Reactive magnetron sputtering is a specialized physical vapor deposition (PVD) technique used to deposit compound thin films, such as oxides or nitrides, onto a substrate. It combines the principles of magnetron sputtering with the introduction of reactive gases, such as oxygen or nitrogen, into the vacuum chamber. This method allows for the formation of compound films by reacting the ejected target material atoms with the reactive gas. The process is highly efficient due to the use of magnetic fields to confine electrons and enhance plasma density, but it can exhibit instability due to target poisoning and hysteresis effects. Reactive magnetron sputtering is widely used in industries requiring precise thin-film coatings, such as semiconductors, optics, and protective coatings.
Key Points Explained:
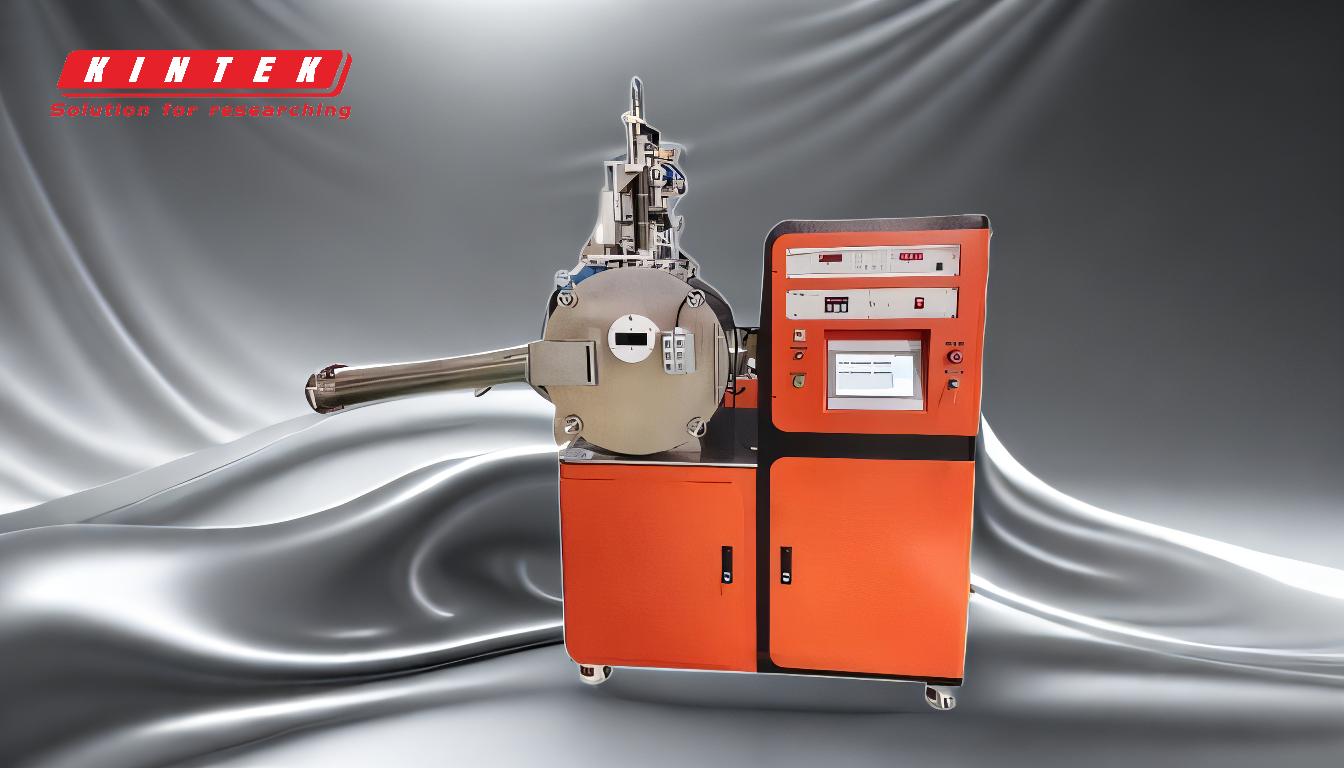
-
Definition and Purpose of Reactive Magnetron Sputtering:
- Reactive magnetron sputtering is a PVD method used to deposit compound thin films (e.g., oxides, nitrides) onto substrates.
- It involves introducing reactive gases (e.g., oxygen, nitrogen) into the vacuum chamber during the sputtering process.
- The reactive gas reacts with the ejected target material atoms to form compound films on the substrate.
-
Core Principles of Magnetron Sputtering:
- Magnetron sputtering uses a high vacuum chamber and a low-pressure gas (usually argon) to create a plasma.
- A high negative voltage is applied between the cathode (target) and anode, ionizing the argon gas and creating a plasma.
- Positive argon ions collide with the negatively charged target, ejecting target atoms in a line-of-sight distribution.
- These ejected atoms condense on the substrate to form a thin film.
-
Role of Magnetic Fields:
- Magnetic fields are used to confine electrons near the target surface, increasing plasma density and deposition rates.
- The magnetic field traps electrons, enhancing ionization efficiency and reducing substrate damage from ion bombardment.
-
Introduction of Reactive Gases:
- Reactive gases like oxygen or nitrogen are introduced into the chamber during the sputtering process.
- These gases react with the ejected target atoms to form compound films (e.g., metal oxides or nitrides) on the substrate.
- The reaction occurs both in the plasma and on the substrate surface.
-
Challenges and Instability:
- Reactive magnetron sputtering exhibits hysteresis, meaning the system's response to changes in operating parameters (e.g., gas flow rate, power) is non-linear.
- Target poisoning occurs when the reactive gas reacts with the target surface, forming a compound layer that reduces sputtering efficiency.
- These factors make the process inherently unstable and require careful control of parameters.
-
Advantages of Reactive Magnetron Sputtering:
- High deposition rates due to the enhanced plasma density from magnetic confinement.
- Ability to deposit high-quality compound films with precise stoichiometry.
- Versatility in depositing a wide range of materials, including oxides, nitrides, and other compounds.
-
Applications:
- Semiconductor manufacturing: Deposition of dielectric and conductive layers.
- Optics: Creation of anti-reflective and protective coatings.
- Protective coatings: Hard coatings for tools and wear-resistant surfaces.
- Energy: Thin-film solar cells and battery materials.
-
Process Optimization:
- Control of reactive gas flow rates to balance film composition and deposition rate.
- Monitoring and adjusting power levels to prevent target poisoning.
- Use of feedback systems to manage hysteresis and maintain process stability.
By understanding these key points, a purchaser of equipment or consumables can better evaluate the suitability of reactive magnetron sputtering for their specific application and ensure optimal process control for high-quality thin-film deposition.
Summary Table:
Aspect | Details |
---|---|
Definition | A PVD technique for depositing compound thin films (e.g., oxides, nitrides). |
Key Principles | Combines magnetron sputtering with reactive gases (e.g., oxygen, nitrogen). |
Role of Magnetic Fields | Confines electrons, enhances plasma density, and increases deposition rates. |
Challenges | Instability due to target poisoning and hysteresis effects. |
Advantages | High deposition rates, precise stoichiometry, and material versatility. |
Applications | Semiconductors, optics, protective coatings, and energy solutions. |
Process Optimization | Control of gas flow rates, power levels, and feedback systems. |
Discover how reactive magnetron sputtering can enhance your thin-film applications—contact our experts today!