Evaporation in Physical Vapor Deposition (PVD) is a process where a material is heated to its vaporization point in a vacuum environment, causing it to evaporate and subsequently condense onto a substrate to form a thin film. This method is widely used to enhance the surface properties of materials, such as hardness, durability, and resistance to corrosion and oxidation. The process involves several key steps, including the creation of a vacuum, heating the source material to evaporation, and the deposition of the vaporized material onto the substrate. Proper control of parameters like substrate temperature and vacuum conditions is crucial for achieving uniform and high-quality coatings.
Key Points Explained:
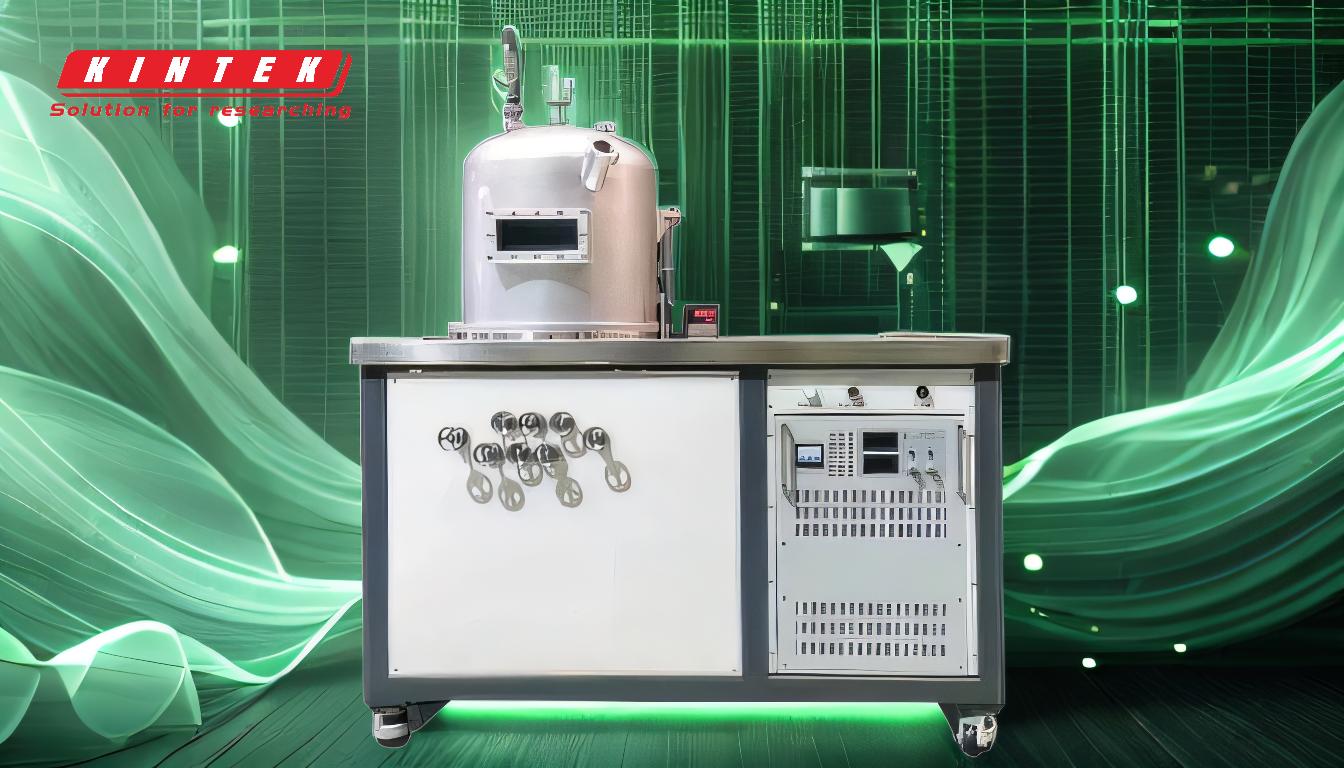
-
Understanding Evaporation in PVD:
- Evaporation is a key technique within the broader PVD process, where a solid material is transformed into a vapor phase and then deposited onto a substrate.
- The process begins with heating the source material until it evaporates, releasing atoms or molecules into the surrounding vacuum.
-
Steps in the Evaporation Process:
-
Creation of a Vacuum Environment:
- A high vacuum is essential to prevent contamination and ensure that the vaporized material travels unimpeded to the substrate.
-
Heating the Source Material:
- The source material is heated to its evaporation point, typically using resistive heating, electron beam heating, or laser heating.
-
Vaporization and Deposition:
- Once vaporized, the material diffuses through the vacuum and condenses onto the substrate, forming a thin film.
-
Substrate Preparation and Heating:
- The substrate is often heated to ensure proper adhesion and uniformity of the deposited film.
-
Creation of a Vacuum Environment:
-
Types of Evaporation Techniques:
-
Resistive Heating:
- The source material is heated using a resistive element, suitable for materials with lower melting points.
-
Electron Beam Evaporation:
- A focused electron beam is used to heat the source material, allowing for the evaporation of high-melting-point materials.
-
Laser Evaporation:
- A laser is used to vaporize the material, providing precise control over the deposition process.
-
Resistive Heating:
-
Critical Parameters in Evaporation PVD:
-
Vacuum Pressure:
- Maintaining a high vacuum is crucial to minimize collisions between vaporized particles and residual gas molecules.
-
Substrate Temperature:
- Proper heating of the substrate ensures strong adhesion and uniform film formation.
-
Deposition Rate:
- Controlling the rate at which material is deposited affects the thickness and quality of the film.
-
Vacuum Pressure:
-
Applications of Evaporation PVD:
-
Enhancing Surface Properties:
- Evaporation PVD is used to improve hardness, wear resistance, and corrosion resistance of materials.
-
Optical Coatings:
- Used in the production of mirrors, lenses, and other optical components.
-
Decorative Coatings:
- Applied to consumer products to provide a durable and aesthetically pleasing finish.
-
Enhancing Surface Properties:
-
Advantages of Evaporation PVD:
-
High Purity Films:
- The vacuum environment ensures that the deposited films are free from contaminants.
-
Versatility:
- Can be used with a wide range of materials, including metals, alloys, and ceramics.
-
Precision:
- Allows for precise control over film thickness and composition.
-
High Purity Films:
-
Challenges and Considerations:
-
Material Limitations:
- Some materials may be difficult to evaporate due to high melting points or other properties.
-
Uniformity:
- Achieving uniform film thickness can be challenging, especially on complex geometries.
-
Cost:
- The need for high vacuum and specialized equipment can make the process expensive.
-
Material Limitations:
By understanding these key points, one can appreciate the complexity and precision required in the evaporation PVD process, as well as its wide range of applications in various industries.
Summary Table:
Aspect | Details |
---|---|
Process Overview | Material is heated to vaporize in a vacuum, then condenses onto a substrate. |
Key Steps | Vacuum creation, source heating, vaporization, and deposition. |
Evaporation Techniques | Resistive heating, electron beam evaporation, laser evaporation. |
Critical Parameters | Vacuum pressure, substrate temperature, deposition rate. |
Applications | Surface hardening, optical coatings, decorative finishes. |
Advantages | High purity films, versatility, precise control. |
Challenges | Material limitations, uniformity, cost. |
Discover how evaporation PVD can transform your material performance—contact our experts today!