The processes of Cold Isostatic Pressing (CIP) and Hot Isostatic Pressing (HIP) are advanced material consolidation techniques used in various industries to achieve high-density, uniform, and defect-free components. CIP involves applying uniform hydraulic pressure to a material at room temperature, typically using a liquid medium, to shape and consolidate powdered materials. HIP, on the other hand, combines high pressure and elevated temperatures, often using an inert gas like argon, to eliminate porosity and improve material properties. Both processes are essential for producing high-performance materials, such as ceramics, alloys, and castings, with enhanced mechanical properties and structural integrity.
Key Points Explained:
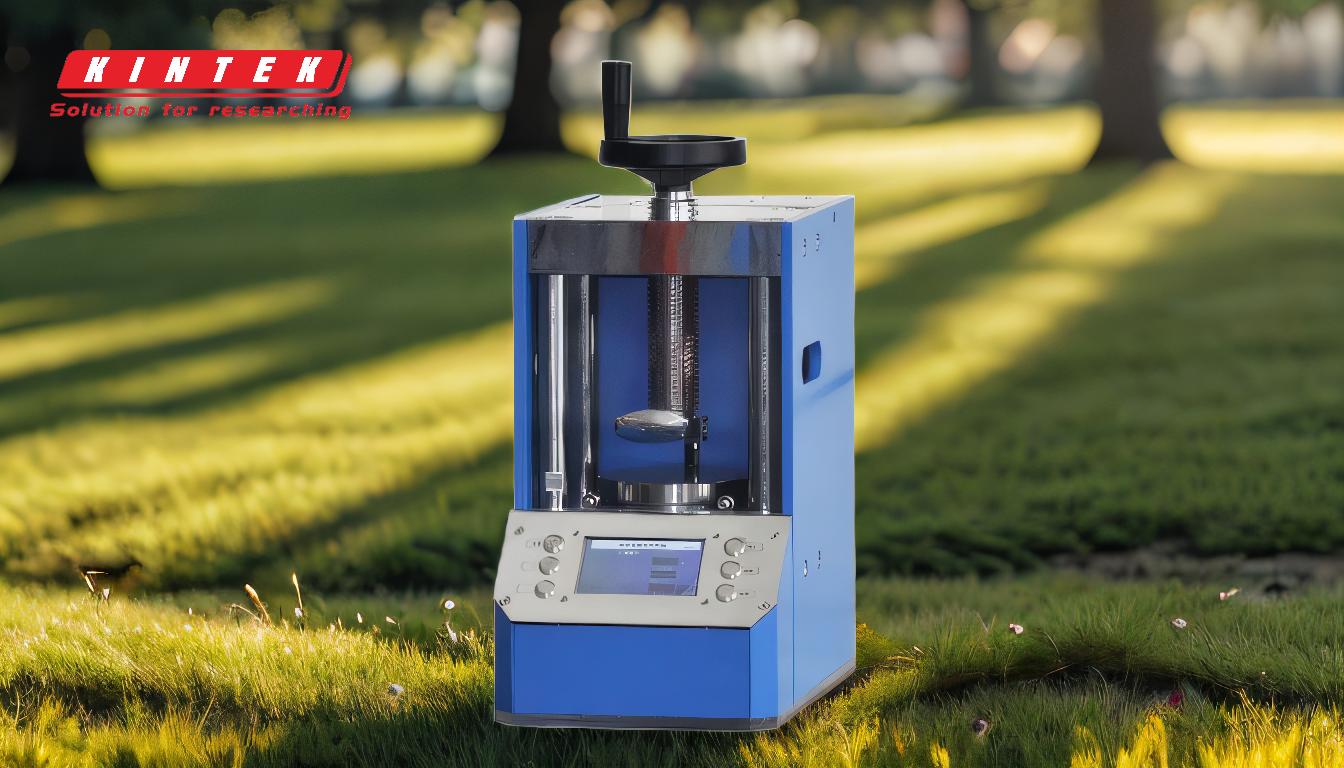
-
Cold Isostatic Pressing (CIP):
- Process Overview: CIP involves loading powdered material into a flexible mold, sealing it, and submerging it in a high-pressure fluid medium. Hydraulic pressure is applied uniformly from all directions, compacting the powder into a solid mass.
-
Key Features:
- Performed at room temperature.
- Uses a liquid medium (e.g., water or oil) to transmit pressure.
- Ideal for shaping intricate geometries and achieving high green density.
- Applications: CIP is widely used for producing ceramic components, such as zirconia and alumina ceramics, as well as consolidating metal powders for further processing.
-
Hot Isostatic Pressing (HIP):
- Process Overview: HIP applies both high pressure and elevated temperature simultaneously to a material using an inert gas (e.g., argon) in a pressurized vessel. The heat and pressure work together to eliminate porosity and improve material density.
-
Key Features:
- Operates at temperatures below the material's melting point.
- Uniform pressure from all directions ensures isotropic properties.
- Enhances mechanical properties like tensile strength, ductility, and fatigue resistance.
- Applications: HIP is commonly used for improving the quality of castings, rejuvenating worn components, and producing high-performance alloys and ceramics.
-
Comparison of CIP and HIP:
- Temperature: CIP is performed at ambient temperatures, while HIP involves elevated temperatures.
- Pressure Medium: CIP uses a liquid medium, whereas HIP uses an inert gas.
- Outcomes: CIP is primarily used for shaping and consolidating powders, while HIP focuses on eliminating defects and enhancing material properties.
-
Advantages of Isostatic Pressing:
- Uniform Density: Both CIP and HIP ensure uniform density and microstructure throughout the material.
- Complex Shapes: These processes can produce intricate shapes that are difficult to achieve with traditional methods.
- Material Versatility: Suitable for a wide range of materials, including metals, ceramics, and composites.
-
Industrial Applications:
- CIP: Used in the production of advanced ceramics, refractory materials, and metal powders for additive manufacturing.
- HIP: Applied in aerospace, automotive, and medical industries to improve the performance of critical components like turbine blades, engine parts, and orthopedic implants.
By leveraging the unique capabilities of CIP and HIP, manufacturers can produce high-quality materials with superior mechanical properties, opening new possibilities for innovation and performance optimization.
Summary Table:
Aspect | CIP (Cold Isostatic Pressing) | HIP (Hot Isostatic Pressing) |
---|---|---|
Temperature | Room temperature | Elevated temperatures (below melting point) |
Pressure Medium | Liquid (e.g., water or oil) | Inert gas (e.g., argon) |
Primary Outcome | Shapes and consolidates powders | Eliminates defects and enhances material properties |
Applications | Ceramics, metal powders, refractory materials | Aerospace, automotive, medical components |
Key Benefits | Uniform density, complex shapes, material versatility | Improved mechanical properties, defect-free materials |
Learn how CIP and HIP can optimize your material performance—contact our experts today!