Chemical Vapor Deposition (CVD) is a sophisticated technique used to deposit solid materials onto a substrate through chemical reactions involving gaseous precursors. The process typically occurs in a controlled environment, where precursor gases are introduced into a reaction chamber under specific conditions of temperature, pressure, and flow rate. These gases decompose or react on the substrate's surface, forming a thin, uniform layer of the desired material. CVD is widely utilized in industries such as semiconductors, where it is essential for producing high-quality thin films and coatings. The process can be enhanced through various methods, including plasma assistance, laser irradiation, and the use of metal-organic compounds, making it versatile for different applications.
Key Points Explained:
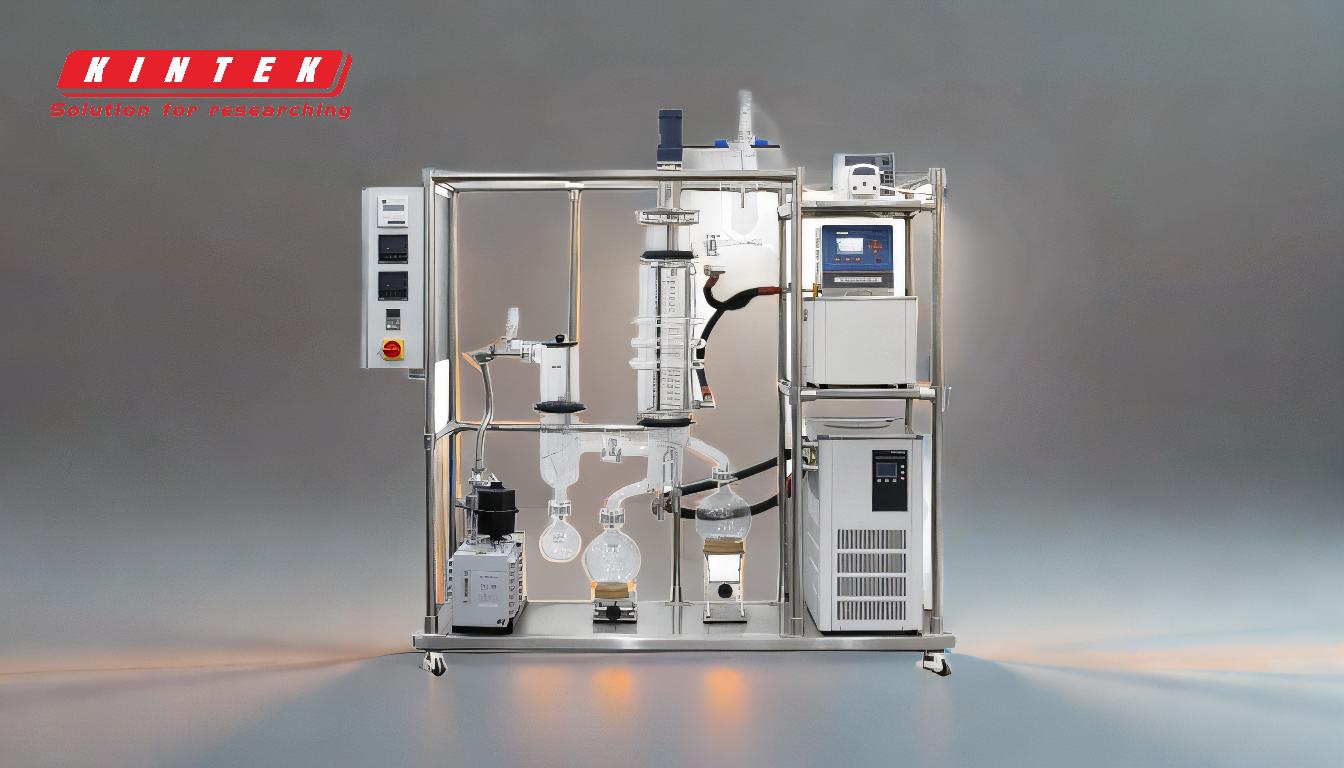
-
Basic Principle of CVD:
- Gaseous Precursors: The process begins with the introduction of gaseous precursor reactants into a reaction chamber.
- Chemical Reactions: These precursors undergo chemical reactions, such as decomposition or combination, on or near the surface of a heated substrate.
- Thin Film Formation: The result of these reactions is the formation of a thin, solid film on the substrate.
-
Process Conditions:
- Temperature: The substrate is typically heated to facilitate the chemical reactions necessary for deposition.
- Pressure: The reaction chamber operates under controlled pressure conditions, which can vary depending on the specific CVD method used.
- Flow Rate: The flow rate of the precursor gases is carefully regulated to ensure uniform deposition.
-
Types of CVD:
- Atmospheric Pressure CVD (APCVD): Conducted at atmospheric pressure, suitable for certain types of films.
- Plasma-Assisted CVD (PACVD): Utilizes plasma to enhance the chemical reactions, allowing for lower temperature processes.
- Laser-Assisted CVD (LACVD): Employs laser irradiation to precisely control the deposition process.
- Metal-Organic CVD (MOCVD): Uses metal-organic compounds as precursors, often for depositing complex materials like semiconductors.
-
Reaction Chamber Environment:
- Vacuum Environment: Many CVD processes are performed in a vacuum to minimize contamination and control the deposition environment.
- Gas Flow and By-products: Volatile by-products are generated during the reactions and are removed from the chamber by gas flow, ensuring a clean deposition process.
-
Deposition Mechanism:
- Surface Reaction: The precursor gases react on the substrate's surface, leading to the formation of a chemically bonded thin film.
- Uniform Layer Formation: The process is designed to create a uniform layer of material, which is critical for applications requiring precise thickness and composition.
-
Applications:
- Semiconductor Industry: CVD is extensively used to produce thin films for semiconductor devices, including integrated circuits and solar cells.
- High-Performance Materials: The technique is also employed to deposit high-quality, high-performance solid materials for various industrial applications.
-
Advantages of CVD:
- High Purity: The controlled environment and precise conditions result in high-purity deposits.
- Versatility: CVD can be adapted to deposit a wide range of materials, from metals to ceramics.
- Uniformity: The process ensures uniform deposition, essential for applications requiring consistent material properties.
-
Challenges and Considerations:
- Complexity: The process can be complex, requiring precise control over numerous parameters.
- Cost: The equipment and precursor materials can be expensive, making CVD a costly technique.
- Safety: Handling precursor gases and operating high-temperature, high-vacuum systems require stringent safety measures.
In summary, Chemical Vapor Deposition is a versatile and powerful technique for depositing thin films and coatings with high precision and quality. Its applications span various industries, particularly in the production of semiconductor devices and high-performance materials. Understanding the principles, conditions, and mechanisms of CVD is essential for optimizing the process and achieving desired material properties.
Summary Table:
Aspect | Details |
---|---|
Basic Principle | Gaseous precursors react on a heated substrate to form a thin solid film. |
Process Conditions | Controlled temperature, pressure, and flow rate for uniform deposition. |
Types of CVD | APCVD, PACVD, LACVD, MOCVD. |
Applications | Semiconductors, high-performance materials, solar cells, and more. |
Advantages | High purity, versatility, and uniform deposition. |
Challenges | Complexity, high cost, and safety considerations. |
Interested in optimizing your thin film production? Contact our experts today to learn more about CVD solutions!