Chemical Vapor Deposition (CVD) is a sophisticated process used to deposit thin films of materials onto a substrate through chemical reactions in the vapor phase. The process involves several key steps, starting with the evaporation of a volatile compound, followed by thermal decomposition or chemical reactions, and culminating in the deposition of a solid film on the substrate. CVD is widely used in various industries due to its ability to produce high-quality, uniform coatings. However, it requires precise control over temperature, pressure, and gas flow, and often involves complex chemical reactions. The process is environmentally friendly but can be time-consuming and costly, making it less suitable for large-scale production without further optimization.
Key Points Explained:
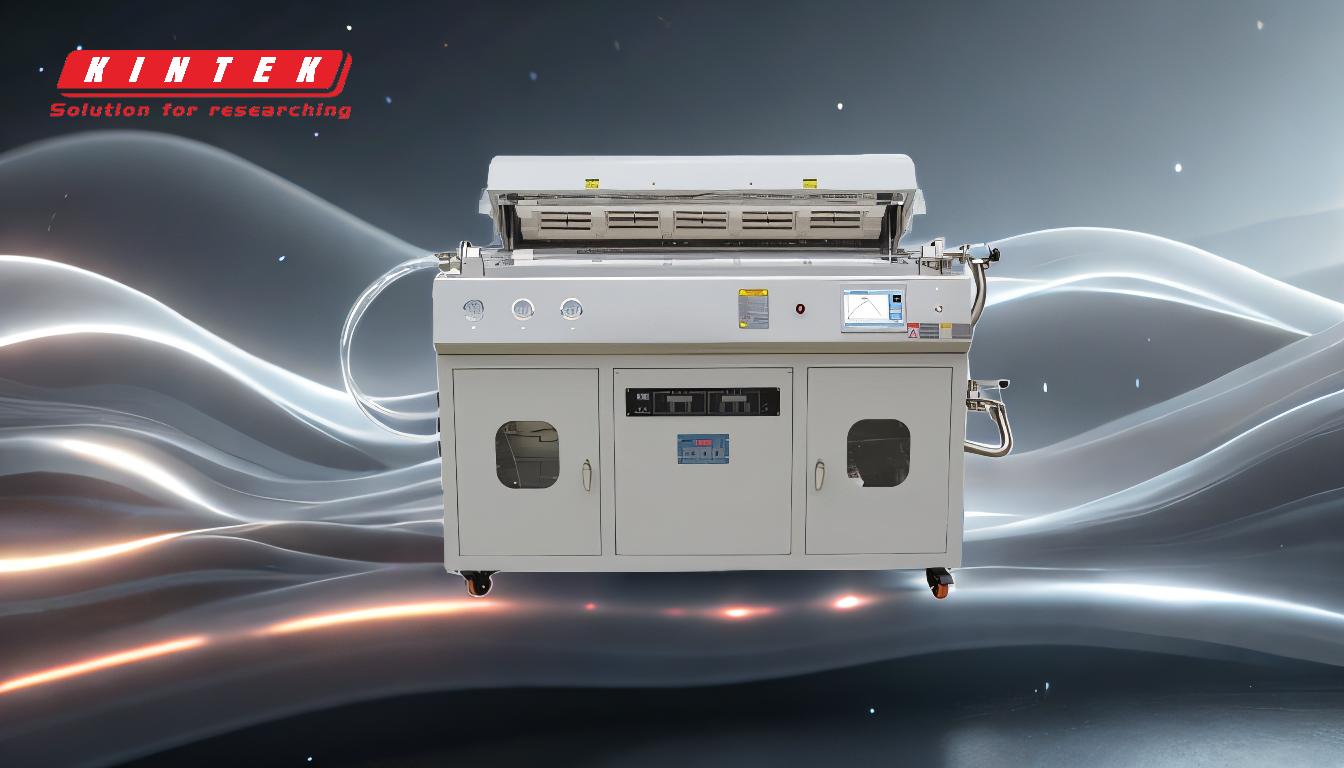
-
Evaporation of Volatile Compounds:
- The first step in the CVD process involves the evaporation of a volatile compound of the material to be deposited. This compound is typically in a gaseous state and is introduced into the reaction chamber.
- The volatile compound is chosen based on its ability to decompose or react at the substrate's surface to form the desired material.
-
Thermal Decomposition and Chemical Reactions:
- Once the volatile compound is in the vapor phase, it undergoes thermal decomposition or reacts with other gases, liquids, or vapors present in the reaction chamber.
- These reactions can include decomposition, combination, hydrolysis, oxidation, or reduction, depending on the specific requirements of the deposition process.
- The result of these reactions is the formation of reactive species that are essential for the deposition process.
-
Deposition on the Substrate:
- The reactive species formed during the chemical reactions are transported to the substrate surface, where they adsorb and undergo further surface reactions.
- These surface reactions lead to the formation of a solid film, which can be either crystalline or amorphous, depending on the process conditions.
- The deposition process is highly controlled to ensure uniformity and adherence to the substrate.
-
Transport and Adsorption:
- The reactants must be transported to the substrate surface through a boundary layer, which is a region of reduced gas flow near the surface.
- Once the reactants reach the surface, they undergo physical or chemical adsorption, which is the precursor to the formation of the solid film.
-
Desorption and By-product Removal:
- After the solid film is formed, volatile by-products are desorbed from the surface and transported back into the main gas stream.
- These by-products are then removed from the reaction chamber through convection and diffusion processes, ensuring that the deposition environment remains clean and conducive to further reactions.
-
Environmental and Economic Considerations:
- CVD is considered an environmentally friendly process because it typically uses gases and produces minimal waste.
- However, the process can be time-consuming due to the lower decomposition rates of some compounds, and it requires sophisticated equipment, which can increase production costs.
- These factors make CVD less suitable for large-scale production without further optimization, particularly for materials like LiFePO4, where uniform carbon coatings are desired.
-
Temperature and Pressure Control:
- The CVD process is conducted at elevated temperatures, often around 1925°F (1051°C), to facilitate the necessary chemical reactions.
- Precise control of temperature and pressure within the reaction chamber is crucial to ensure the quality and uniformity of the deposited film.
In summary, the CVD process is a complex and highly controlled method for depositing thin films of materials onto substrates. It involves multiple steps, from the evaporation of volatile compounds to the deposition of a solid film, and requires precise control over various parameters to achieve the desired results. While it offers many advantages, including environmental friendliness and the ability to produce high-quality coatings, it also presents challenges in terms of production time and cost, particularly for large-scale applications.
Summary Table:
Step | Description |
---|---|
1. Evaporation | Volatile compounds are evaporated and introduced into the reaction chamber. |
2. Decomposition | Compounds undergo thermal decomposition or chemical reactions in the vapor phase. |
3. Deposition | Reactive species form a solid film on the substrate surface. |
4. Transport/Adsorption | Reactants are transported and adsorbed onto the substrate. |
5. By-product Removal | Volatile by-products are desorbed and removed from the chamber. |
6. Environmental Impact | CVD is eco-friendly but can be time-consuming and costly for large-scale use. |
7. Temperature Control | Precise temperature and pressure control ensures uniform film quality. |
Learn how CVD can enhance your material coatings—contact our experts today for tailored solutions!