Nitrogen plays a critical role in the annealing process, primarily by creating an inert atmosphere that prevents oxidation and other undesirable chemical reactions during heat treatment. It is widely used in metalworking to reduce hardness, increase ductility, and improve the overall quality of metals. By displacing oxygen and other reactive gases, nitrogen ensures a stable environment, which is essential for processes like bright annealing, neutral hardening, and tempering. Its inert nature makes it ideal for protecting metals from oxidation, decarburization, and contamination, while also enhancing the efficiency and safety of the annealing process. Nitrogen annealing is particularly beneficial for tools, components, and non-ferrous metals, ensuring they are less prone to cracking and easier to shape.
Key Points Explained:
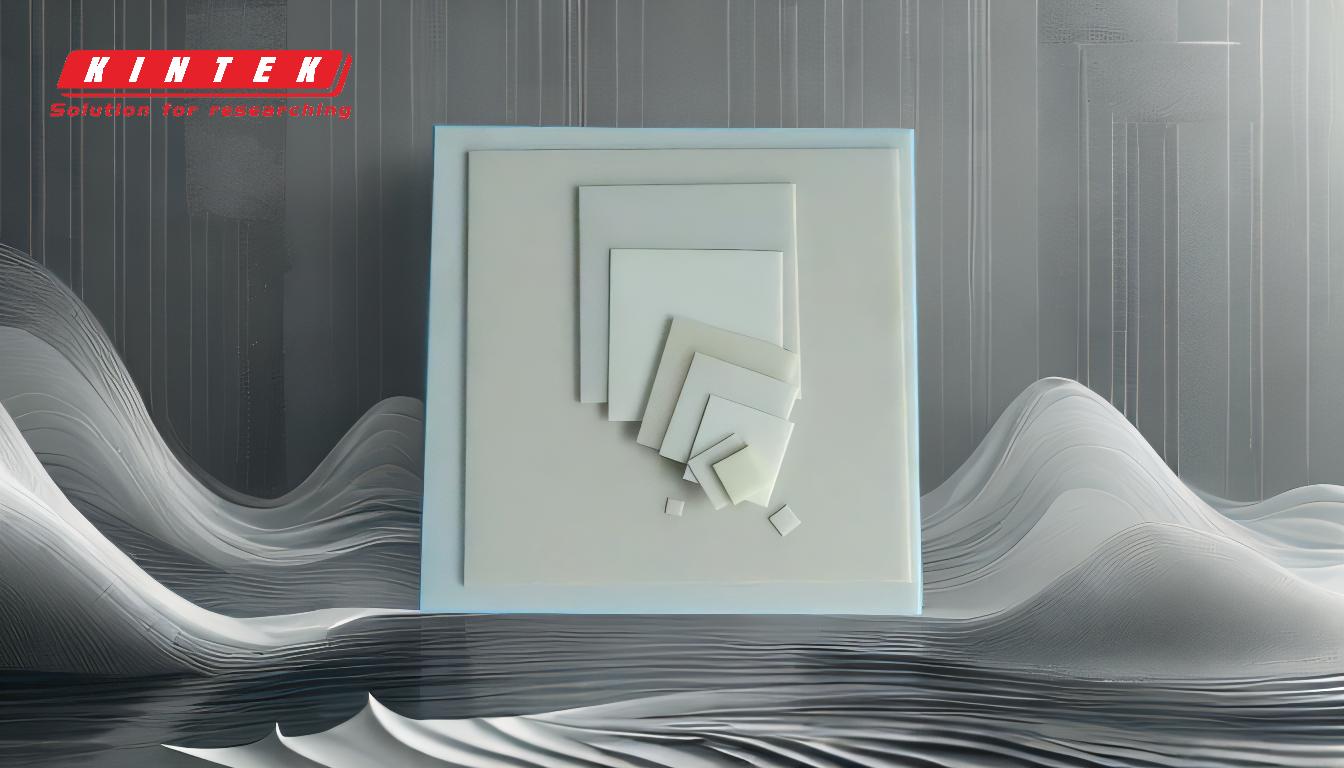
-
Prevention of Oxidation:
- Nitrogen is an inert gas, meaning it does not readily react with other substances. During annealing, it creates an oxygen-free environment, preventing the metal from oxidizing. Oxidation can degrade the surface quality and mechanical properties of the metal, making nitrogen essential for maintaining material integrity.
-
Creation of an Inert Atmosphere:
- The use of nitrogen ensures that the furnace environment remains chemically neutral. This is particularly important for processes like bright annealing, where the goal is to achieve a clean, oxide-free surface. By displacing oxygen and other reactive gases, nitrogen minimizes the risk of unwanted chemical reactions.
-
Enhanced Heat Treatment Efficiency:
- Nitrogen improves the efficiency of heat treatment processes by providing a stable and controlled environment. Its inert nature allows for uniform heating and cooling, which is critical for achieving consistent material properties. This is especially important for precision components and tools.
-
Decarburization Prevention:
- Decarburization, the loss of carbon from the surface of steel, can weaken the material. Nitrogen helps prevent this by maintaining a neutral atmosphere, ensuring that the carbon content of the metal remains intact during annealing.
-
Safety and Hazard Mitigation:
- Nitrogen is used to displace hazardous gases in the furnace atmosphere before annealing begins. This reduces the risk of explosions or unstable conditions, making the process safer for operators and equipment.
-
Applications in Various Industries:
- Nitrogen annealing is widely used in the production of tools, springs, bearings, and non-ferrous metals like copper and aluminum. It is also employed in specialized processes such as nitriding, carbonitriding, and powder metallurgy, where maintaining a controlled atmosphere is crucial.
-
Improved Material Properties:
- By preventing oxidation and decarburization, nitrogen annealing helps produce metals that are more ductile, less brittle, and easier to work with. This is particularly beneficial for components that require high precision and durability.
-
High Purity Requirements:
- The effectiveness of nitrogen in annealing depends on its purity. High-purity nitrogen (99.99% or higher) is often required to ensure optimal results. Advanced systems can provide nitrogen with purity levels up to 99.9995%, meeting the stringent demands of modern metalworking processes.
-
Versatility in Metalworking:
- Nitrogen annealing is not limited to steel but is also used for non-ferrous metals and specialized alloys. Its versatility makes it a valuable tool in a wide range of industrial applications, from automotive manufacturing to electronics.
-
Cost-Effectiveness:
- While nitrogen is a critical component in annealing, it is also cost-effective compared to other protective gases. Its widespread availability and relatively low cost make it a practical choice for large-scale industrial processes.
In summary, nitrogen is indispensable in the annealing process due to its ability to create a stable, inert environment that prevents oxidation, decarburization, and other chemical reactions. Its use enhances the efficiency, safety, and quality of heat treatment processes, making it a key component in modern metalworking and manufacturing industries.
Summary Table:
Key Benefits of Nitrogen in Annealing | Details |
---|---|
Prevents Oxidation | Creates an oxygen-free environment, protecting metal surfaces. |
Inert Atmosphere | Ensures a chemically neutral environment for bright annealing. |
Efficiency in Heat Treatment | Provides uniform heating and cooling for consistent results. |
Prevents Decarburization | Maintains carbon content in steel, preserving strength. |
Safety Enhancement | Displaces hazardous gases, reducing explosion risks. |
Versatile Applications | Used in tools, springs, bearings, and non-ferrous metals. |
High Purity Requirements | Requires 99.99%+ purity for optimal performance. |
Cost-Effective | Affordable and widely available for industrial use. |
Ready to optimize your annealing process with nitrogen? Contact our experts today to learn more!