PVD (Physical Vapor Deposition) is a coating technique used to deposit thin films of material onto a substrate through physical processes, such as vaporization and condensation, typically performed in a vacuum environment. Unlike chemical vapor deposition system, which relies on chemical reactions, PVD involves the physical transformation of a solid material into a vapor, which then condenses onto the substrate. The process is widely used for creating durable, high-quality coatings with excellent adhesion and uniformity. PVD methods include vacuum evaporation, sputtering, arc plasma plating, and ion plating, each offering unique advantages depending on the application. While PVD is generally more complex and costly than some other deposition methods, it provides superior film quality and is suitable for applications requiring precise control over coating properties.
Key Points Explained:
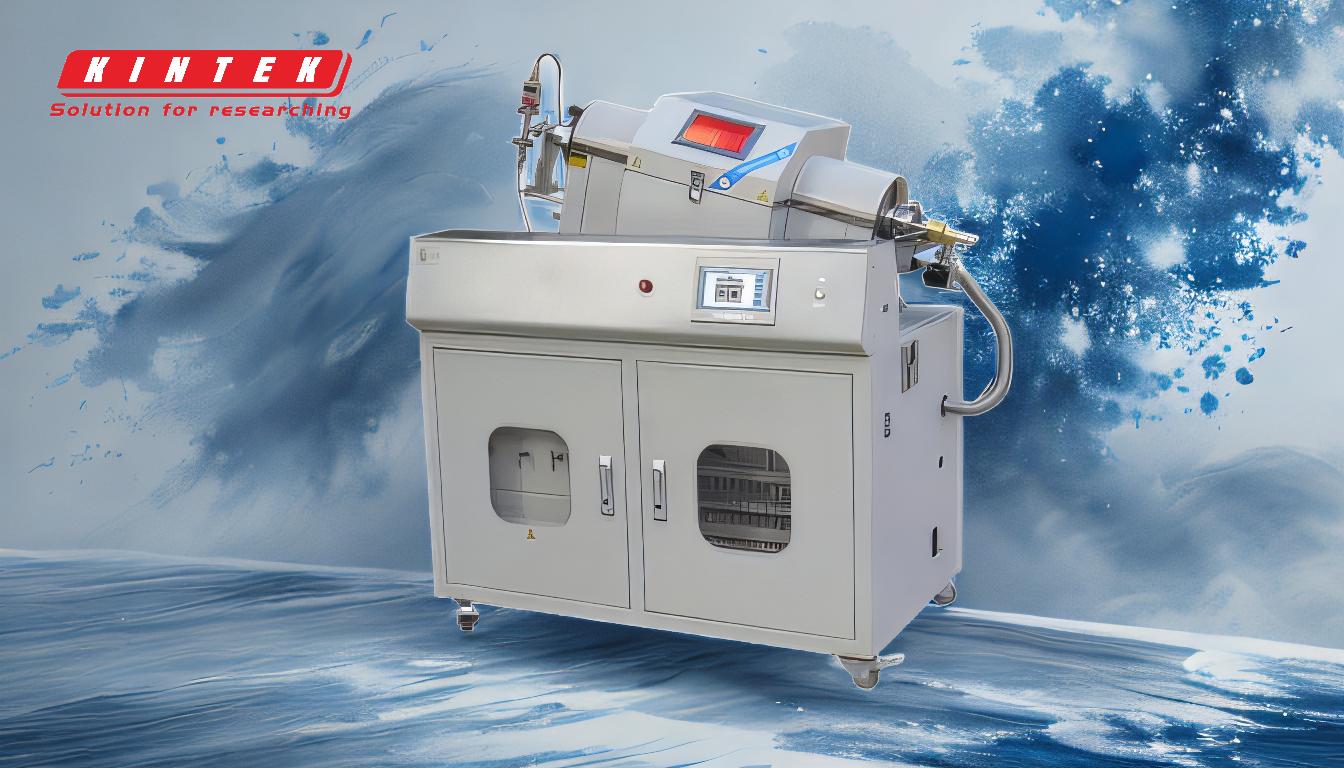
-
Definition and Process of PVD:
- PVD is a physical process where a solid material is vaporized in a vacuum and then deposited onto a substrate as a thin film.
- The process typically involves:
- Cleaning the substrate to ensure proper adhesion.
- Creating a vacuum environment to minimize contamination.
- Vaporizing the target material using methods like sputtering or evaporation.
- Depositing the vaporized material onto the substrate atom by atom.
- This method ensures high-quality, uniform coatings with excellent durability and adhesion.
-
Comparison with CVD:
- PVD differs from chemical vapor deposition system in that it relies on physical processes rather than chemical reactions.
- CVD involves the interaction of gases with the substrate, forming a solid coating through chemical reactions, often at high temperatures.
- PVD, on the other hand, uses line-of-sight deposition, where material is directly transferred to the substrate without chemical interaction, resulting in fewer impurities and better control over film properties.
-
Main PVD Methods:
- Vacuum Evaporation: The target material is heated to its vaporization point in a vacuum, and the vapor condenses onto the substrate.
- Sputtering Deposition: High-energy ions bombard the target material, ejecting atoms that deposit onto the substrate.
- Arc Plasma Plating: An electric arc vaporizes the target material, creating a plasma that deposits onto the substrate.
- Ion Plating: Combines sputtering and evaporation, with ionized particles enhancing film adhesion and density.
-
Advantages of PVD:
- Produces high-quality, uniform coatings with excellent adhesion and durability.
- Can be performed at lower temperatures compared to CVD, reducing the risk of substrate damage.
- Does not produce corrosive byproducts, making it environmentally friendly.
- Suitable for a wide range of materials, including metals, ceramics, and composites.
-
Applications of PVD:
- Widely used in industries such as aerospace, automotive, electronics, and medical devices.
- Common applications include wear-resistant coatings, decorative finishes, and functional coatings for optical and electronic components.
- PVD is particularly valued for its ability to create thin, precise coatings with controlled properties.
-
Challenges and Considerations:
- PVD is generally more complex and costly than other deposition methods, such as evaporation.
- The process requires specialized equipment and a controlled vacuum environment.
- Deposition rates are typically lower than those of CVD, although methods like EBPVD (Electron Beam Physical Vapor Deposition) offer higher rates.
In summary, PVD is a versatile and precise deposition method that offers significant advantages in terms of coating quality and control. While it may be more complex and expensive than some alternatives, its ability to produce durable, high-performance coatings makes it a preferred choice for many advanced applications.
Summary Table:
Aspect | Details |
---|---|
Definition | Physical process vaporizing solid material in a vacuum to deposit thin films. |
Key Methods | Vacuum Evaporation, Sputtering, Arc Plasma Plating, Ion Plating. |
Advantages | High-quality, uniform coatings; excellent adhesion; environmentally friendly. |
Applications | Aerospace, automotive, electronics, medical devices. |
Challenges | Higher complexity and cost; requires specialized vacuum equipment. |
Learn how PVD can enhance your coating processes—contact our experts today!