The rotary calciner process involves using a rotary kiln to heat materials to high temperatures, causing chemical dissociation or physical changes such as moisture removal. The process relies on a rotating drum, slightly inclined to allow material flow, and is heated either internally or externally. The material tumbles inside the drum, ensuring uniform exposure to heat, while controlled temperature and retention time ensure the desired reaction. Rotary calciners are commonly used for inorganic materials like limestone, dolomite, and magnesite, producing uniform products efficiently.
Key Points Explained:
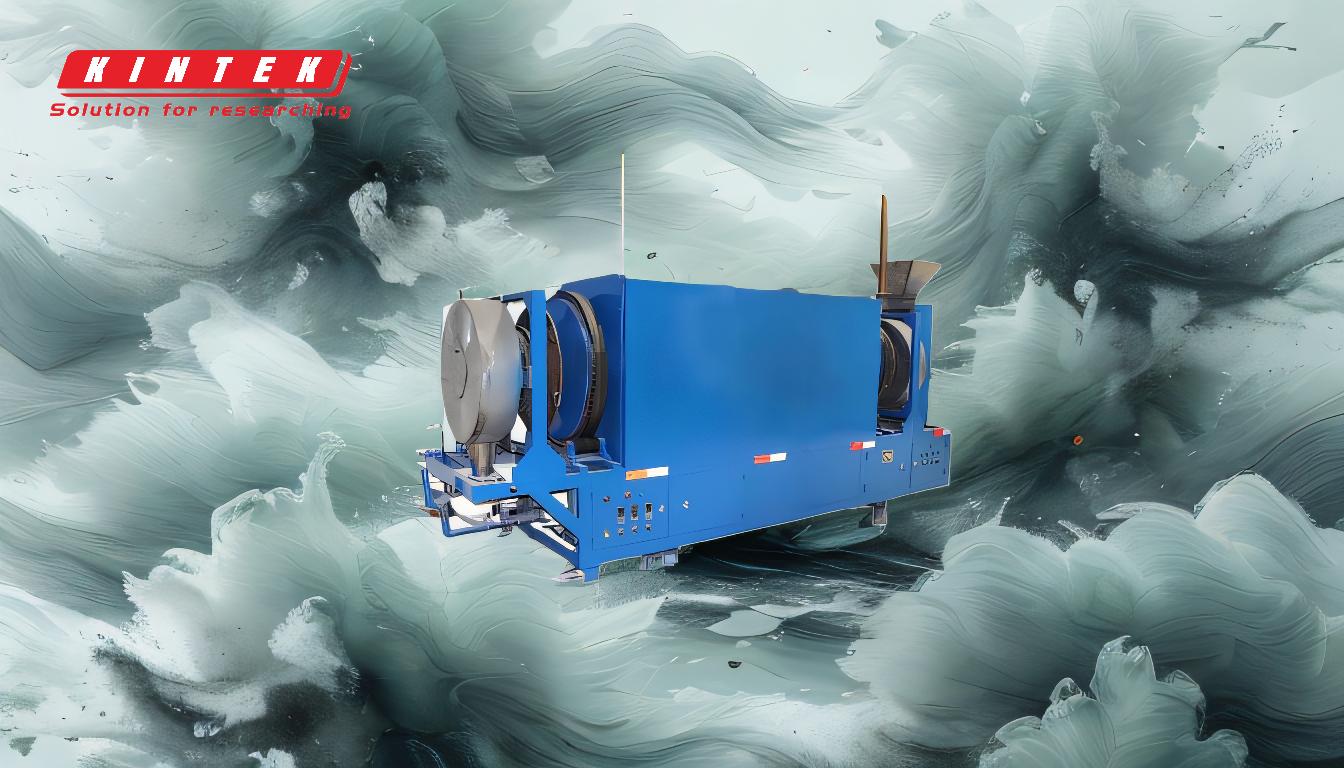
-
Core Function of Rotary Calciners:
- Rotary calciners are designed to heat materials to high temperatures, enabling chemical dissociation or physical changes such as moisture removal.
- This process is particularly useful for inorganic materials like calcium carbonate, which dissociates into calcium oxide and carbon dioxide.
-
Rotary Kiln Structure and Operation:
- The rotary kiln is a large, hollow, cylindrical drum that rotates slowly about its longitudinal axis.
- It is slightly inclined to allow gravity to assist in moving the material from the upper end (feedstock entry) to the lower end (exit port).
- The rotation ensures tumbling and mixing of the material, promoting uniform heat exposure.
-
Heating Mechanisms:
- Heating can be achieved through direct or indirect methods:
- Direct Heating: Hot gases are generated inside the kiln or introduced from an external furnace.
- Indirect Heating: Heat is applied externally to the drum, avoiding direct contact between the material and the heat source.
- The direction of hot gases can be co-current (same direction as material flow) or counter-current (opposite direction), depending on the desired thermal efficiency and reaction control.
- Heating can be achieved through direct or indirect methods:
-
Temperature and Retention Time:
- The temperature and retention time are predetermined based on chemical and thermal analyses of the material.
- These parameters ensure the material reaches the required state, whether for chemical dissociation or moisture removal.
- The kiln's sealed design helps maintain a controlled atmosphere, optimizing the reaction conditions.
-
Applications of Rotary Calciners:
- Rotary calciners are widely used in industries requiring high-temperature processing, such as:
- Cement Production: Calcination of limestone to produce lime.
- Mineral Processing: Processing of dolomite, magnesite, and other minerals.
- Chemical Manufacturing: Production of inorganic compounds and removal of bound moisture from materials like borax.
- Rotary calciners are widely used in industries requiring high-temperature processing, such as:
-
Advantages of Rotary Calciners:
- Uniform Product Quality: The tumbling action ensures consistent heat distribution, resulting in a uniform product.
- High Processing Rates: Rotary calciners can handle large volumes of material efficiently, making them suitable for industrial-scale operations.
- Versatility: They can process a wide range of materials and particle sizes, typically up to 60 mm.
-
Operational Considerations:
- Material Feed Rate: The rate at which material is fed into the kiln must be controlled to match the retention time and temperature requirements.
- Kiln Rotation Speed: The speed of rotation affects the tumbling action and material flow, influencing heat exposure and reaction efficiency.
- Heat Source Management: The choice of heat source (direct or indirect) and gas flow direction (co-current or counter-current) impacts energy efficiency and process control.
By understanding these key points, a purchaser can evaluate the suitability of rotary calciners for their specific needs, considering factors like material type, desired output, and operational efficiency.
Summary Table:
Aspect | Details |
---|---|
Core Function | Heats materials for chemical dissociation or physical changes like moisture removal. |
Structure | Rotating drum, slightly inclined for material flow and uniform heat exposure. |
Heating Mechanisms | Direct (internal) or indirect (external) heating methods. |
Applications | Cement production, mineral processing, and chemical manufacturing. |
Advantages | Uniform product quality, high processing rates, and versatility. |
Operational Factors | Material feed rate, kiln rotation speed, and heat source management. |
Ready to optimize your material processing? Contact us today to learn more about rotary calciners!