The induction furnace is a critical piece of equipment in steel manufacturing, particularly for melting steel and producing alloys with precise compositions. It operates by using electrical energy to generate heat through electromagnetic induction, eliminating the need for external combustion or gases. The process involves charging steel into a crucible surrounded by a coiled copper electromagnet. When powered, the coil creates a reversing magnetic field, inducing eddy currents in the metal. These currents generate heat, melting the steel while simultaneously stirring it. Once the steel reaches the desired temperature (around 1650°C), it is tapped into a ladle for further processing. This method is efficient, clean, and allows for precise control over the melting process.
Key Points Explained:
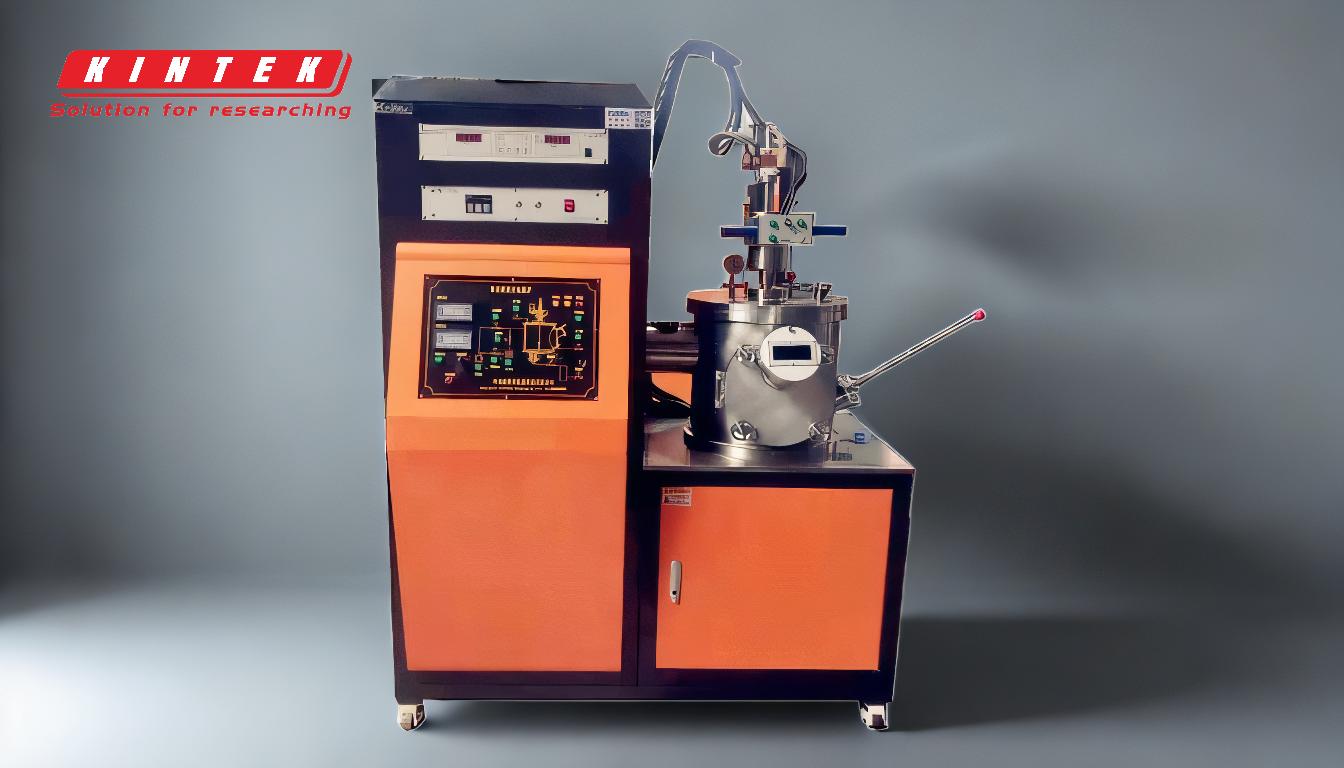
-
Basic Operation of an Induction Furnace:
- The induction furnace uses electromagnetic induction to generate heat. A high-voltage electrical source powers a primary coil, which induces a low-voltage, high-current flow in the metal (secondary coil).
- The alternating current in the coil creates a reversing magnetic field, which induces eddy currents in the metal charge. These currents generate heat due to the resistance of the metal, melting it efficiently.
-
Components of an Induction Furnace:
- Crucible: A container made of refractory material that holds the metal charge during melting.
- Copper Coil: Surrounds the crucible and carries alternating current to create the magnetic field.
- Power Supply: Provides the high-frequency alternating current required for induction heating.
- Cooling System: Ensures the coil and other components do not overheat during operation.
-
Melting Process:
- The steel charge is loaded into the crucible.
- The induction coil is powered, creating a magnetic field that induces eddy currents in the metal.
- The eddy currents generate heat, melting the steel. The magnetic field also causes self-stirring, ensuring uniform temperature and composition.
- The process continues until the steel reaches the desired temperature (typically around 1650°C).
-
Advantages of Induction Furnaces:
- Energy Efficiency: Induction furnaces convert electrical energy directly into heat with minimal losses.
- Precision: The process allows for precise control over temperature and composition, making it ideal for producing high-quality alloys.
- Clean Operation: No combustion gases or oxygen are required, reducing emissions and contamination.
- Compact Design: Induction furnaces are relatively small compared to other melting furnaces, making them suitable for foundries with limited space.
-
Applications in Steel Manufacturing:
- Induction furnaces are widely used in foundries for melting steel and producing alloys.
- They are particularly useful for small to medium-scale production, where precision and flexibility are critical.
- The ability to produce clean, high-quality steel makes induction furnaces ideal for specialized applications, such as aerospace and automotive industries.
-
Comparison with Other Steelmaking Processes:
- Electric Arc Furnace (EAF): Unlike induction furnaces, EAFs use an electric arc to generate heat. While EAFs are suitable for large-scale production, induction furnaces offer better precision and are more efficient for smaller batches.
- Blast Furnace: Blast furnaces rely on combustion and are primarily used for large-scale iron production. Induction furnaces, on the other hand, are more versatile and environmentally friendly.
-
Challenges and Limitations:
- Initial Cost: Induction furnaces require a significant initial investment in equipment and power supply.
- Maintenance: The crucible and coil require regular maintenance to ensure efficient operation.
- Scalability: While ideal for small to medium-scale production, induction furnaces may not be cost-effective for very large-scale steelmaking.
In summary, the induction furnace is a highly efficient and precise tool for steel manufacturing, offering numerous advantages in terms of energy efficiency, cleanliness, and control. Its ability to produce high-quality steel and alloys makes it indispensable in modern foundries, particularly for specialized applications. However, it is essential to consider the initial costs and maintenance requirements when choosing this technology.
Summary Table:
Aspect | Details |
---|---|
Operation | Uses electromagnetic induction to generate heat for melting steel. |
Components | Crucible, copper coil, power supply, cooling system. |
Melting Process | Steel is heated to ~1650°C, with self-stirring for uniform composition. |
Advantages | Energy-efficient, precise, clean, and compact. |
Applications | Ideal for small to medium-scale steel and alloy production. |
Challenges | High initial cost, maintenance requirements, limited scalability. |
Learn how an induction furnace can enhance your steel manufacturing process—contact us today for expert advice!