The range of a TF tube furnace, specifically a high-temperature tube furnace, typically spans from room temperature up to 1700°C or even 1800°C, depending on the model and configuration. These furnaces are designed for high-temperature applications such as sintering, annealing, and heat treatment, and are widely used in research labs, production facilities, and technical ceramics manufacturing. The horizontal orientation of tube furnaces allows for continuous processing of long samples, and they are equipped with heating elements like resistance wires or graphite elements to achieve uniform high temperatures. Alumina tubes are commonly used for high-temperature operations, though they must be carefully selected to avoid thermal shock.
Key Points Explained:
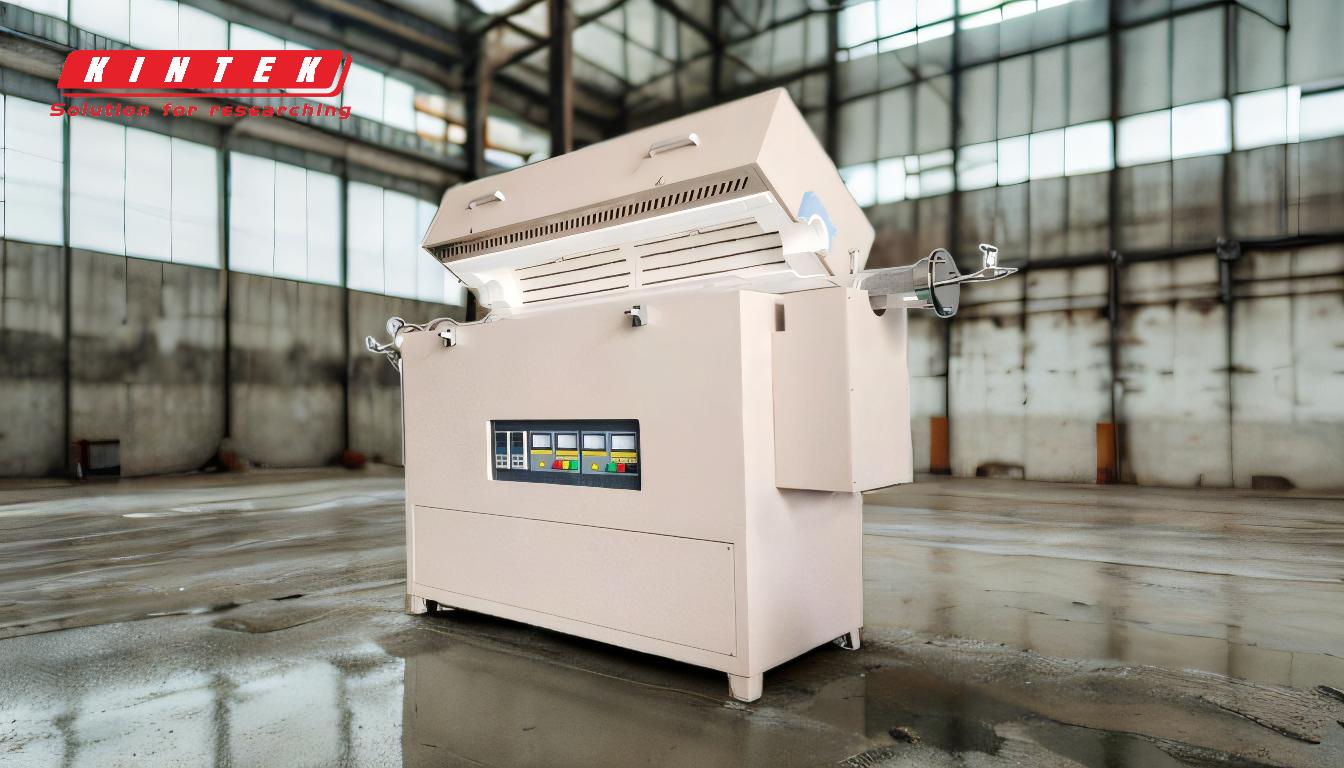
-
Temperature Range:
- The operating temperature of a high-temperature tube furnace typically ranges from room temperature up to 1700°C or 1800°C, depending on the specific model and heating elements used. This makes them suitable for demanding applications like sintering, annealing, and heat treatment. For more details, see high temperature tube furnace.
-
Applications:
- These furnaces are used in a variety of settings, including:
- Dental labs
- University and research labs
- Production facilities
- Common processes include:
- Annealing
- Sintering
- Melting
- Binder burnout
- Curing
- Metal joining
- These furnaces are used in a variety of settings, including:
-
Design and Orientation:
- Tube furnaces are typically designed with a horizontal orientation, which is ideal for processing long samples such as wires or rods. The horizontal design allows for continuous processing and uniform heat distribution.
-
Heating Elements:
- High-temperature tube furnaces are equipped with advanced heating elements, such as:
- Resistance wires
- Graphite elements
- These elements ensure uniform heating and can withstand extreme temperatures.
- High-temperature tube furnaces are equipped with advanced heating elements, such as:
-
Process Tubes:
- The furnace tubes are usually made of alumina for high-temperature operations. Key considerations include:
- Tube diameter: Smaller diameters perform better under thermal stress.
- Thermal shock resistance: Alumina tubes are prone to thermal shock, so careful handling is required.
- The furnace tubes are usually made of alumina for high-temperature operations. Key considerations include:
-
Uniformity and Reliability:
- High-temperature tube furnaces are designed with heating elements on all sides of the chamber to ensure temperature uniformity. This is critical for processes like fusion, firing, and testing.
- These furnaces have a proven track record of reliability in both lab and production environments, particularly in the manufacturing of technical ceramics.
-
Sample Handling:
- Samples are typically placed inside the tube using ceramic or metal boats and a long push rod. This setup allows for precise positioning and handling of materials during high-temperature processes.
By understanding these key points, purchasers and users can make informed decisions about selecting and operating a high-temperature tube furnace for their specific needs.
Summary Table:
Feature | Details |
---|---|
Temperature Range | Room temperature up to 1700°C or 1800°C, depending on model and configuration. |
Applications | Sintering, annealing, heat treatment, melting, binder burnout, curing, and metal joining. |
Design | Horizontal orientation for continuous processing of long samples. |
Heating Elements | Resistance wires or graphite elements for uniform high-temperature heating. |
Process Tubes | Alumina tubes for high-temperature operations; smaller diameters perform better. |
Uniformity & Reliability | Heating elements on all sides ensure temperature uniformity and reliability. |
Sample Handling | Ceramic or metal boats with a long push rod for precise material handling. |
Ready to explore high-temperature tube furnaces for your lab or production needs? Contact us today to find the perfect solution!