The sintering process is a critical manufacturing technique used to transform powdery materials into dense, solid bodies by applying heat and pressure below the material's melting point. It involves several stages, including the preparation of a powder blend with a bonding agent, shaping the material into a desired form, heating to remove the bonding agent, and fusing the primary particles to create a low-porosity, unified mass. This process is widely used in industries such as powder metallurgy and ceramics to produce durable and high-strength components. The key steps include composition, compression, heating, particle merging, and solidification, each contributing to the final material's properties.
Key Points Explained:
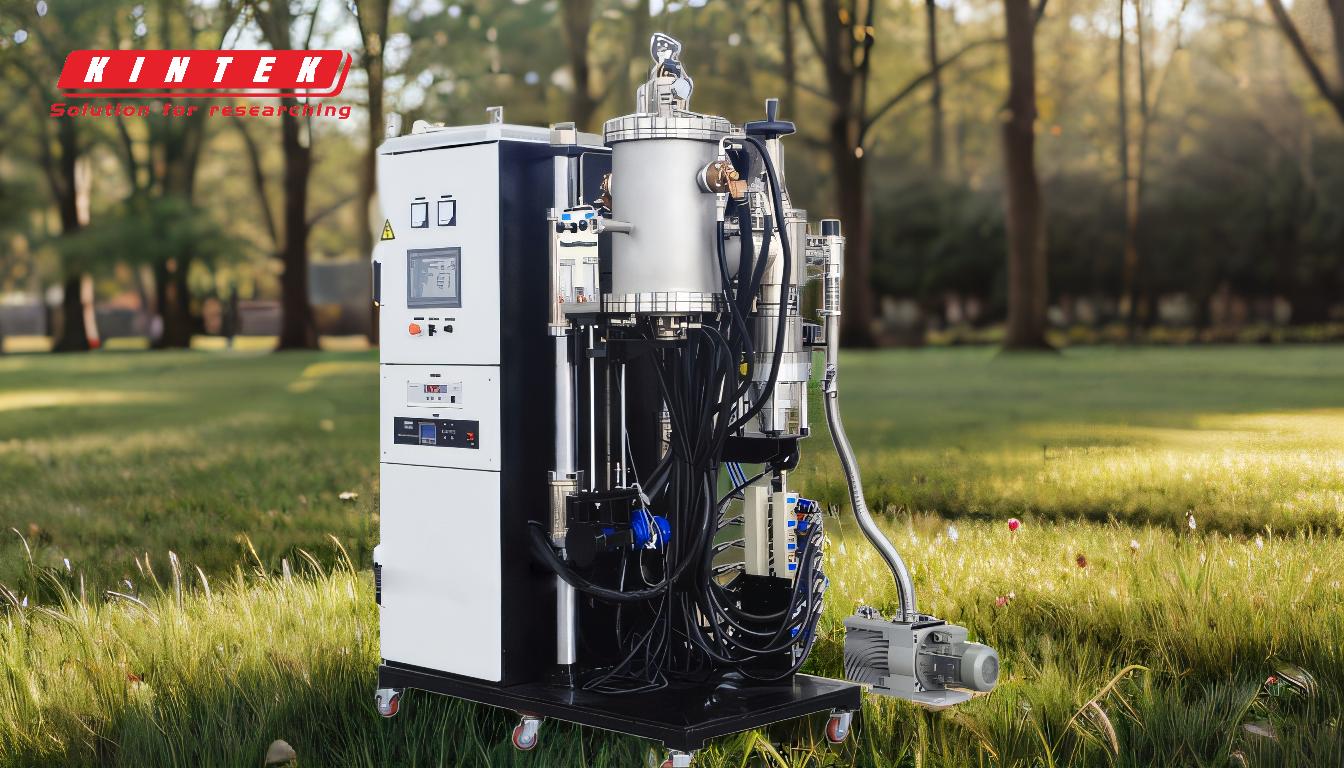
-
Preparation of the Powder Blend:
- Composition: The process begins by mixing primary materials (such as metal or ceramic powders) with a bonding agent (e.g., wax or polymer). The bonding agent helps the powder particles adhere to each other, forming a cohesive blend.
- Shaping: The powder blend is then shaped into the desired form using techniques like cold pressing, 3D printing, or other forming methods. This creates a "green part," which is a preliminary structure that holds its shape but is not yet fully dense.
-
Compression and Forming:
- Compression: The green part is compressed to achieve the required shape and density. This step ensures that the particles are closely packed, reducing porosity and preparing the material for the heating phase.
- Controlled Atmosphere: In some cases, compression occurs in a controlled atmosphere to prevent oxidation or contamination, which could affect the material's properties.
-
Heating and Removal of the Bonding Agent:
- Initial Heating: The green part is heated to a temperature where the bonding agent evaporates or burns away. This step is crucial for eliminating any organic materials that could interfere with the sintering process.
- Temperature Control: The temperature is carefully controlled to ensure that the bonding agent is fully removed without damaging the primary material.
-
Particle Merging and Fusion:
-
Sintering Temperature: The temperature is then raised to just below the material's melting point. At this stage, one of two processes occurs:
- Solid-State Sintering: The primary particles begin to fuse at their surfaces due to atomic diffusion, creating a denser structure.
- Liquid Phase Sintering (LPS): An intermediate bonding agent, such as bronze, melts and flows between the particles, bonding them together while the primary material remains solid.
- Densification: The particles densify and merge, reducing porosity and increasing the material's strength and durability.
-
Sintering Temperature: The temperature is then raised to just below the material's melting point. At this stage, one of two processes occurs:
-
Solidification and Cooling:
- Cooling Phase: After the sintering process is complete, the material is allowed to cool and solidify into a unified mass. This step ensures that the material retains its shape and properties.
- Final Properties: The final product is a dense, low-porosity material with enhanced mechanical properties, such as hardness, strength, and durability.
-
Applications and Benefits:
- Industrial Use: Sintering is widely used in powder metallurgy for producing metal components and in ceramic manufacturing for creating durable ceramic products.
- High Melting Point Materials: This process is particularly useful for materials with extremely high melting points, such as tungsten and molybdenum, which are difficult to process using traditional melting techniques.
- Customization: Sintering allows for the production of complex shapes and customized components, making it a versatile manufacturing method.
By following these steps, the sintering process transforms loose powders into strong, dense materials suitable for a wide range of industrial applications. The careful control of temperature, pressure, and atmosphere ensures that the final product meets the desired specifications and performance requirements.
Summary Table:
Stage | Key Details |
---|---|
Preparation | Mix primary materials with a bonding agent and shape into a 'green part.' |
Compression | Compress the green part to reduce porosity and achieve desired density. |
Heating | Heat to remove the bonding agent and prepare for particle fusion. |
Particle Merging | Raise temperature to fuse particles via solid-state or liquid phase sintering. |
Solidification | Cool and solidify into a dense, low-porosity material with enhanced properties. |
Applications | Used in powder metallurgy and ceramics for durable, high-strength components. |
Discover how sintering can enhance your manufacturing process—contact us today for expert guidance!