal for small-scale filtration tasks where precision and control are essential.
- Common applications include clarifying liquids, recovering solids, and testing filtration efficiency.
-
Importance of Pressure Control:
- Proper pressure control ensures efficient filtration without damaging the filter media or equipment. Over-pressurizing can lead to leaks, filter media rupture, or equipment failure.
- Many modern lab filter presses come with pressure gauges and safety mechanisms to monitor and regulate pressure during operation.
-
Adjusting Pressure for Specific Needs:
- The pressure can be adjusted based on the specific requirements of the filtration task. For example, delicate materials may require lower pressures to avoid damage, while denser slurries may need higher pressures for effective separation.
- Operators should refer to the equipment manual and conduct small-scale tests to determine the optimal pressure for their application.
-
Maintenance and Safety Considerations:
- Regular maintenance of the filter press, including checking seals, hoses, and pressure gauges, is essential to ensure safe and efficient operation.
- Safety precautions should be taken when operating at higher pressures to prevent accidents or equipment damage.
By understanding the pressure range and its influencing factors, users can optimize the performance of their lab filter press for various filtration tasks.
Summary Table:
Aspect | Details |
---|---|
Typical Pressure Range | 100-225 psi (7-15 bar) |
Pressure Application | Hydraulic or mechanical, depending on design |
Key Influencing Factors | Material properties, filtration speed, equipment design |
Applications | Pharmaceuticals, food & beverage, chemical processing, environmental testing |
Pressure Control | Essential to prevent damage to filter media or equipment |
Adjustments | Adjust based on material type, desired speed, and equipment specifications |
Maintenance | Regular checks on seals, hoses, and pressure gauges for safe operation |
Need help selecting the right filter press for your lab? Contact us today to get expert advice!