Physical Vapor Deposition (PVD) metallization is a sophisticated process used to deposit thin films of material onto a substrate. This process is widely utilized in various industries, including electronics, optics, and tool manufacturing, to enhance the properties of surfaces, such as hardness, wear resistance, and electrical conductivity. The PVD process typically involves several key steps: cleaning the substrate, creating a vapor from the target material, reacting the vapor with gases to form a compound, and depositing the compound onto the substrate. Each step is crucial to ensure the quality and performance of the final coating.
Key Points Explained:
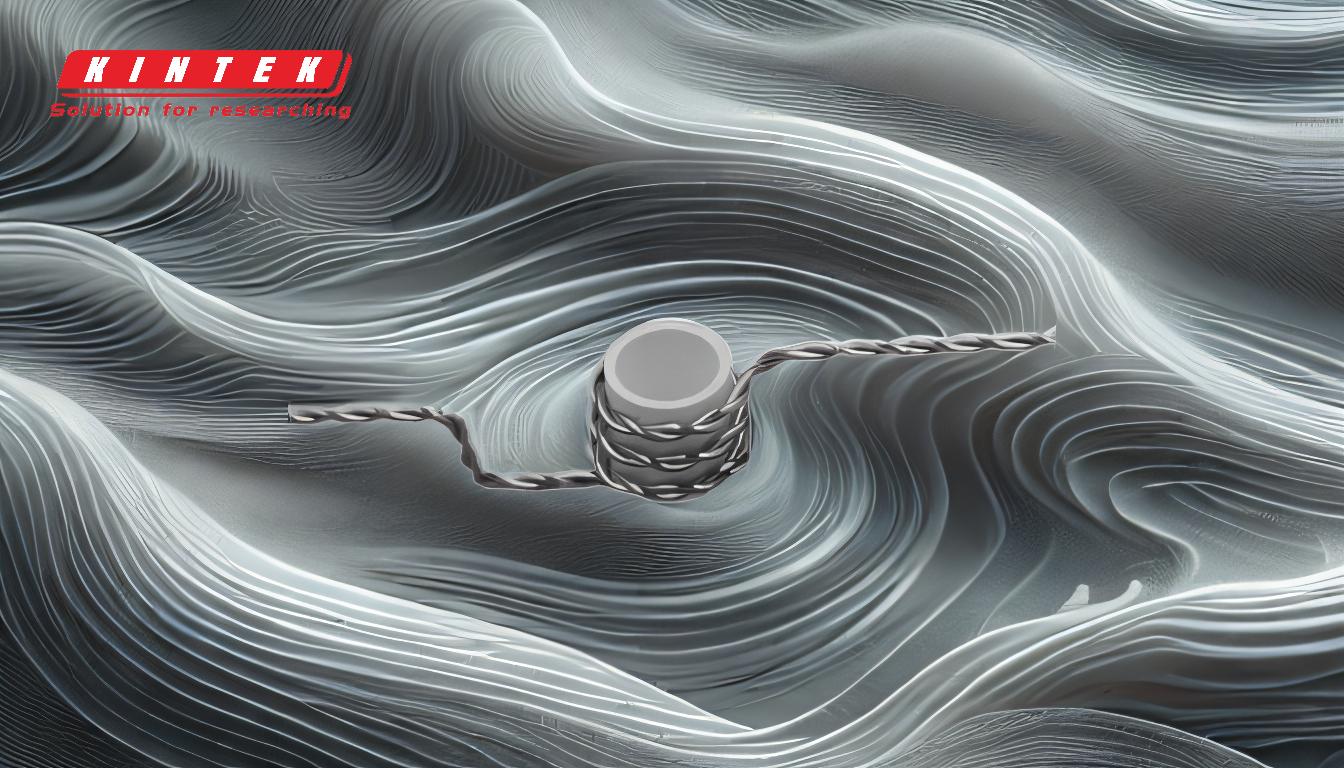
-
Substrate Cleaning:
- Purpose: The first step in the PVD process is to clean the substrate thoroughly. This is essential to remove any contaminants, such as oils, dust, or oxides, that could interfere with the adhesion and quality of the coating.
- Methods: Cleaning can be done using various techniques, including ultrasonic cleaning, chemical cleaning, or plasma cleaning. The choice of method depends on the type of substrate and the level of cleanliness required.
-
Vaporization of the Target Material:
- Process: The target material, which is the substance to be deposited, is vaporized. This is typically achieved by creating a plasma in a vacuum chamber. The plasma is generated using high-power electricity or a laser, which ionizes the gas and creates high-energy electrons.
- Mechanism: These high-energy electrons collide with the gas molecules, causing them to dissociate into atoms. The target material is then vaporized, either by sputtering (where ions bombard the target, knocking off atoms) or by evaporation (where the target is heated until it vaporizes).
-
Reaction with Gaseous Species:
- Introduction of Reactive Gas: After the target material is vaporized, a reactive gas (such as nitrogen or oxygen) is introduced into the chamber. This gas reacts with the vaporized atoms to form a compound.
- Formation of Compound: The reaction between the vaporized atoms and the reactive gas determines the properties of the final coating, such as its hardness, color, and chemical composition. For example, if titanium is the target material and nitrogen is the reactive gas, the resulting compound would be titanium nitride (TiN), which is known for its hardness and gold-like appearance.
-
Deposition onto the Substrate:
- Mechanism: The compound formed in the previous step is then deposited onto the substrate. This occurs atom by atom, ensuring a uniform and thin film. The deposition process is controlled to achieve the desired thickness and properties of the coating.
- Environment: The entire process takes place in a vacuum chamber to prevent contamination and to control the reaction environment precisely.
-
Testing and Quality Control:
- Batch Testing: After the coating is applied, each batch of components is tested for consistency. This ensures that the coating meets the required specifications in terms of composition, thickness, and color.
- Analytical Tools: Tools such as X-ray fluorescence (XRF) machines and spectrophotometers are used to analyze the coating. XRF can determine the elemental composition and thickness of the coating, while a spectrophotometer can measure the color and reflectivity.
-
High-Temperature Vacuum Conditions:
- Importance: The PVD process is performed under high-temperature vacuum conditions to ensure the stability and quality of the coating. The vacuum environment prevents oxidation and contamination, while the high temperature aids in the vaporization and reaction processes.
- Equipment: The vacuum chamber is equipped with heating elements and precise control systems to maintain the required conditions throughout the process.
In summary, the PVD metallization process is a multi-step procedure that involves cleaning the substrate, vaporizing the target material, reacting it with a gas to form a compound, and depositing this compound onto the substrate. Each step is critical to achieving a high-quality, durable coating with the desired properties. The process is carried out under controlled vacuum and high-temperature conditions to ensure the best results.
Summary Table:
Step | Description |
---|---|
Substrate Cleaning | Remove contaminants using ultrasonic, chemical, or plasma cleaning methods. |
Vaporization | Vaporize target material via sputtering or evaporation in a vacuum chamber. |
Reaction with Gas | Introduce reactive gas (e.g., nitrogen) to form a compound (e.g., TiN). |
Deposition | Deposit the compound onto the substrate atom by atom for uniform coating. |
Testing & Quality | Analyze coating thickness, composition, and color using XRF and spectrophotometry. |
High-Temperature Vacuum | Maintain vacuum and high-temperature conditions for optimal coating stability. |
Discover how PVD metallization can enhance your product's performance—contact our experts today!