Sintering is a thermal process used to create solid objects from powdered materials by heating them below their melting point. This allows particles to bond through atomic diffusion, forming a dense, low-porosity structure. The process is widely used in manufacturing ceramics, metals, and plastics, particularly for materials with high melting points. Sintering involves several stages, including powder preparation, compression, heating, and solidification. It enhances material strength and structural integrity by reducing porosity and fusing particles into a unified mass. The process can be accelerated using techniques like liquid phase sintering (LPS) and is essential for producing complex shapes and high-performance materials.
Key Points Explained:
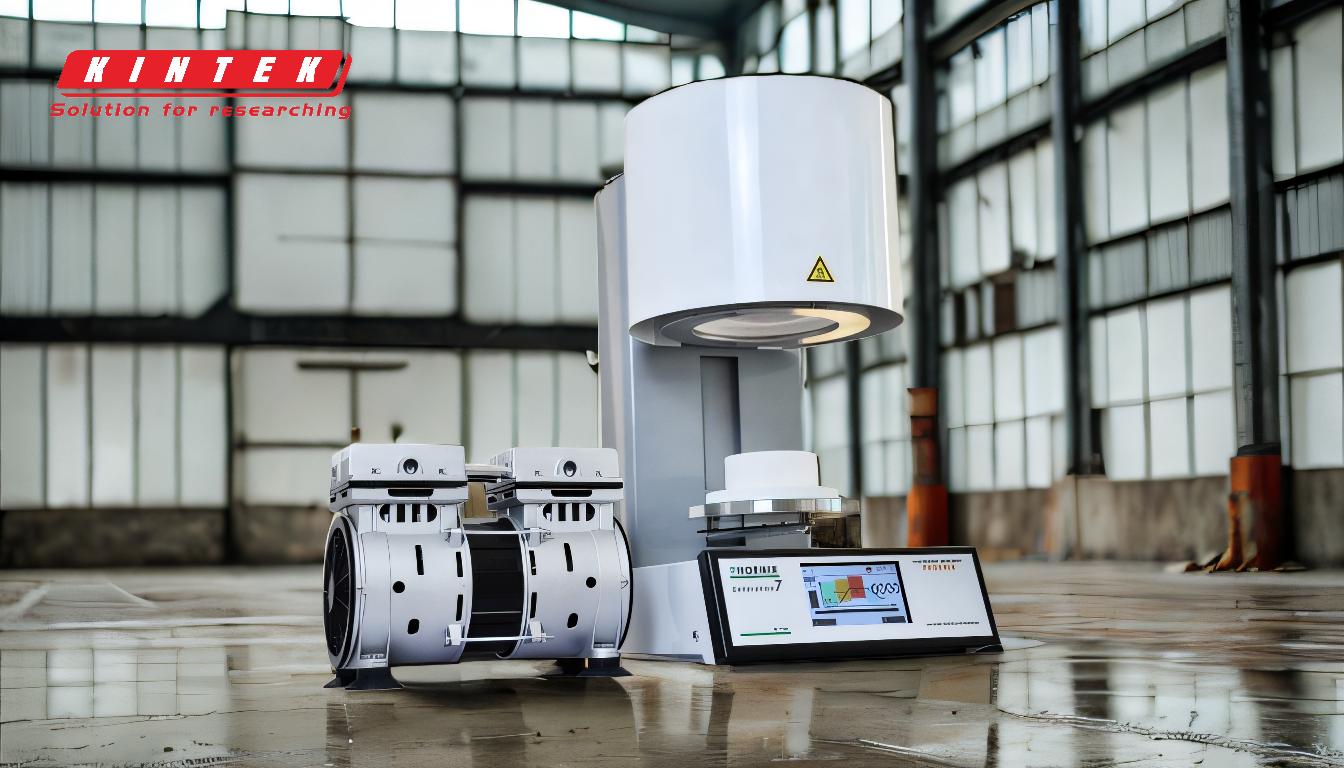
-
Definition and Purpose of Sintering:
- Sintering is a process that fuses powdered materials into a solid mass using heat and pressure without melting the material.
- It is used to create dense, strong, and low-porosity structures, particularly for materials with high melting points like ceramics, metals, and sintered plastics.
-
Stages of the Sintering Process:
- Powder Preparation: The raw material is ground into fine powder and mixed with coupling agents or binders if necessary.
- Compression: The powder is pressed into the desired shape using molds, cold welds, or 3D-printed lasers.
- Heating and Consolidation: The compacted powder is heated to a temperature just below its melting point, allowing atomic diffusion to bond particles.
- Particle Merging: Particles densify and merge, reducing porosity and forming a solid structure. Techniques like liquid phase sintering (LPS) can accelerate this step.
- Solidification: The material cools and solidifies into a unified, dense mass.
-
Mechanism of Sintering:
- Atoms in the powdered material diffuse across particle boundaries due to elevated temperatures, fusing particles together.
- This solid-state diffusion mechanism reduces porous spaces between particles, compacting the material into a solid lump.
-
Applications of Sintering:
- Ceramics: Used to produce high-strength, heat-resistant components like tiles, insulators, and cutting tools.
- Metals: Commonly used for manufacturing parts with complex shapes, such as gears, bearings, and filters.
- Plastics: Sintered plastics are used in applications requiring lightweight, durable materials, such as automotive components and medical devices.
-
Advantages of Sintering:
- Enhanced Material Properties: Sintering improves strength, durability, and structural integrity by reducing porosity.
- Cost-Effective: It allows for the production of complex shapes with minimal material waste.
- Versatility: Suitable for a wide range of materials, including those with extremely high melting points.
-
Techniques to Enhance Sintering:
- Liquid Phase Sintering (LPS): Introduces a liquid phase to accelerate particle bonding and densification.
- Controlled Atmosphere: Prevents oxidation and contamination during the sintering process.
- High-Pressure Compression: Ensures uniform density and shape retention in the final product.
-
Natural vs. Industrial Sintering:
- Natural Sintering: Occurs in mineral deposits over geological timescales due to heat and pressure.
- Industrial Sintering: A controlled process used in manufacturing to produce high-performance materials and components.
By understanding these key points, a purchaser of equipment or consumables can make informed decisions about the sintering process, ensuring the selection of appropriate materials and techniques for their specific applications.
Summary Table:
Aspect | Details |
---|---|
Definition | A process that bonds powdered materials using heat and pressure. |
Stages | Powder Preparation, Compression, Heating, Solidification. |
Applications | Ceramics, Metals, Plastics (e.g., tiles, gears, automotive parts). |
Advantages | Enhanced strength, cost-effectiveness, versatility. |
Enhancement Techniques | Liquid Phase Sintering (LPS), Controlled Atmosphere, High-Pressure Compression. |
Unlock the potential of sintering for your materials—contact our experts today!