A muffle furnace is a specialized heating device used in laboratories, industrial settings, and research institutions for processes like heat treatment, material analysis, and element detection. Its design ensures that materials are heated in a contamination-free environment, making it ideal for scientific and industrial applications. The process involves heating materials in a sealed chamber, often with controlled atmospheres, to achieve specific outcomes like oxidation or melting. Key considerations when using a muffle furnace include safety features, temperature control, and the furnace's design to accommodate various materials and processes.
Key Points Explained:
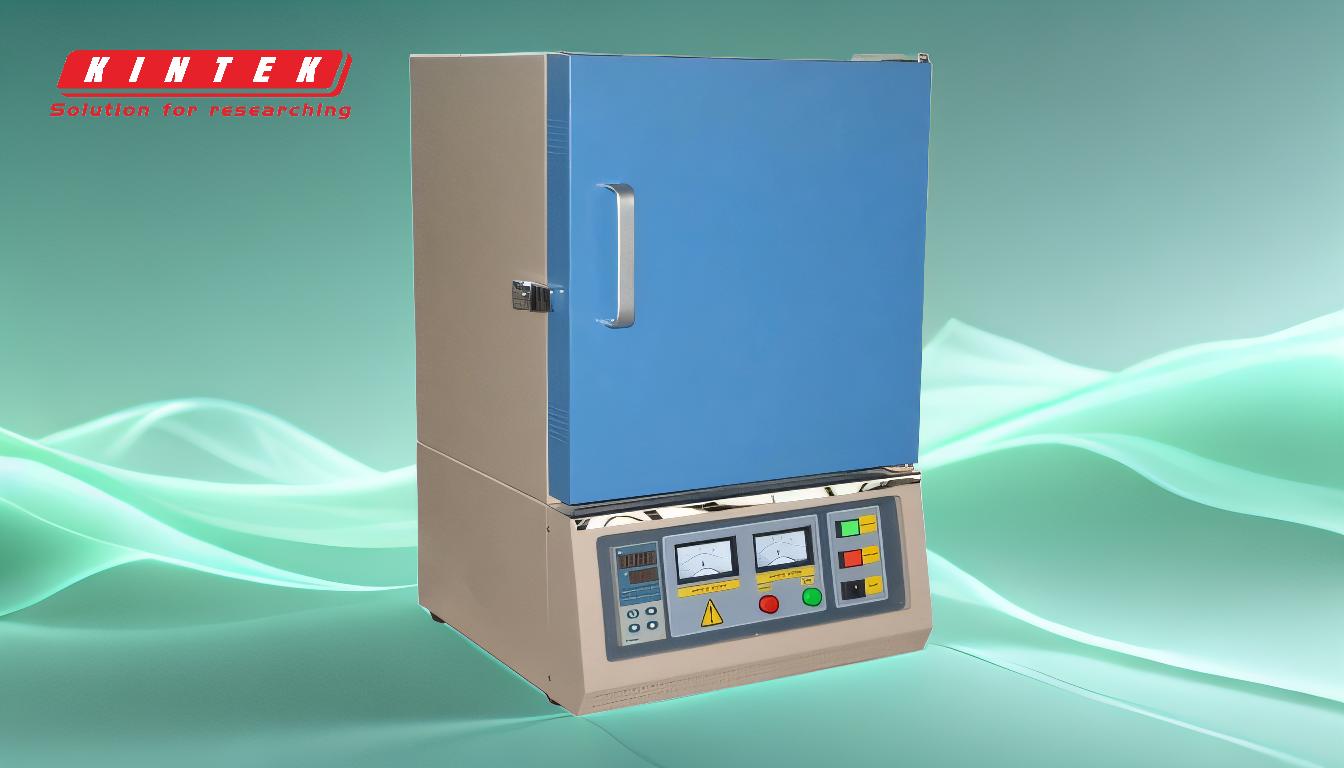
-
Purpose and Applications of a Muffle Furnace
- A muffle furnace is primarily used for heat treatment processes such as hardening, annealing, and tempering of metals.
- It is also employed in scientific research for material analysis and detecting elements in substances like coal.
- Its ability to isolate materials from combustion gases makes it suitable for contamination-sensitive applications.
-
Heating Process in a Muffle Furnace
- The furnace heats materials in a sealed chamber equipped with burners and lances, which create controlled atmospheres (e.g., oxygen and hydrogen) to promote oxidation or other chemical reactions.
- After heating, materials can be melted and shaped into desired forms, such as sheets or molds.
-
Advantages of Using a Muffle Furnace
- High-temperature processing: Capable of reaching very high temperatures quickly, making it efficient for various industrial and laboratory tasks.
- Durability: Built to withstand rigorous use in demanding environments.
- Versatility: Suitable for a wide range of materials and applications, from metal treatment to scientific research.
-
Design Features of a Muffle Furnace
- The furnace chamber includes racks for organizing materials, ensuring even heating and complete combustion.
- Doors can be designed to open in multiple directions (downward, upward, or sideways) for easy loading and unloading of samples.
- Safety features like gas-tight doors and positive pressure maintenance prevent accidents and ensure controlled environments.
-
Historical and Functional Significance
- Historically, muffle furnaces were designed to isolate materials from combustion byproducts like ash and soot, ensuring contamination-free heating.
- Modern muffle furnaces maintain this principle by separating the combustion and heating chambers, making them ideal for precise scientific experiments and industrial processes.
-
Choosing the Right Muffle Furnace
- The selection depends on the intended purpose, such as the type of materials to be processed and the required temperature range.
- Safety features, chamber design, and ease of operation are critical factors to consider when purchasing a muffle furnace.
By understanding these key points, users can effectively utilize a muffle furnace for their specific needs, ensuring optimal performance and safety in their applications.
Summary Table:
Aspect | Details |
---|---|
Purpose | Heat treatment, material analysis, and element detection. |
Heating Process | Sealed chamber with controlled atmospheres for oxidation, melting, etc. |
Advantages | High-temperature processing, durability, and versatility. |
Design Features | Racks for even heating, multi-directional doors, and safety mechanisms. |
Applications | Metal treatment, scientific research, and contamination-sensitive tasks. |
Selection Criteria | Temperature range, safety features, and chamber design. |
Discover how a muffle furnace can enhance your lab or industrial processes—contact us today for expert guidance!