The pyrolysis method for biochar involves heating biomass in an oxygen-free or low-oxygen environment to break it down into biochar, bio-oil, and syngas. This process typically occurs at temperatures between 200°C and 900°C, depending on the type of pyrolysis (slow, fast, or intermediate). Slow pyrolysis, which is commonly used for biochar production, operates at lower temperatures (around 400°C) with longer residence times, resulting in higher biochar yields. The biomass undergoes pre-treatment (drying and grinding), followed by controlled heating in a reactor. The process energy can be self-sustained by combusting the gaseous byproducts. Biochar settles at the bottom of the reactor, while bio-oil and syngas are collected for further use.
Key Points Explained:
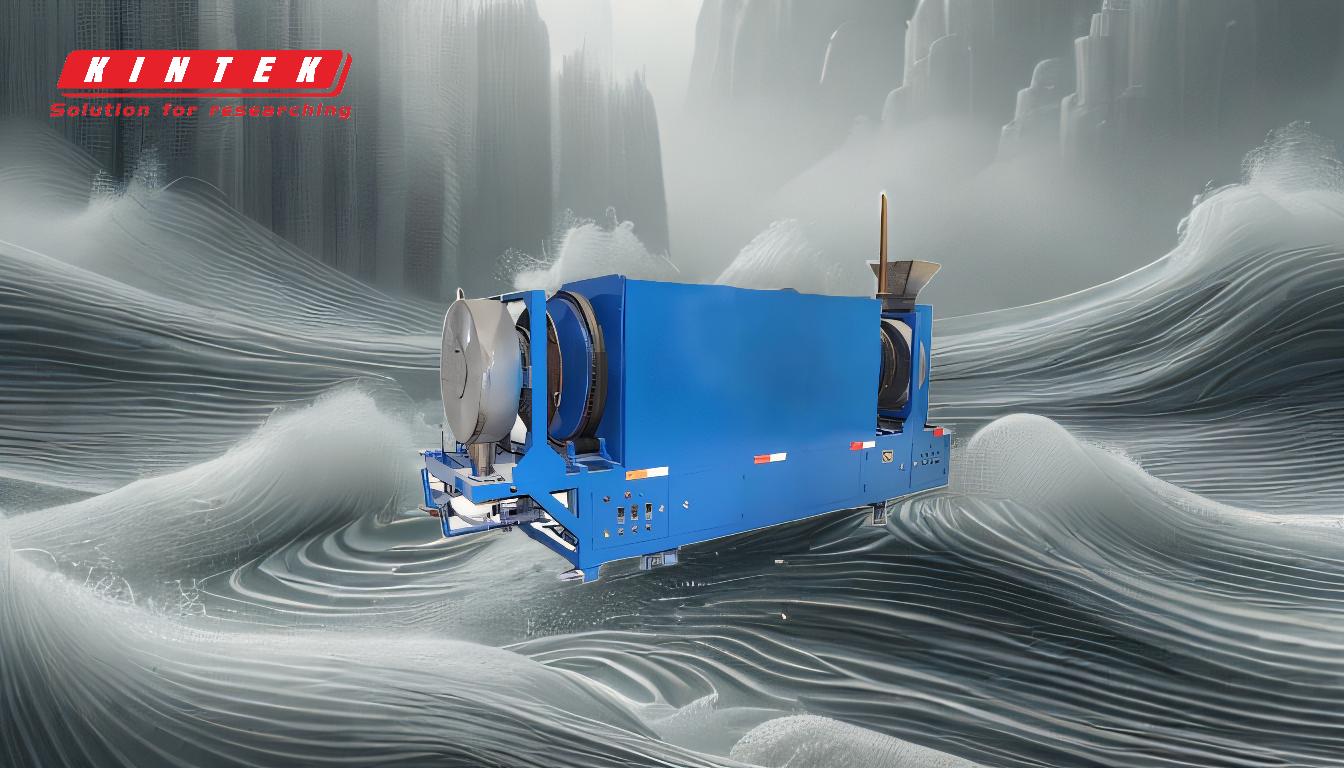
-
Definition and Purpose of Pyrolysis for Biochar:
- Pyrolysis is a thermal decomposition process that converts biomass into biochar, bio-oil, and syngas in the absence of oxygen.
- Biochar is a carbon-rich solid material used for soil amendment, carbon sequestration, and other applications.
-
Types of Pyrolysis:
- Slow Pyrolysis: Operates at lower temperatures (around 400°C) with longer residence times (several hours). It maximizes biochar yield and is the most common method for biochar production.
- Fast Pyrolysis: Uses higher temperatures (500°C–700°C) and shorter residence times (seconds to minutes). It produces more bio-oil and less biochar.
- Gasification: Operates at even higher temperatures (above 700°C) and produces primarily syngas.
-
Steps in the Pyrolysis Process:
- Pre-Treatment: Biomass is dried and mechanically comminuted (crushed or ground) to ensure uniform heating and efficient decomposition.
- Pyrolysis: The biomass is heated in a reactor under controlled conditions. The absence of oxygen prevents combustion and allows thermal decomposition.
- Separation: The resulting products (biochar, bio-oil, and syngas) are separated. Biochar settles at the bottom, while bio-oil and syngas are condensed and collected.
- Cooling and Cleaning: Biochar is cooled, and exhaust gases are de-dusted to reduce harmful emissions.
-
Key Parameters in Pyrolysis:
- Temperature: Determines the yield and quality of biochar. Lower temperatures favor biochar production, while higher temperatures increase bio-oil and syngas yields.
- Residence Time: Longer residence times in slow pyrolysis enhance biochar formation.
- Heating Rate: Slow heating rates are typical for slow pyrolysis, while fast pyrolysis requires rapid heating.
-
Energy Efficiency and Sustainability:
- The energy required for pyrolysis can be partially or fully covered by combusting the syngas produced during the process, making it energy-efficient.
- Biochar production contributes to carbon sequestration, as the carbon in biochar is stable and resistant to decomposition.
-
Applications of Biochar:
- Soil Amendment: Improves soil fertility, water retention, and microbial activity.
- Carbon Sequestration: Reduces greenhouse gas emissions by storing carbon in a stable form.
- Waste Management: Converts agricultural and forestry waste into valuable products.
-
Industrial Pyrolysis Systems:
- Industrial-scale pyrolysis involves feeding dry biomass into a reactor with low oxygen levels, supplying heat via a combustion chamber, and separating the products using cyclones and quenching systems.
- Non-condensable syngas is often recycled to the combustion chamber to sustain the process.
By understanding these key points, a purchaser of pyrolysis equipment or consumables can make informed decisions about the type of system and parameters needed for their specific biochar production goals.
Summary Table:
Aspect | Details |
---|---|
Process | Thermal decomposition of biomass in an oxygen-free environment. |
Temperature Range | 200°C–900°C, depending on pyrolysis type. |
Main Products | Biochar, bio-oil, and syngas. |
Types of Pyrolysis | Slow (400°C, high biochar yield), Fast (500°C–700°C, more bio-oil), Gasification (above 700°C, syngas). |
Key Steps | Pre-treatment, pyrolysis, separation, cooling, and cleaning. |
Applications | Soil amendment, carbon sequestration, waste management. |
Energy Efficiency | Self-sustained by combusting syngas; contributes to carbon sequestration. |
Ready to optimize your biochar production? Contact our experts today for tailored solutions!