Heat sintering is a manufacturing process used to create solid objects from powdered materials by applying heat without melting the material completely. This process is widely used in industries such as metallurgy, ceramics, and dentistry to produce components with high strength, durability, and thermal resistance. The process involves several stages, including powder preparation, compaction, controlled heating in a sintering furnace, and cooling. The key to successful sintering lies in precise temperature control, which ensures particle bonding and densification without liquefaction. Below is a detailed explanation of the heat sintering process.
Key Points Explained:
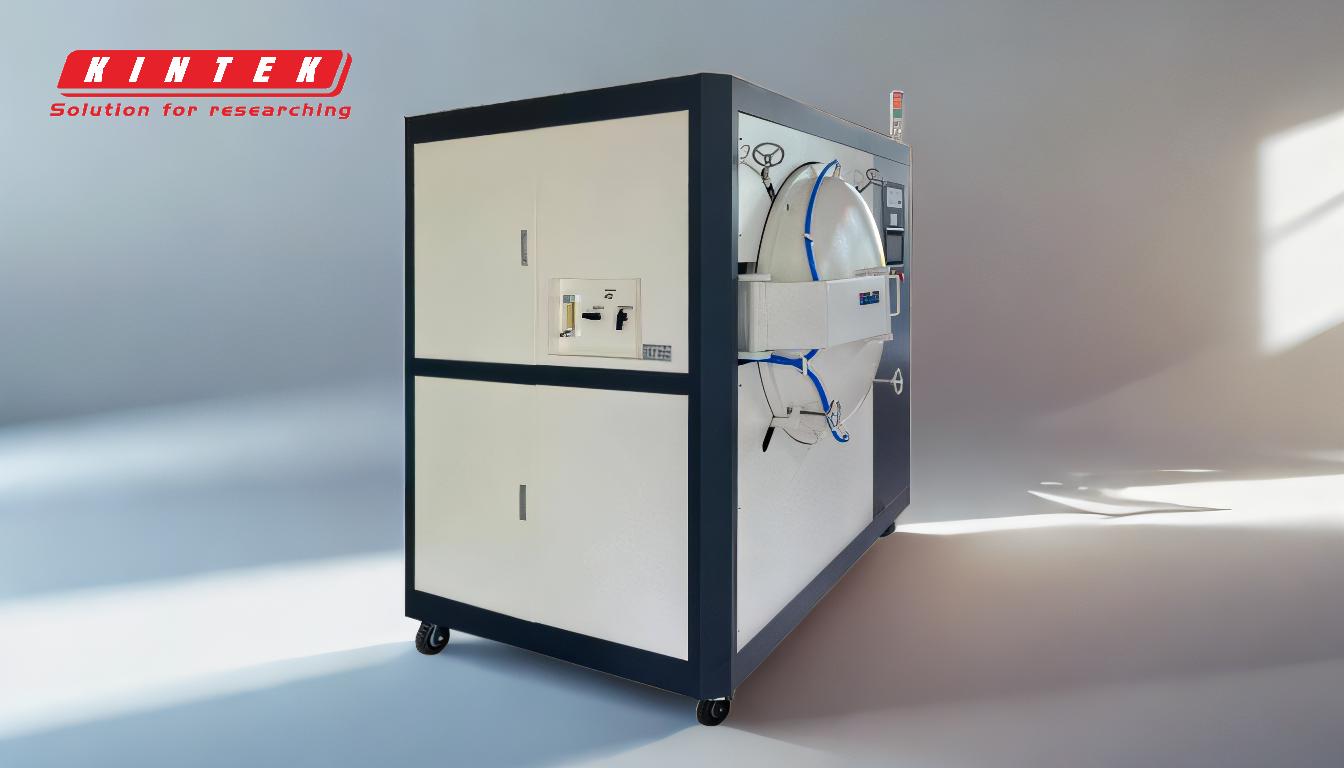
-
Preparation of the Powder Compact
- The process begins with the preparation of the raw material, typically in powdered form. This powder can be created through various methods, such as cold welding, 3D-printing, or pressing tools.
- The powder is then compacted into a specific shape using pressure to ensure uniformity and eliminate voids. This step is crucial for achieving the desired density and structural integrity in the final product.
- Compaction can occur at room temperature or under heated conditions, depending on the material and application.
-
Heating and Consolidation
- The compacted powder is placed in a sintering furnace, where it is heated to a temperature just below the material's melting point. This temperature is critical as it activates atomic diffusion across particle boundaries.
- During this stage, particles begin to bond through a process called neck formation, where material diffuses from the particle surfaces to the contact points between particles.
- For some materials, liquid phase sintering (LPS) may be used to accelerate the densification process. In LPS, a small amount of liquid phase forms at the particle boundaries, enhancing particle merging and reducing porosity.
-
Particle Merging and Densification
- As the temperature increases, particles densify and merge, reducing the overall porosity of the material. This stage is essential for achieving the desired mechanical properties, such as strength and thermal resistance.
- The degree of densification depends on factors such as temperature, time, and the material's properties. Precise control of these parameters ensures optimal results.
-
Solidification and Cooling
- After the heating stage, the material is allowed to cool gradually. This cooling process solidifies the sintered product into a single, unified mass.
- Cooling must be controlled to prevent thermal stresses that could lead to cracking or deformation.
- The final product exhibits a rigid and cohesive structure with high dimensional accuracy and mechanical strength.
-
Temperature Control in Sintering
- Temperature is a critical factor in the sintering process. It must be high enough to facilitate atomic diffusion and particle bonding but remain below the material's melting point to avoid liquefaction.
- Key temperature control points include the ignition temperature, end temperature, and exhaust gas temperature. These are carefully monitored to ensure proper sintering and high-quality output.
- Advanced sintering furnaces are equipped with precise temperature control systems to maintain consistent heating and cooling rates.
-
Applications of Sintering
- Sintering is used in various industries, including metallurgy for producing metal components, ceramics for creating thermally resistant materials, and dentistry for processing zirconia crowns and bridges.
- In dentistry, specialized dental sintering furnaces are used to achieve the extremely high temperatures required to sinter zirconia to its final hardness.
-
Advantages of Sintering
- Sintering allows for the production of complex shapes with high precision and minimal material waste.
- It enhances material properties such as strength, thermal resistance, and durability.
- The process is cost-effective and scalable for mass production.
By understanding the stages and principles of heat sintering, manufacturers can optimize the process to produce high-quality components tailored to specific applications. The use of advanced sintering furnaces and precise temperature control systems ensures consistent and reliable results.
Summary Table:
Stage | Description |
---|---|
Powder Preparation | Raw material is prepared in powdered form and compacted into a specific shape. |
Heating & Consolidation | Compacted powder is heated below melting point to activate particle bonding. |
Particle Merging | Particles densify and merge, reducing porosity and enhancing material strength. |
Cooling | Controlled cooling solidifies the material into a cohesive, high-strength product. |
Temperature Control | Precise temperature management ensures optimal densification and avoids liquefaction. |
Applications | Used in metallurgy, ceramics, and dentistry for high-performance components. |
Advantages | Produces complex shapes with minimal waste, enhances strength, and is cost-effective. |
Discover how heat sintering can revolutionize your manufacturing process—contact our experts today for more information!