Roller mills operate on the principles of compression and shearing to grind grains into fine particles. The process involves feeding grains between rotating cylinders (rollers) with a controlled gap that determines the fineness of the grind. As the rollers rotate, they exert compressive forces to crush the grains and shear forces to further break them down, resulting in a uniform and finely ground product. This method is efficient and widely used in industries such as food processing, agriculture, and manufacturing.
Key Points Explained:
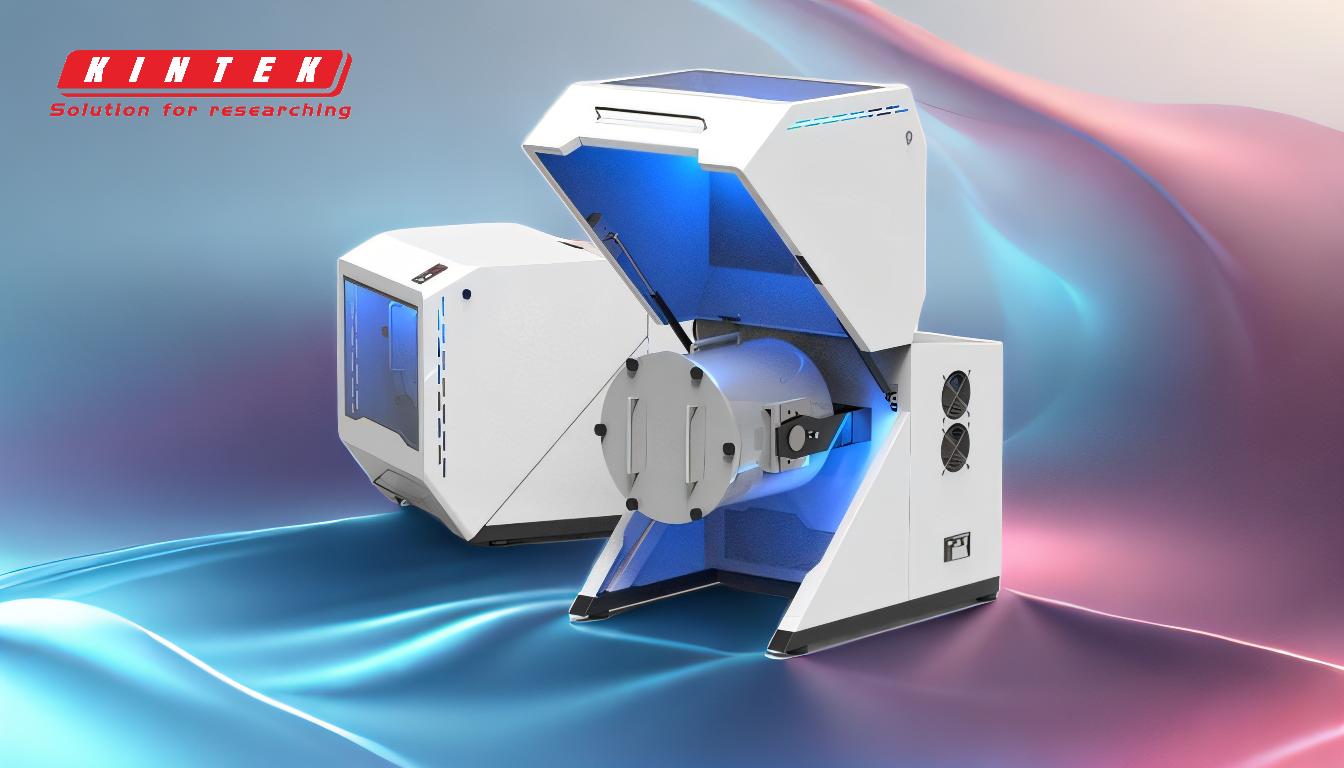
-
Principle of Operation:
- Roller mills rely on compression and shearing forces to grind materials.
- Compression occurs as the grains are pressed between the rotating rollers, breaking them into smaller particles.
- Shearing happens when the grains are dragged and torn apart by the differential speeds of the rollers, further refining the grind.
-
Role of Rotating Cylinders (Rollers):
- The rollers are the core components of a roller mill. They rotate either at the same speed or at slightly different speeds to enhance grinding efficiency.
- The gap between the rollers is adjustable, allowing control over the fineness of the grind. A smaller gap produces finer particles, while a larger gap yields coarser output.
-
Material Feeding Mechanism:
- Grains or other materials are fed into the mill through a controlled feed system, ensuring a consistent flow between the rollers.
- Proper feeding prevents overloading and ensures uniform grinding.
-
Compression and Shearing in Action:
- As the material passes through the rollers, it is subjected to high pressure, which crushes the grains.
- Simultaneously, the shearing action caused by the differential rotation of the rollers further breaks down the particles, resulting in a fine and consistent grind.
-
Applications and Advantages:
- Roller mills are widely used in industries such as flour milling, animal feed production, and chemical processing.
- Advantages include:
- High efficiency in grinding.
- Ability to produce uniform particle sizes.
- Low energy consumption compared to other grinding methods.
- Minimal heat generation, preserving the quality of heat-sensitive materials.
-
Adjustability and Control:
- The gap between the rollers can be precisely adjusted to meet specific grinding requirements.
- This adjustability makes roller mills versatile, suitable for a wide range of materials and fineness levels.
-
Comparison with Other Grinding Methods:
- Unlike laboratory hammer mills, which rely on impact forces, roller mills use compression and shearing, resulting in less noise and wear.
- Roller mills are more efficient for fine grinding and produce less dust compared to other grinding systems.
By understanding these key points, equipment and consumable purchasers can make informed decisions about the suitability of roller mills for their specific applications. The ability to control the fineness of the grind and the efficiency of the process make roller mills a preferred choice in many industries.
Summary Table:
Key Aspect | Details |
---|---|
Principle of Operation | Compression and shearing forces break down grains into fine particles. |
Role of Rollers | Rotating cylinders with adjustable gaps control grind fineness. |
Material Feeding | Controlled feed system ensures consistent flow and uniform grinding. |
Applications | Flour milling, animal feed production, chemical processing. |
Advantages | High efficiency, uniform particle size, low energy consumption, minimal heat generation. |
Adjustability | Precise gap adjustment for versatile grinding requirements. |
Comparison | Less noise, wear, and dust compared to hammer mills. |
Interested in optimizing your grinding process? Contact us today to find the perfect roller mill for your needs!