A fluidized bed is a versatile and widely used technology in various industrial processes, primarily due to its efficient heat and mass transfer capabilities. It consists of solid particles suspended in a fluid (usually a gas or liquid), creating a fluid-like state that enhances mixing, heat transfer, and chemical reactions. Fluidized beds are employed in applications such as combustion, drying, granulation, coating, and chemical synthesis. Their purpose is to improve process efficiency, uniformity, and scalability, making them ideal for industries like pharmaceuticals, energy, food processing, and materials manufacturing. The fluidized state allows for precise control over temperature, particle size, and reaction kinetics, ensuring consistent product quality and optimized energy usage.
Key Points Explained:
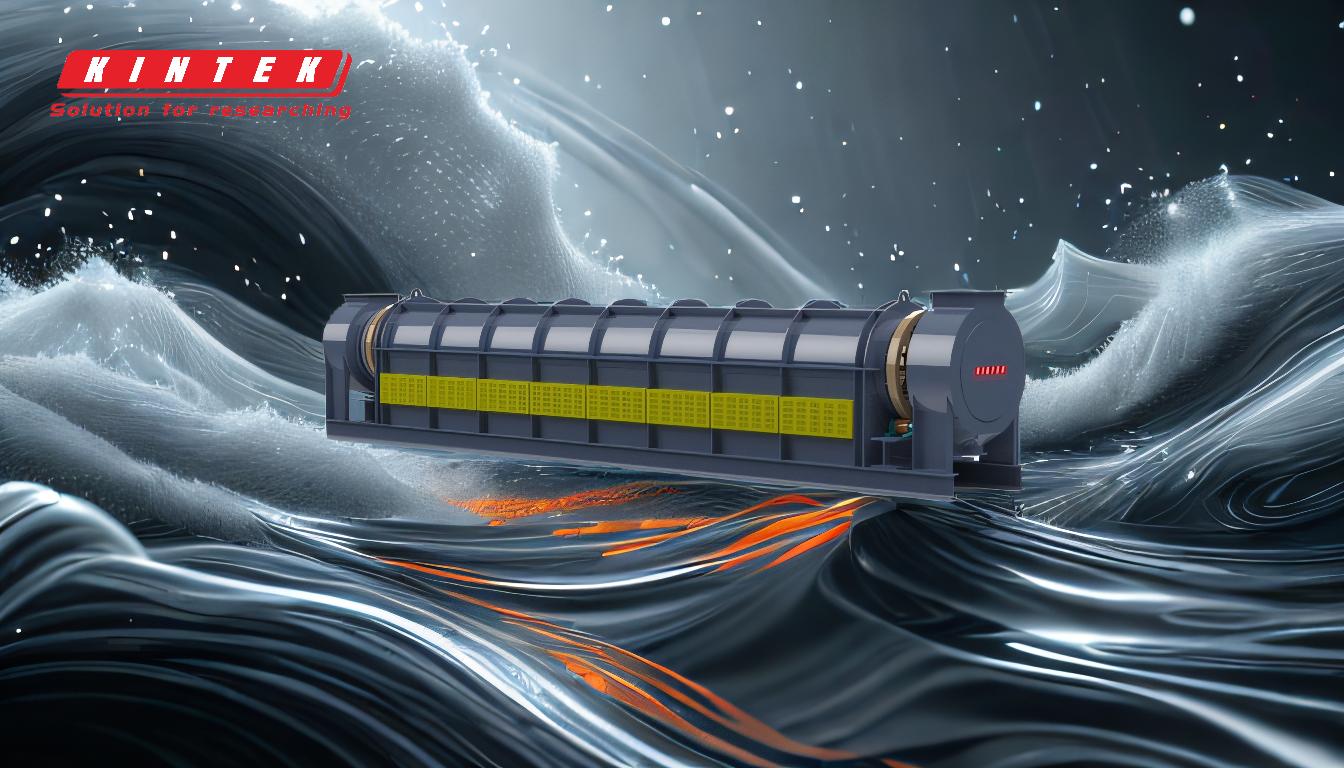
-
Efficient Heat and Mass Transfer:
- Fluidized beds excel in transferring heat and mass between the solid particles and the fluid medium. This is due to the high surface area of the particles and the turbulent mixing caused by the fluid flow.
- This efficiency is crucial in processes like combustion, where uniform temperature distribution is needed to maximize energy output and minimize emissions.
-
Enhanced Mixing and Uniformity:
- The fluid-like behavior of the bed ensures that particles are thoroughly mixed, leading to uniform temperature and composition throughout the system.
- This is particularly beneficial in chemical reactions, where consistent conditions are required to achieve desired reaction rates and product quality.
-
Versatility in Applications:
- Combustion: Fluidized beds are used in power plants for clean and efficient burning of coal, biomass, and waste materials. The technology reduces harmful emissions and improves fuel efficiency.
- Drying and Granulation: In industries like pharmaceuticals and food processing, fluidized beds are used to dry powders or granules and to create uniform particle sizes.
- Coating: Fluidized beds are employed to apply coatings to particles, such as in the production of controlled-release drug formulations or protective coatings on industrial materials.
- Chemical Synthesis: They facilitate reactions in industries like petrochemicals, where precise control over reaction conditions is essential.
-
Scalability and Process Control:
- Fluidized beds can be easily scaled up or down, making them suitable for both laboratory research and large-scale industrial production.
- Advanced control systems allow operators to adjust parameters like fluid velocity, temperature, and particle size, ensuring optimal performance and product quality.
-
Energy Efficiency and Environmental Benefits:
- The technology reduces energy consumption by improving heat transfer and reaction efficiency.
- In combustion applications, fluidized beds lower emissions of pollutants like nitrogen oxides and sulfur dioxide, contributing to cleaner industrial processes.
-
Challenges and Considerations:
- While fluidized beds offer numerous advantages, they also present challenges such as particle attrition (wear and tear of particles), erosion of equipment, and the need for precise fluid flow control.
- Proper design and maintenance are essential to mitigate these issues and ensure long-term operational efficiency.
In summary, the purpose of a fluidized bed is to enhance process efficiency, uniformity, and control across a wide range of industrial applications. Its ability to improve heat and mass transfer, coupled with its versatility and scalability, makes it a cornerstone technology in modern manufacturing and energy production.
Summary Table:
Key Feature | Description |
---|---|
Efficient Heat and Mass Transfer | High surface area and turbulent mixing ensure optimal energy and material flow. |
Enhanced Mixing and Uniformity | Fluid-like behavior ensures consistent temperature and composition. |
Versatility in Applications | Used in combustion, drying, granulation, coating, and chemical synthesis. |
Scalability and Process Control | Easily scalable for lab research or industrial production with precise control. |
Energy Efficiency | Reduces energy consumption and lowers emissions in combustion processes. |
Challenges | Particle attrition, equipment erosion, and precise fluid flow control required. |
Learn how fluidized beds can optimize your industrial processes—contact our experts today!