Magnetron sputtering is a physical vapor deposition (PVD) technique used to deposit thin films onto substrates. It operates by bombarding a target material (cathode) with high-energy ions in a vacuum environment, causing atoms to be ejected from the target surface. These ejected atoms then travel to the substrate, where they condense to form a thin film. The process is enhanced by a magnetic field, which confines electrons near the target, increasing ionization and sustaining the plasma. This method is widely used for creating high-quality coatings in industries such as semiconductors, optics, and wear-resistant coatings.
Key Points Explained:
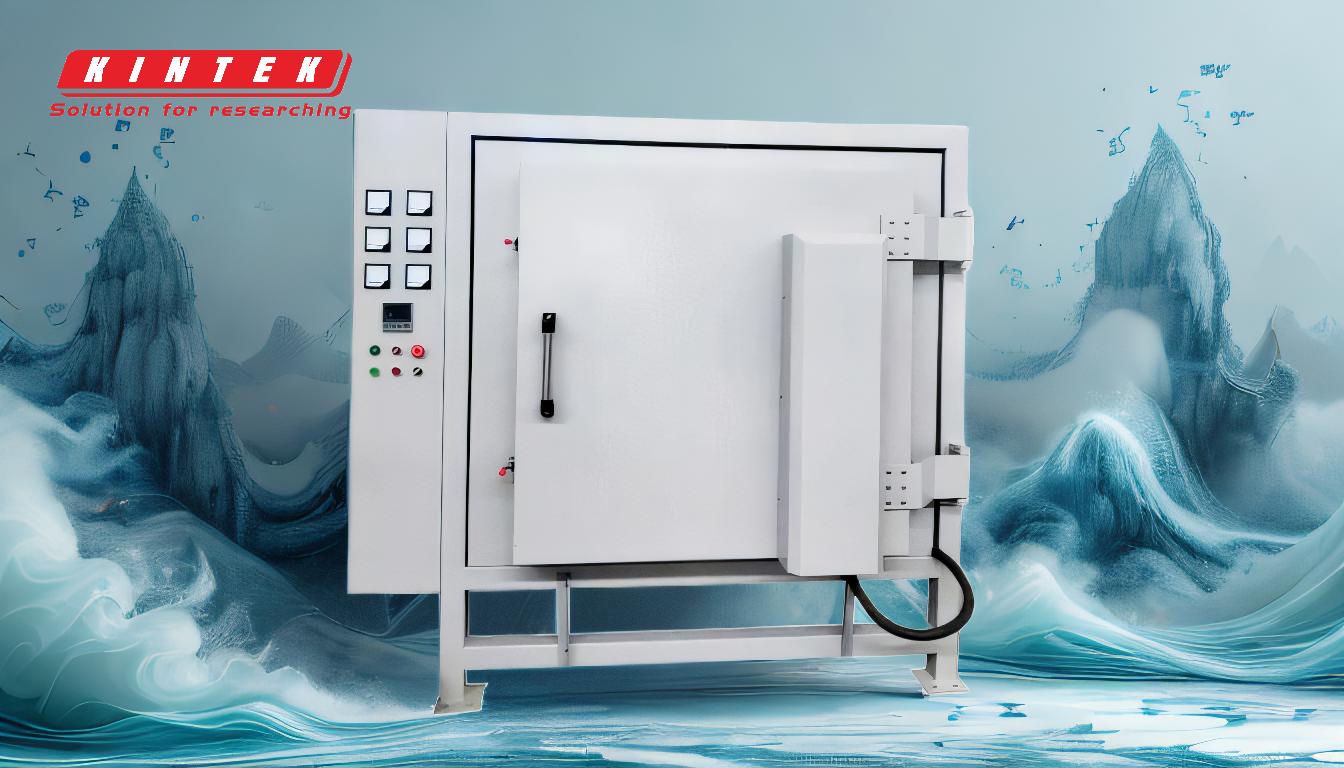
-
Basic Principle of Magnetron Sputtering:
- Magnetron sputtering involves bombarding a target material (cathode) with high-energy ions in a vacuum chamber.
- The ions are generated in a plasma, typically using an inert gas like argon.
- When the ions collide with the target surface, they transfer energy, causing atoms to be ejected from the target in a process called sputtering.
-
Role of the Magnetic Field:
- A magnetic field is applied near the target using a magnetron.
- This field forces electrons to follow a circular or cycloidal path, increasing their residence time in the plasma.
- The longer residence time enhances the probability of collisions between electrons and argon atoms, increasing ionization and sustaining the plasma.
-
Energy Transfer and Sputtering:
- The target is negatively charged (typically −300 V or more), attracting positively charged ions from the plasma.
- When these ions collide with the target surface, they transfer kinetic energy to the target atoms.
- If the transferred energy exceeds the binding energy of the target atoms, they are ejected from the surface, creating a flux of sputtered atoms.
-
Formation of Thin Films:
- The sputtered atoms travel through the vacuum chamber and deposit onto a substrate.
- The atoms condense on the substrate surface, forming a thin film of the target material.
- This process is highly controllable, allowing for precise deposition of coatings with specific properties.
-
Advantages of Magnetron Sputtering:
- High ion density in the plasma ensures efficient sputtering and high deposition rates.
- The magnetic field confinement improves energy efficiency and reduces substrate heating.
- The technique is versatile, capable of depositing a wide range of materials, including metals, alloys, and ceramics.
- It produces high-quality, uniform coatings with excellent adhesion and density.
-
Applications of Magnetron Sputtering:
- Semiconductors: Used for depositing thin films in integrated circuits and microelectronics.
- Optics: Applied in the production of anti-reflective coatings, mirrors, and optical filters.
- Wear-Resistant Coatings: Used to enhance the durability of tools, automotive parts, and industrial components.
- Decorative Coatings: Employed in the production of aesthetically pleasing finishes on consumer products.
-
Process Parameters:
- Power Supply: The voltage applied to the target determines the energy of the ions and the sputtering rate.
- Gas Pressure: The pressure of the inert gas (e.g., argon) affects the plasma density and the mean free path of the sputtered atoms.
- Magnetic Field Strength: The strength and configuration of the magnetic field influence electron confinement and plasma stability.
- Substrate Temperature: The temperature of the substrate can affect the adhesion and microstructure of the deposited film.
By understanding these key points, one can appreciate the complexity and precision of magnetron sputtering, making it a cornerstone technology in modern thin-film deposition processes.
Summary Table:
Aspect | Details |
---|---|
Basic Principle | Bombarding a target with high-energy ions in a vacuum to eject atoms. |
Role of Magnetic Field | Confines electrons, increasing ionization and sustaining the plasma. |
Energy Transfer | Ions transfer kinetic energy to eject target atoms (sputtering). |
Thin Film Formation | Sputtered atoms deposit on a substrate, forming a uniform thin film. |
Advantages | High deposition rates, energy efficiency, and versatile material deposition. |
Applications | Semiconductors, optics, wear-resistant coatings, and decorative finishes. |
Process Parameters | Power supply, gas pressure, magnetic field strength, and substrate temperature. |
Discover how magnetron sputtering can enhance your thin film processes—contact our experts today!