An inert atmosphere is primarily used to prevent unwanted chemical reactions, such as oxidation or decarburization, by replacing reactive gases like oxygen with non-reactive gases such as nitrogen, argon, or carbon dioxide. This controlled environment is essential in processes like heat treatment, sintering, and laboratory experiments, where exposure to oxygen or other reactive elements could damage materials or compromise results. Additionally, inert atmospheres enhance safety by reducing the risk of fire or explosions in industrial settings. The use of inert gases ensures cleaner, more stable, and precise outcomes in various applications, including automotive, aerospace, and petrochemical manufacturing.
Key Points Explained:
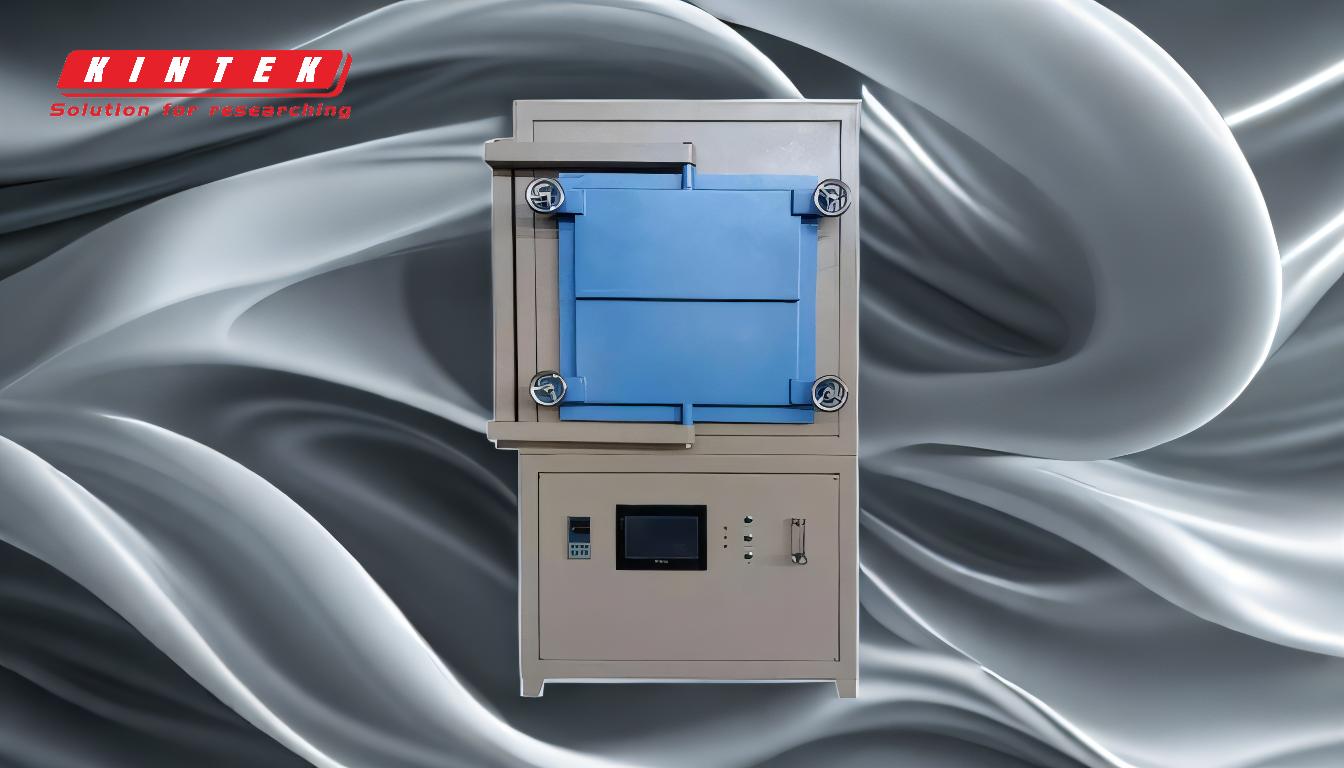
-
Prevention of Oxidation and Unwanted Chemical Reactions:
- Oxidation occurs when materials react with oxygen, leading to degradation or contamination.
- Inert gases like nitrogen, argon, or carbon dioxide displace oxygen, creating a non-reactive environment.
- This is critical in processes such as sintering, bright annealing, and carbonitriding, where maintaining material integrity is essential.
-
Protection of Sensitive Materials:
- Inert atmospheres are used in laboratories and industrial furnaces to protect samples or parts that are sensitive to oxygen exposure.
- For example, steel components can be protected from reacting with carbon, oxygen, or nitrogen during heat treatment, ensuring high-quality results.
-
Enhanced Safety by Reducing Fire and Explosion Risks:
- Replacing combustible or reactive gases with inert gases minimizes the risk of fire or explosions.
- This is particularly important in industries like petrochemical manufacturing, where the accumulation of flammable gases can be hazardous.
-
Improved Process Control and Quality:
- Inert atmosphere furnaces feature precision temperature controls and energy-efficient insulation, ensuring consistent and high-quality outcomes.
- Processes like hot isostatic pressing (HIP) and vacuum operations rely on inert atmospheres to achieve clean, controlled environments.
-
Applications Across Industries:
- Inert atmospheres are widely used in industries such as automotive, aerospace, and petrochemical manufacturing.
- They are essential for processes like sintering, bright annealing, and carbonitriding, which require highly controlled environments to produce reliable and durable components.
-
Scientific Basis for Using Inert Gases:
- Different gases have varying reactivity and oxidation potentials. Inert gases are chosen for their low reactivity, ensuring stability even under changing conditions.
- This scientific principle underpins the effectiveness of inert atmospheres in preventing unwanted reactions and maintaining material properties.
-
Cost and Energy Efficiency:
- Modern inert atmosphere furnaces are designed with energy-efficient insulation and microprocessor-based controls, optimizing cost savings while maintaining performance.
- This makes inert atmospheres a practical and economical choice for industrial and laboratory applications.
By understanding these key points, purchasers of equipment and consumables can make informed decisions about the use of inert atmospheres in their processes, ensuring safety, quality, and efficiency.
Summary Table:
Key Benefit | Description |
---|---|
Prevents Oxidation | Replaces reactive gases like oxygen with non-reactive gases (e.g., nitrogen). |
Protects Sensitive Materials | Shields materials from oxygen exposure during heat treatment or experiments. |
Enhances Safety | Reduces fire and explosion risks by minimizing flammable gas accumulation. |
Improves Process Control | Ensures precise temperature control and consistent, high-quality outcomes. |
Wide Industry Applications | Used in automotive, aerospace, and petrochemical manufacturing processes. |
Cost and Energy Efficient | Features energy-efficient insulation and microprocessor-based controls. |
Ready to optimize your processes with inert atmospheres? Contact us today for expert guidance!