The principle of the CVD (Chemical Vapor Deposition) method involves the use of chemical reactions to produce high-purity, high-performance solid materials. This process typically occurs in a vacuum or controlled atmosphere where gaseous reactants are introduced to a substrate, leading to the deposition of a thin film or coating. The process is widely used in the semiconductor industry, as well as for creating protective coatings, optical fibers, and nanomaterials. The CVD method is highly versatile and can be tailored to produce materials with specific properties by adjusting parameters such as temperature, pressure, and reactant composition.
Key Points Explained:
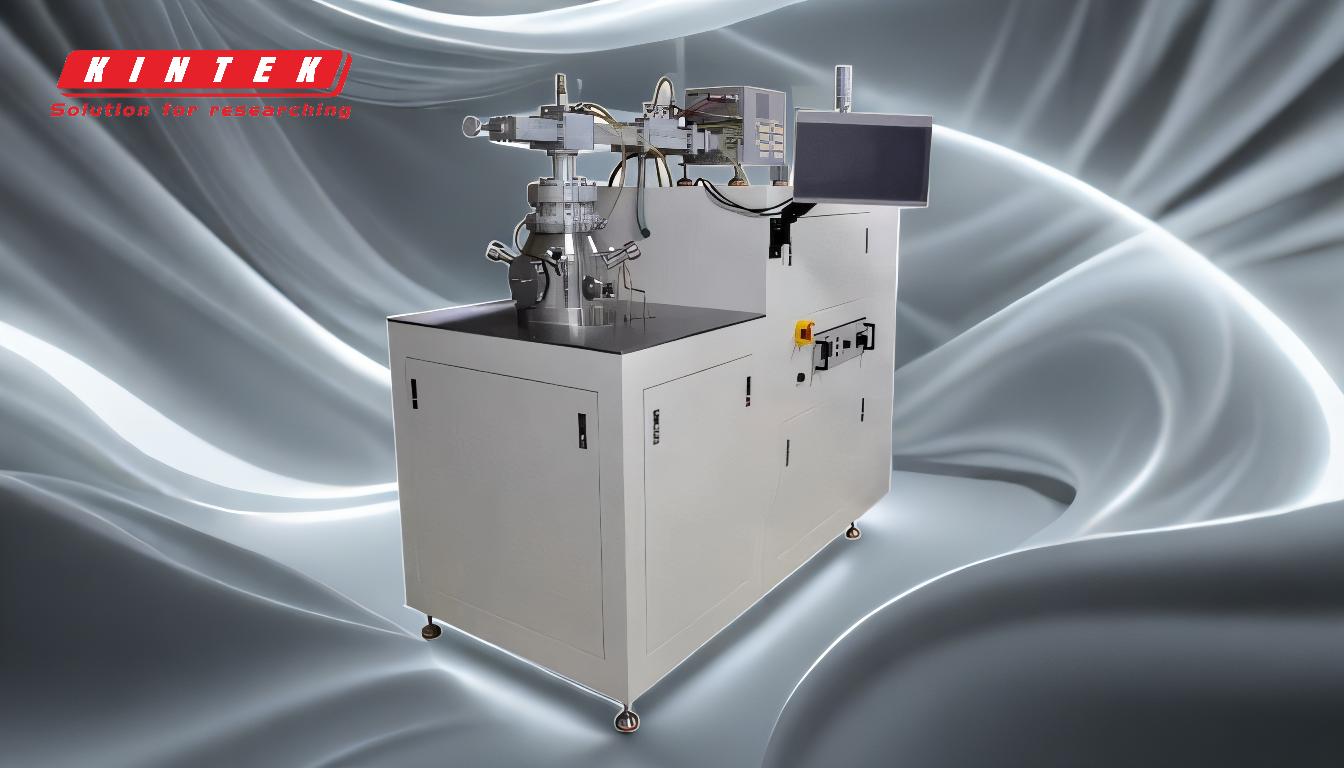
-
Basic Principle of CVD:
- CVD involves the chemical reaction of gaseous precursors to form a solid material on a substrate. This process is driven by thermal energy, which activates the chemical reactions necessary for deposition.
- The process can be conducted at atmospheric pressure or under vacuum, depending on the desired outcome and the materials involved.
-
Key Components of a CVD System:
- Reactor Chamber: This is where the chemical reactions take place. It is designed to withstand high temperatures and corrosive environments.
- Gas Delivery System: This system controls the flow of precursor gases into the reactor chamber. Precise control of gas flow rates is crucial for achieving uniform deposition.
- Substrate Holder: The substrate, which is the material to be coated, is placed on a holder within the reactor. The holder may be heated or cooled to control the deposition process.
- Exhaust System: This system removes by-products and unreacted gases from the reactor chamber, ensuring a clean environment for the deposition process.
-
Types of CVD Processes:
- Atmospheric Pressure CVD (APCVD): Conducted at atmospheric pressure, this method is simpler and less expensive but may produce less uniform coatings.
- Low-Pressure CVD (LPCVD): Conducted under reduced pressure, this method allows for better control of the deposition process and is often used for high-purity applications.
- Plasma-Enhanced CVD (PECVD): This method uses plasma to enhance the chemical reactions, allowing for lower deposition temperatures and faster processing times.
-
Applications of CVD:
- Semiconductor Manufacturing: CVD is widely used to deposit thin films of silicon, silicon dioxide, and other materials in the production of integrated circuits.
- Protective Coatings: CVD can produce hard, wear-resistant coatings such as diamond-like carbon (DLC) and titanium nitride (TiN).
- Optical Fibers: CVD is used to manufacture the core and cladding layers of optical fibers, which are essential for telecommunications.
- Nanomaterials: CVD is a key method for producing carbon nanotubes, graphene, and other nanomaterials with unique properties.
-
Advantages of CVD:
- High Purity: The process can produce materials with extremely high purity levels, which is critical for many applications.
- Uniformity: CVD allows for the deposition of uniform thin films over large areas, which is essential for producing consistent products.
- Versatility: The method can be adapted to deposit a wide range of materials, including metals, ceramics, and polymers.
-
Challenges and Considerations:
- Cost: CVD equipment can be expensive, and the process may require high-purity gases and precursors, which can add to the cost.
- Complexity: The process requires precise control of multiple parameters, including temperature, pressure, and gas flow rates, which can be challenging to manage.
- Safety: The use of toxic or flammable gases in CVD processes requires stringent safety measures to protect operators and the environment.
In summary, the CVD method is a powerful technique for depositing high-quality materials with precise control over their properties. Its applications span a wide range of industries, from electronics to optics, and it continues to be a critical tool in the development of advanced materials and technologies. For more information on related equipment, you can explore the short path distillation system.
Summary Table:
Aspect | Details |
---|---|
Basic Principle | Chemical reactions of gaseous precursors deposit solid materials on a substrate. |
Key Components | Reactor chamber, gas delivery system, substrate holder, exhaust system. |
Types of CVD Processes | APCVD, LPCVD, PECVD. |
Applications | Semiconductors, protective coatings, optical fibers, nanomaterials. |
Advantages | High purity, uniformity, versatility. |
Challenges | Cost, complexity, safety considerations. |
Discover how CVD can revolutionize your material deposition process—contact our experts today!