Sintering is a manufacturing process that involves compacting and forming a solid mass of material by heat or pressure without melting it to the point of liquefaction. This process is widely used in the production of metal, ceramic, and composite materials. The sintering process typically involves several key steps, including powder preparation, compaction, and heating in a sintering furnace to bond particles together. The process can be broken down into stages such as blending, compaction, heating, and cooling, each of which plays a crucial role in achieving the desired material properties. Sintering is essential for creating strong, durable materials with minimal porosity and enhanced mechanical properties.
Key Points Explained:
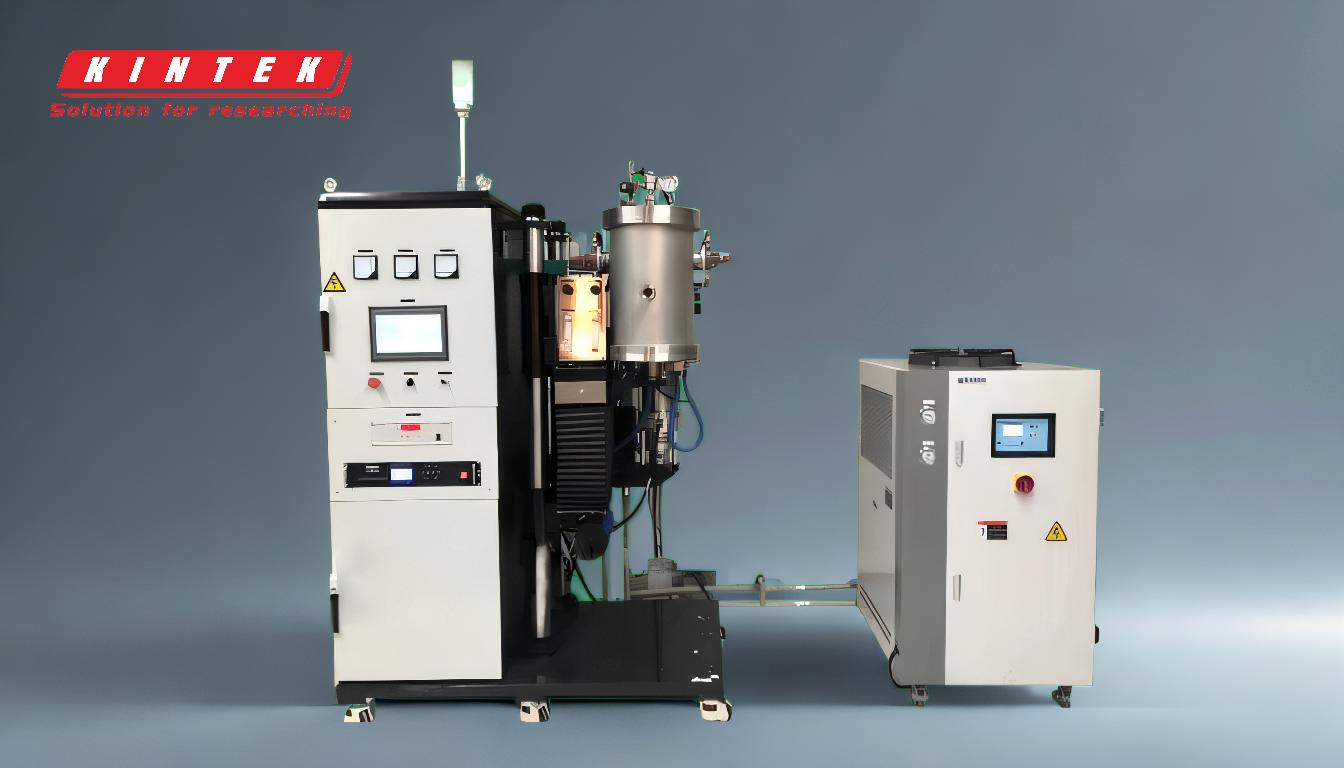
-
Powder Preparation:
- The process begins with the preparation of powdered materials, which can be metals, ceramics, or composites. The powder is often mixed with additives such as binders, lubricants, or alloying elements to improve its properties. For example, in metal sintering, powdered metals are blended with alloying elements to achieve specific mechanical properties.
-
Compaction:
- The prepared powder is then compacted into a desired shape using high pressure. This can be done using molds, dies, or pressing tools. The compaction process ensures that the powder particles are in close contact, which is crucial for the subsequent bonding during sintering. The compacted part, often referred to as a "green body," is still porous and lacks the final mechanical strength.
-
Heating in a Sintering Furnace:
- The green body is then placed in a sintering furnace, where it is heated to a temperature below the melting point of the primary material. The heat causes the particles to bond at their surfaces, reducing porosity and increasing density. In some cases, a liquid phase may form, which helps to accelerate the bonding process. The temperature and duration of heating are carefully controlled to achieve the desired material properties.
-
Bonding and Densification:
- During the heating process, the particles begin to bond through mechanisms such as diffusion, surface tension, and grain boundary migration. This stage is critical for achieving the final density and mechanical strength of the material. The bonding process can be enhanced by the presence of a liquid phase or intermediate bonding agents, which help to fill in any remaining pores.
-
Cooling and Solidification:
- After the bonding process is complete, the material is allowed to cool and solidify. The cooling rate can affect the final microstructure and properties of the material. Controlled cooling is often used to prevent the formation of internal stresses or cracks. The final product is a dense, strong material with minimal porosity and enhanced mechanical properties.
-
Post-Sintering Treatments:
- In some cases, additional treatments such as machining, surface finishing, or heat treatment may be applied to the sintered part to achieve the desired final properties. These treatments can further enhance the material's strength, durability, and surface quality.
The sintering process is a versatile and essential technique in materials science and manufacturing, allowing for the production of complex shapes and high-performance materials with tailored properties. The use of a sintering furnace is crucial in this process, providing the controlled environment needed for the successful bonding and densification of materials.
Summary Table:
Step | Description |
---|---|
Powder Preparation | Prepare powdered materials (metals, ceramics, composites) with additives. |
Compaction | Compact powder into a shape using high pressure to form a porous 'green body.' |
Heating | Heat in a sintering furnace below melting point to bond particles. |
Bonding & Densification | Particles bond via diffusion, surface tension, and grain boundary migration. |
Cooling | Cool and solidify the material to achieve final density and strength. |
Post-Sintering | Apply treatments like machining or heat treatment for enhanced properties. |
Discover how sintering can transform your materials—contact our experts today!